The principle of an arc melting furnace revolves around generating high temperatures through an electric arc to melt metals. This is achieved by creating an arc between two electrodes, which produces intense heat. The process involves charging the electrode, a meltdown phase where the metal is liquefied, and refining to achieve the desired metal properties. The arc can be generated using either high tension (H.T.) or low tension (L.T.) methods, depending on the application. This method is widely used in metallurgy for melting scrap metal, refining alloys, and producing high-quality metals.
Key Points Explained:
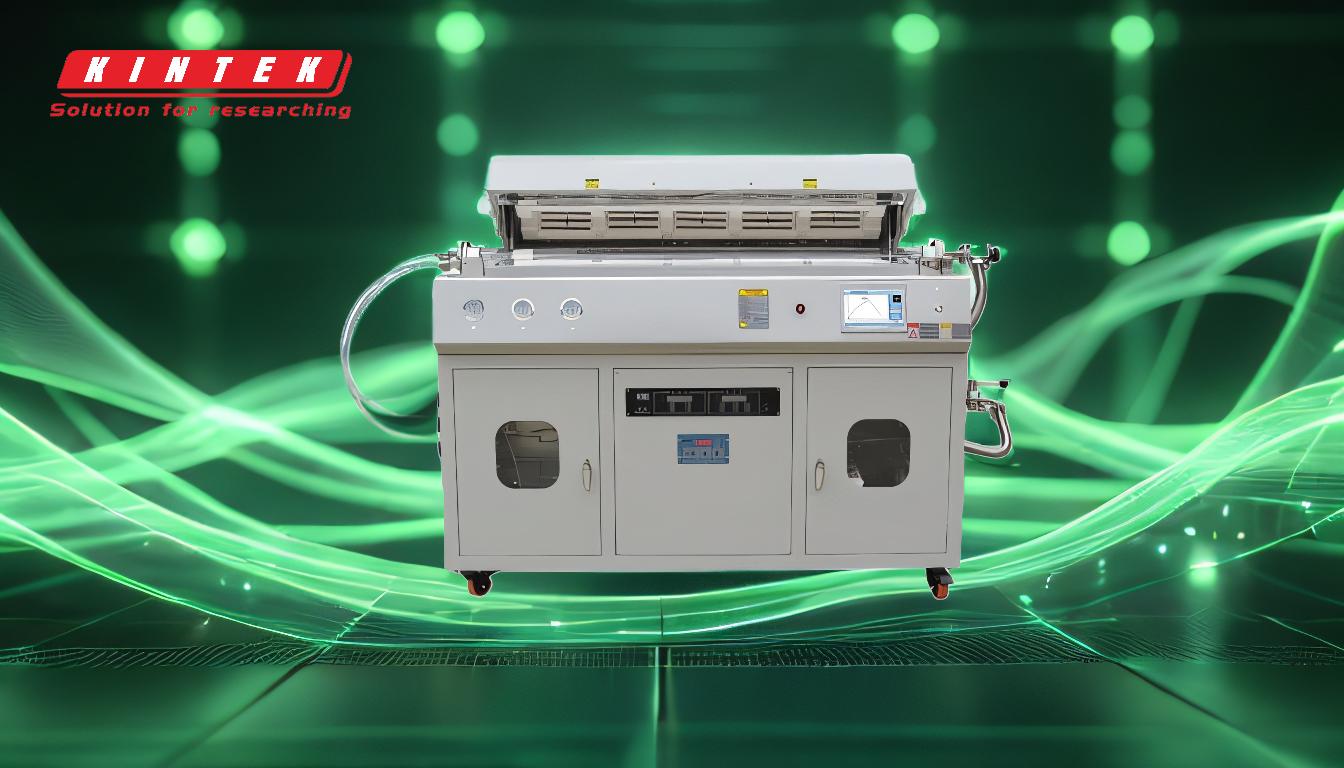
-
Electric Arc Formation:
- The core principle of an arc melting furnace is the creation of an electric arc between two electrodes. This arc is a high-temperature plasma discharge that generates intense heat, sufficient to melt metals.
- The arc can be initiated using either high tension (H.T.) or low tension (L.T.) methods. H.T. involves higher voltage to create the arc, while L.T. uses lower voltage but higher current.
-
Heat Generation and Melting:
- The heat produced by the electric arc is used to melt the metal. The temperature in the arc can reach up to 3,000°C (5,432°F), which is more than enough to melt most metals.
- The metal is typically charged into the furnace, and the arc is directed onto the metal to initiate the melting process.
-
Meltdown and Refining Phases:
- The process begins with the meltdown phase, where the metal is heated until it liquefies. During this phase, impurities may rise to the surface and form slag.
- Refining follows, where additives like burnt lime and spar are introduced to remove impurities and improve the metal's quality. The slag is then removed, leaving behind the refined metal.
-
Applications of Arc Melting Furnaces:
- Arc melting furnaces are extensively used in metallurgy for melting scrap metal, refining alloys, and producing high-quality metals. They are particularly useful in industries that require precise control over the melting process and the composition of the final product.
-
Comparison with Induction Melting Furnaces:
- Unlike induction melting furnaces, which use electromagnetic induction to generate heat, arc melting furnaces rely on the direct heat from the electric arc. This makes arc furnaces more suitable for applications requiring higher temperatures and larger-scale melting.
-
Advantages of Arc Melting Furnaces:
- High Efficiency: Arc furnaces can reach very high temperatures quickly, making them efficient for melting metals.
- Flexibility: They can handle a wide range of metals and alloys, including those with high melting points.
- Environmental Benefits: Modern arc furnaces are designed to be more energy-efficient and produce fewer emissions compared to traditional melting methods.
In summary, the principle of an arc melting furnace is centered around the generation of an electric arc to produce the high temperatures needed for melting metals. This method is highly efficient and versatile, making it a cornerstone in modern metallurgical processes.
Summary Table:
Key Aspect | Details |
---|---|
Electric Arc Formation | Created between two electrodes using high tension (H.T.) or low tension (L.T.). |
Heat Generation | Arc temperature reaches up to 3,000°C (5,432°F), sufficient to melt metals. |
Meltdown & Refining | Metal is liquefied, impurities form slag, and refining improves metal quality. |
Applications | Melting scrap metal, refining alloys, and producing high-quality metals. |
Advantages | High efficiency, flexibility, and environmental benefits. |
Discover how arc melting furnaces can revolutionize your metallurgical processes—contact our experts today!