LPCVD (Low-Pressure Chemical Vapor Deposition) systems operate within a specific pressure range to ensure optimal deposition of thin films on substrates. The pressure range for LPCVD systems is typically between 0.1 to 10 Torr, which is considered a medium vacuum application. This pressure range is critical for achieving uniform film deposition, minimizing contamination, and maintaining process control. Additionally, LPCVD systems often operate at high temperatures, ranging from 425 to 900°C, depending on the material being deposited. The combination of low pressure and high temperature ensures precise control over the chemical reactions and film properties.
Key Points Explained:
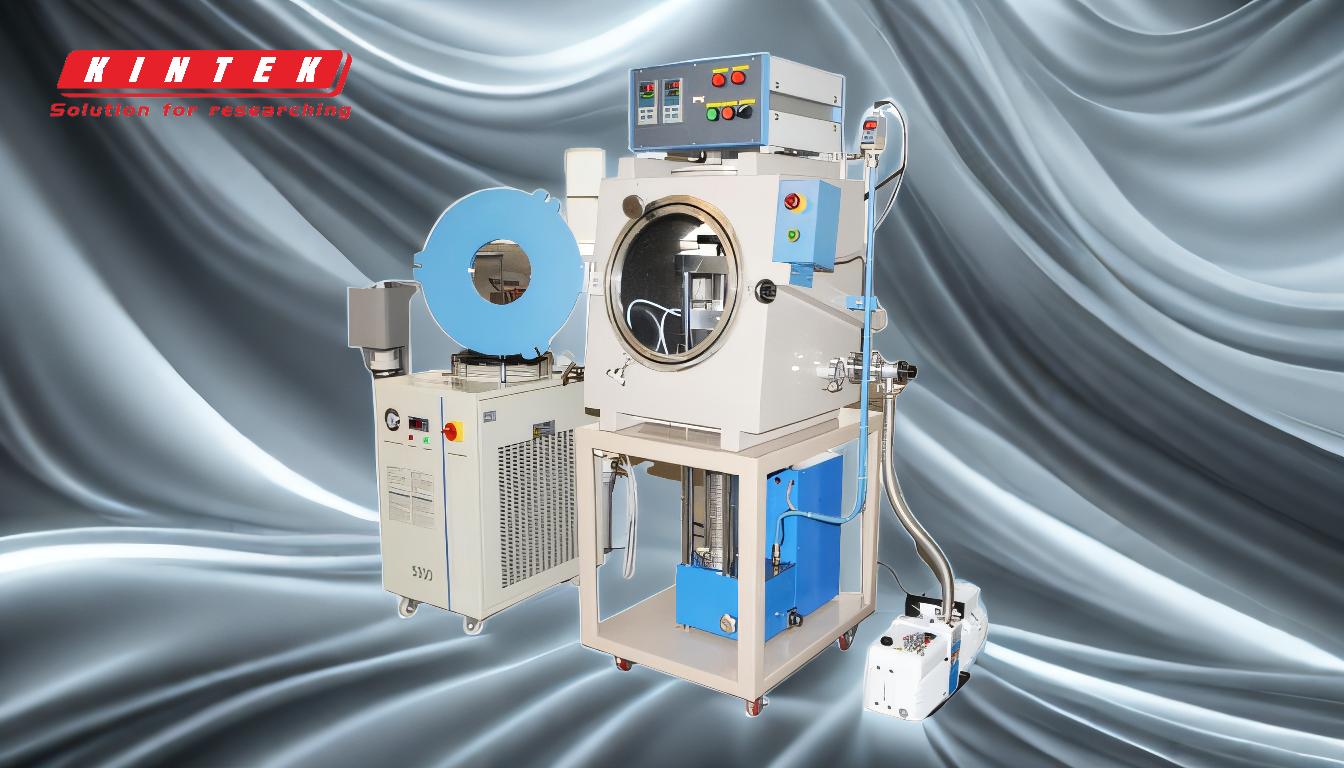
-
Pressure Range of LPCVD Systems:
- LPCVD systems operate in a pressure range of 0.1 to 10 Torr.
- This range is classified as a medium vacuum, which is essential for controlling the deposition process and ensuring uniform film growth.
- The low-pressure environment reduces gas-phase reactions, leading to better film quality and fewer defects.
-
Comparison with Other CVD Processes:
- PECVD (Plasma-Enhanced Chemical Vapor Deposition): Operates at pressures between 10 to 100 Pa (approximately 0.075 to 0.75 Torr) and lower temperatures (200°C to 400°C).
- Atmospheric Pressure CVD (APCVD): Operates at or near atmospheric pressure, which is significantly higher than LPCVD.
- LPCVD's medium vacuum range strikes a balance between the high vacuum of PECVD and the atmospheric pressure of APCVD, making it suitable for a wide range of applications.
-
Temperature Range in LPCVD:
- LPCVD systems typically operate at temperatures between 425°C and 900°C, depending on the material being deposited.
- For example, silicon dioxide deposition often occurs at around 650°C.
- The high temperatures facilitate the chemical reactions necessary for film formation, while the low pressure ensures controlled and uniform deposition.
-
Advantages of LPCVD:
- Uniformity: The low-pressure environment allows for uniform film deposition across large substrates or batches.
- Control: Precise control over pressure and temperature leads to consistent film properties and reduced defects.
- Versatility: LPCVD can deposit a wide range of materials, including silicon dioxide, silicon nitride, and polysilicon.
-
System Configurations:
- LPCVD systems can be configured in various ways, including:
- Tubular Hot-Wall Reactors: Commonly used for batch processing.
- Vertical Flow Batch Reactors: Suitable for high-throughput applications.
- Single-Wafer Cluster Tools: Preferred in modern fabs for their advantages in wafer handling, particle control, and process integration.
- LPCVD systems can be configured in various ways, including:
-
Applications of LPCVD:
- LPCVD is widely used in semiconductor manufacturing for depositing thin films in integrated circuits, MEMS (Micro-Electro-Mechanical Systems), and other microelectronic devices.
- Its ability to produce high-quality, uniform films makes it indispensable in advanced fabrication processes.
By understanding the pressure and temperature ranges of LPCVD systems, equipment and consumable purchasers can make informed decisions about the suitability of LPCVD for their specific applications. The medium vacuum pressure range and high-temperature operation ensure precise and reliable deposition, making LPCVD a cornerstone of modern semiconductor manufacturing.
Summary Table:
Parameter | LPCVD Range |
---|---|
Pressure Range | 0.1 to 10 Torr |
Temperature Range | 425°C to 900°C |
Vacuum Type | Medium Vacuum |
Key Advantages | Uniformity, Control, Versatility |
Common Applications | Semiconductors, MEMS, Microelectronics |
Discover how LPCVD systems can enhance your semiconductor processes—contact us today for expert guidance!