Physical vapor deposition (PVD) is a technique used to deposit thin films of material onto a substrate. The principle of operation involves the physical process of vaporizing a solid material in a vacuum environment and then condensing it onto a substrate to form a thin film. This process does not involve chemical reactions, distinguishing it from chemical vapor deposition (CVD). The key steps include vaporization of the source material, transportation of the vapor through a vacuum, and condensation of the vapor onto the substrate. The method is widely used in various industries for coating applications due to its ability to produce high-quality, durable, and uniform thin films.
Key Points Explained:
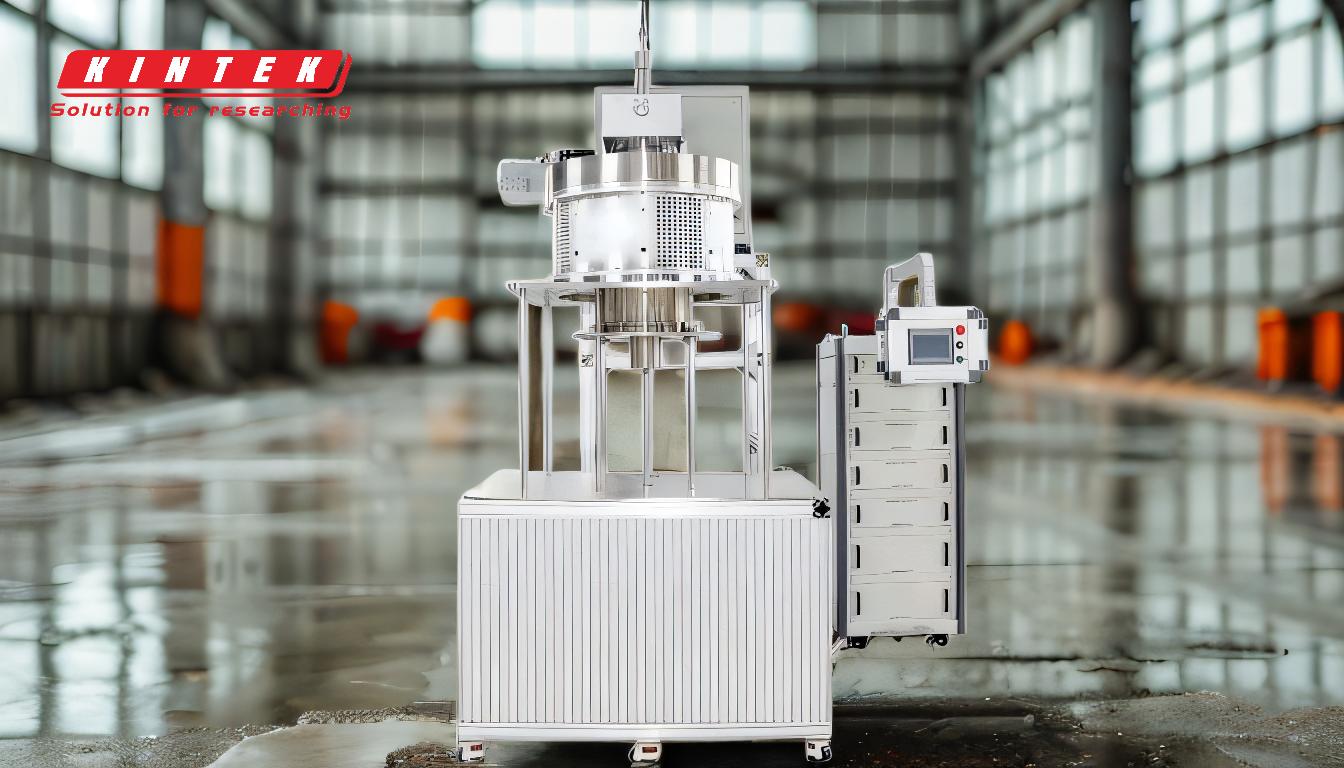
-
Vaporization of Source Material:
- In PVD, the source material, which is typically in solid form, is vaporized. This can be achieved through various methods such as thermal evaporation, sputtering, or electron beam evaporation.
- For instance, in thermal evaporation, the material is heated to a high temperature (250 to 350 degrees Celsius) in a high vacuum chamber, causing it to sublimate or evaporate. This creates a vapor pressure that allows the material to transition from a solid to a vapor state.
-
Transportation of Vapor:
- Once the source material is vaporized, the vapor particles travel through the vacuum environment. The vacuum is crucial as it minimizes the presence of other gases that could interfere with the deposition process.
- The vapor particles move in a straight line due to the low pressure, ensuring that they reach the substrate without significant scattering or contamination.
-
Condensation on Substrate:
- The vapor particles eventually reach the substrate, where they condense to form a thin film. The substrate is usually placed at a specific distance from the source material to ensure uniform coating.
- The condensation process is influenced by factors such as the temperature of the substrate, the rate of vapor deposition, and the nature of the material being deposited.
-
Types of PVD Techniques:
- Thermal Evaporation: As mentioned earlier, this involves heating the source material until it vaporizes. It is one of the simplest and most common PVD methods.
- Sputtering: In this method, high-energy ions are used to bombard the source material, causing atoms to be ejected and deposited onto the substrate. This technique allows for better control over the film's properties and is suitable for a wide range of materials.
- Electron Beam Evaporation: Here, an electron beam is used to heat the source material, providing a more localized and intense heat source compared to thermal evaporation. This method is particularly useful for materials with high melting points.
-
Applications of PVD:
- PVD is extensively used in the manufacturing of semiconductors, optical coatings, and decorative finishes. It is also employed in the production of hard coatings for tools and components to enhance their wear resistance and durability.
- The technique is favored for its ability to produce coatings with excellent adhesion, uniformity, and purity, making it indispensable in high-precision industries.
-
Advantages of PVD:
- High-Quality Films: PVD produces thin films with superior properties, including high density, low porosity, and excellent adhesion.
- Versatility: It can be used with a wide range of materials, including metals, ceramics, and composites.
- Environmental Friendliness: PVD is a clean process that does not involve harmful chemicals, making it environmentally friendly compared to some other coating techniques.
-
Challenges and Considerations:
- Cost: The equipment and maintenance costs for PVD systems can be high, especially for advanced techniques like electron beam evaporation.
- Complexity: The process requires precise control over various parameters, such as vacuum level, temperature, and deposition rate, to achieve the desired film properties.
- Material Limitations: While PVD is versatile, some materials may not be suitable for certain PVD techniques due to their physical properties.
In summary, the principle of operation of physical vapor deposition involves the physical transformation of a solid material into a vapor, which is then transported and condensed onto a substrate to form a thin film. The process is highly controllable and versatile, making it a preferred method for producing high-quality coatings in various industries.
Summary Table:
Key Aspect | Details |
---|---|
Principle | Vaporization of solid material, transportation in vacuum, and condensation on substrate. |
Techniques | Thermal Evaporation, Sputtering, Electron Beam Evaporation. |
Applications | Semiconductors, optical coatings, decorative finishes, and hard coatings for tools. |
Advantages | High-quality films, versatility, and environmental friendliness. |
Challenges | High cost, process complexity, and material limitations. |
Learn how PVD can enhance your coating processes—contact our experts today for tailored solutions!