Physical Vapor Deposition (PVD) is a coating technique that involves the vaporization of a solid material (target) into a gaseous state, followed by its condensation onto a substrate to form a thin film. The process occurs in a vacuum chamber to minimize contamination and ensure precise control over the deposition. PVD methods include sputtering, thermal evaporation, and arc discharge, each utilizing different energy sources to vaporize the target material. The vaporized atoms travel through the chamber and deposit onto the substrate, creating a durable, high-performance coating. PVD is widely used for applications requiring high adhesion, corrosion resistance, and the ability to coat materials with high melting points.
Key Points Explained:
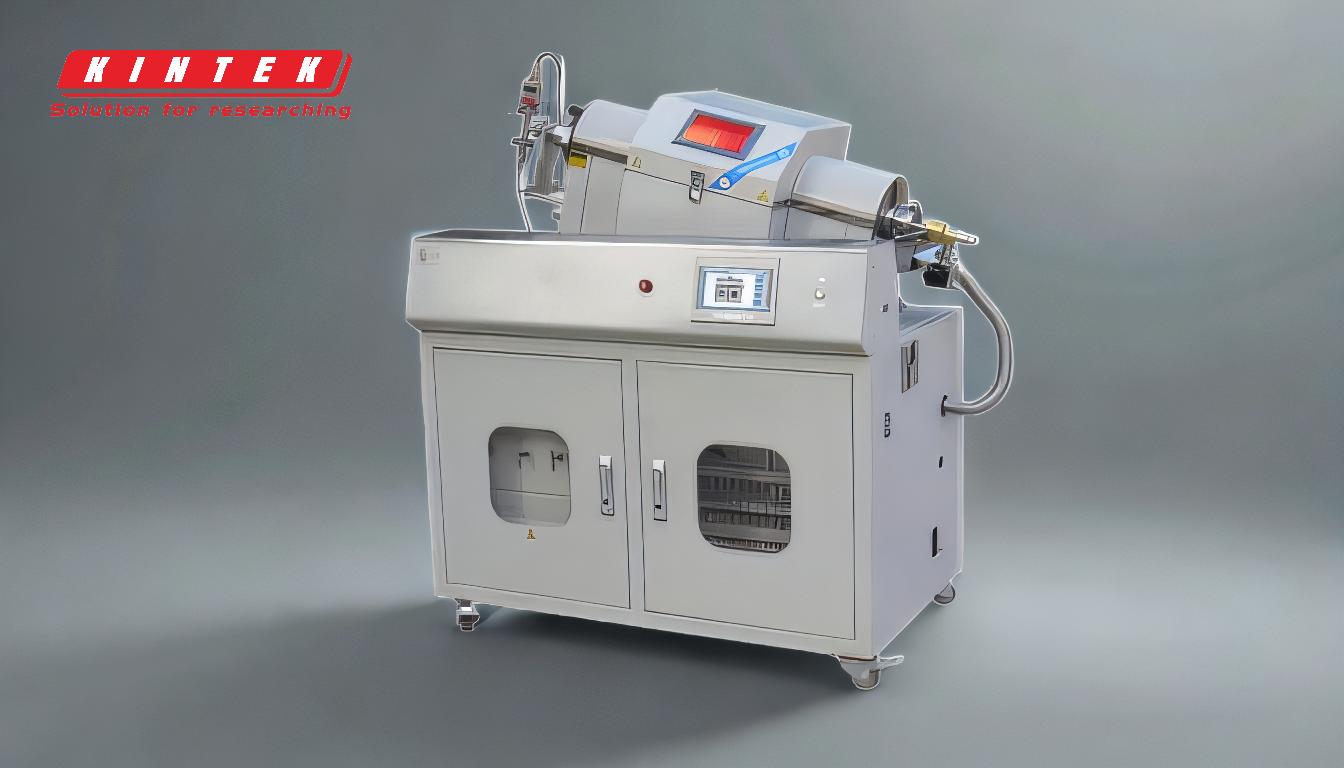
-
Vacuum Environment:
- PVD processes are conducted in a vacuum chamber to reduce the presence of background gases that could interfere with the deposition.
- The vacuum environment ensures that the vaporized atoms travel unimpeded to the substrate, resulting in a clean and high-quality coating.
-
Vaporization of the Target Material:
- The target material, typically a solid, is vaporized using one of several methods:
- Thermal Evaporation: The target is heated to its evaporation point using resistive heating or electron beams.
- Sputtering: High-energy ions bombard the target, dislodging atoms from its surface.
- Arc Discharge: An electric arc vaporizes the target material.
- These methods convert the solid target into a vapor phase, enabling it to travel through the chamber.
- The target material, typically a solid, is vaporized using one of several methods:
-
Transport of Vaporized Atoms:
- Once vaporized, the atoms or molecules of the target material travel through the vacuum chamber.
- The low-pressure environment ensures minimal collisions with other particles, allowing the vapor to reach the substrate efficiently.
-
Condensation on the Substrate:
- The vaporized atoms condense onto the substrate surface, forming a thin film.
- The adhesion of the film to the substrate is typically strong, resulting in durable coatings.
- The process is often "line-of-sight," meaning the atoms travel in straight lines and deposit only on surfaces directly exposed to the vapor stream.
-
Control of Film Thickness and Properties:
- The thickness and properties of the deposited film are controlled by adjusting parameters such as:
- Deposition Rate: Monitored using tools like quartz crystal rate monitors.
- Chamber Pressure: Lower pressures reduce contamination and improve film quality.
- Substrate Temperature: Typically maintained between 50 and 600 degrees Celsius to optimize adhesion and film structure.
- The thickness and properties of the deposited film are controlled by adjusting parameters such as:
-
Applications and Advantages:
- PVD is used to create coatings with high durability, corrosion resistance, and thermal stability.
- It is suitable for coating materials with high melting points, which are challenging to process using other methods.
- Common applications include:
- Protective coatings for tools and machinery.
- Decorative finishes for consumer products.
- Thin films for electronic and optical devices.
-
Comparison with Other Deposition Methods:
- PVD differs from Chemical Vapor Deposition (CVD) in that it relies on physical processes (vaporization and condensation) rather than chemical reactions.
- PVD coatings are typically thinner and more precise than those produced by CVD, making them ideal for applications requiring fine control over film properties.
By understanding these key points, a purchaser of equipment or consumables for PVD processes can make informed decisions about the materials, methods, and parameters required to achieve the desired coating properties.
Summary Table:
Key Aspect | Details |
---|---|
Vacuum Environment | Reduces contamination, ensures clean and high-quality coatings. |
Vaporization Methods | Thermal evaporation, sputtering, arc discharge. |
Transport of Atoms | Vaporized atoms travel unimpeded in a low-pressure environment. |
Condensation on Substrate | Forms durable, high-adhesion thin films in a line-of-sight process. |
Control Parameters | Deposition rate, chamber pressure, substrate temperature. |
Applications | Protective coatings, decorative finishes, thin films for electronics. |
Comparison with CVD | Relies on physical processes, thinner and more precise coatings. |
Ready to enhance your coating processes? Contact our experts today for tailored PVD solutions!