An induction furnace operates on the principle of electromagnetic induction and the Joule effect, where alternating electric current flowing through a coil generates a magnetic field. This magnetic field induces eddy currents in the conductive metal charge placed inside the furnace, causing the metal to heat up due to electrical resistance (Joule heating). The heat generated is localized within the metal itself, allowing for precise and efficient melting without direct contact between the coil and the metal. The process involves converting electrical energy into heat energy, enabling the melting of metals and the creation of alloys with exact compositions. Induction furnaces are widely used in metallurgy due to their efficiency, controllability, and clean operation.
Key Points Explained:
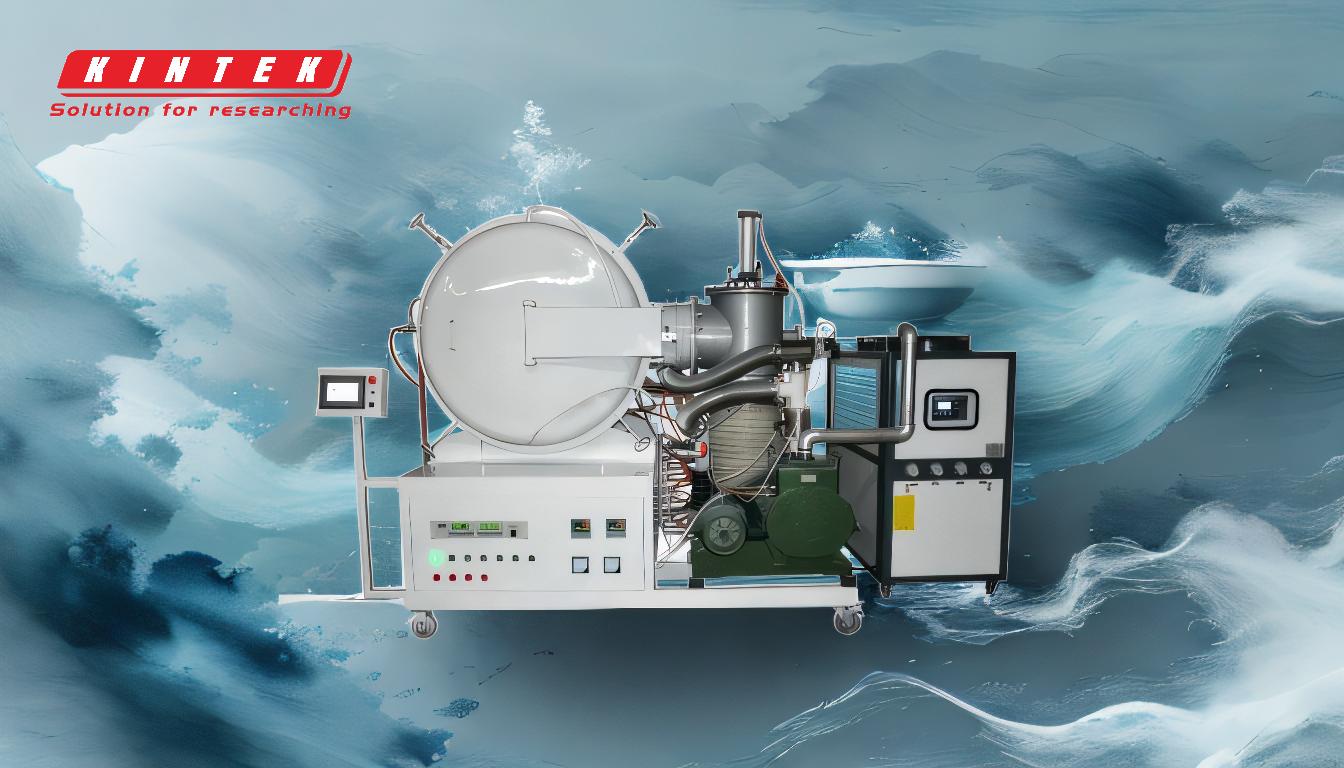
-
Electromagnetic Induction:
- The core principle of an induction furnace is electromagnetic induction. When an alternating current (AC) flows through a coil (inductor), it generates a rapidly alternating magnetic field around the coil.
- This magnetic field penetrates the conductive metal charge placed inside the furnace, inducing eddy currents within the metal. These eddy currents flow in closed loops and are responsible for heating the metal.
-
Joule Heating (Resistive Heating):
- The eddy currents induced in the metal encounter electrical resistance, which converts the electrical energy into heat energy. This phenomenon is known as Joule heating or resistive heating.
- The heat generated is localized within the metal itself, ensuring efficient and rapid melting without heating the surrounding furnace structure.
-
Frequency Conversion:
- Induction furnaces typically use medium-frequency alternating currents (300 Hz to 1000 Hz) for optimal performance. This is achieved by converting the standard power frequency (50 Hz or 60 Hz) into a higher frequency using a power supply unit.
- The process involves converting the three-phase AC power into direct current (DC) and then into adjustable medium-frequency AC. This higher frequency enhances the efficiency of eddy current generation and heat production.
-
Non-Contact Heating:
- Induction heating is a non-contact process, meaning the coil does not physically touch the metal being heated. This eliminates contamination and allows for precise control over the melting process.
- The absence of direct contact also reduces wear and tear on the furnace components, extending their lifespan.
-
Transformer Principle:
- The induction furnace operates similarly to a transformer. The coil acts as the primary winding, and the metal charge acts as the secondary winding.
- The alternating magnetic field induces a current in the metal, which generates heat. The primary coil is typically cooled by circulating water to prevent overheating.
-
Advantages of Induction Furnaces:
- Precision: The ability to control the frequency and power input allows for precise temperature regulation, making it ideal for producing alloys with exact compositions.
- Efficiency: Heat is generated directly within the metal, minimizing energy loss and improving overall efficiency.
- Clean Operation: Since there is no combustion or direct contact, induction furnaces produce fewer emissions and contaminants compared to traditional furnaces.
- Rapid Melting: The localized heating ensures quick melting times, increasing productivity.
-
Applications:
- Induction furnaces are widely used in metallurgy for melting and alloying metals such as steel, iron, copper, and aluminum.
- They are also used in foundries, recycling facilities, and laboratories for their ability to handle small to medium batches with high precision.
-
Cooling and Maintenance:
- The primary coil in an induction furnace is cooled using a water circulation system to prevent overheating and ensure consistent performance.
- Regular maintenance of the coil, power supply, and cooling system is essential to maintain the furnace's efficiency and longevity.
By leveraging the principles of electromagnetic induction and Joule heating, induction furnaces provide a highly efficient, precise, and clean method for melting metals, making them indispensable in modern metallurgical processes.
Summary Table:
Key Aspect | Details |
---|---|
Core Principle | Electromagnetic induction and Joule heating |
Heating Mechanism | Eddy currents induced in metal generate heat through electrical resistance |
Frequency Range | Medium-frequency AC (300 Hz to 1000 Hz) |
Non-Contact Heating | No physical contact between coil and metal, reducing contamination |
Advantages | Precision, efficiency, clean operation, rapid melting |
Applications | Metallurgy, foundries, recycling, labs |
Cooling System | Water circulation for coil cooling |
Ready to enhance your metal melting process? Contact us today to learn more about induction furnaces!