Physical Vapor Deposition (PVD) is a vacuum-based coating process where a solid material is vaporized and then deposited onto a substrate to form a thin film. The process involves transitioning the target material from a solid to a vapor phase, typically through methods like thermal evaporation, sputtering, or arc discharge, and then condensing it onto the substrate. PVD is widely used for creating durable, corrosion-resistant, and high-temperature-tolerant coatings. The process is carried out in a vacuum chamber to ensure controlled conditions, and the resulting thin films exhibit excellent adhesion and uniformity.
Key Points Explained:
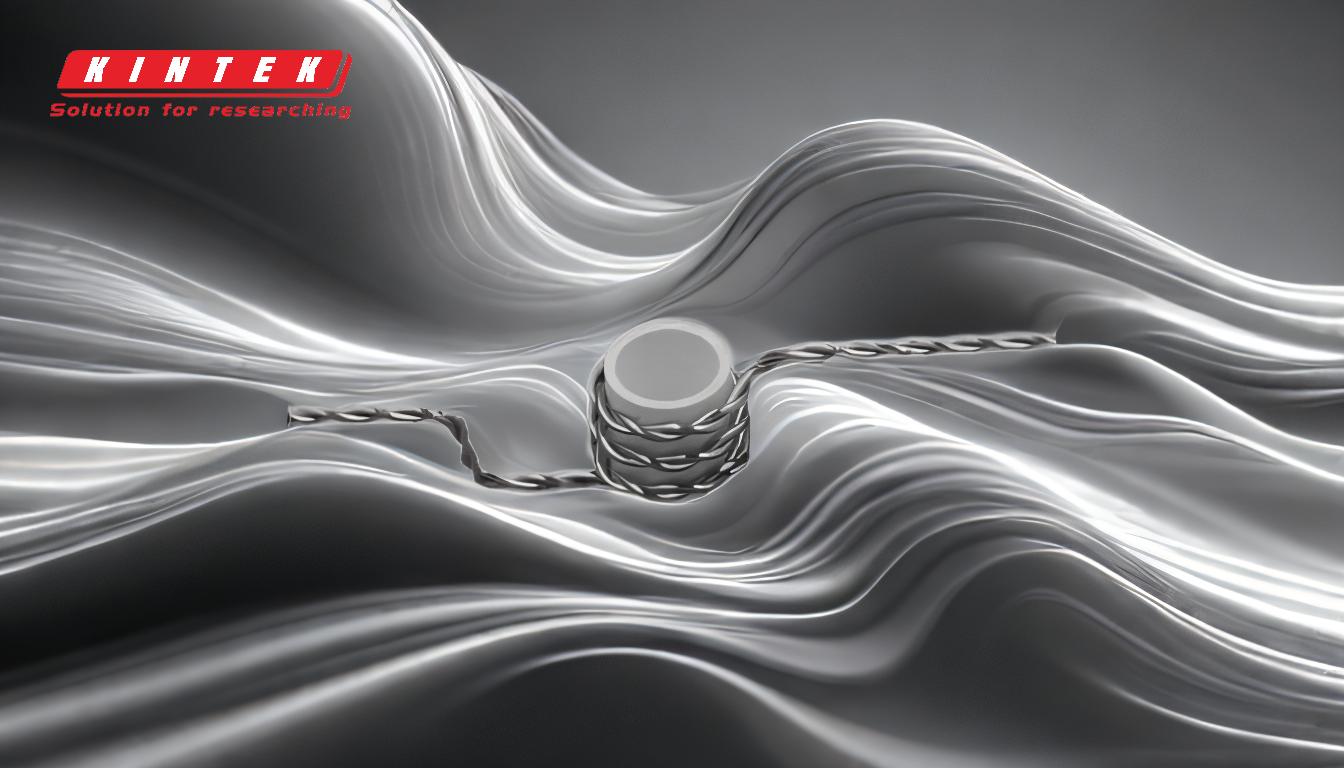
-
Fundamental Principle of PVD:
- PVD involves the transformation of a solid target material into a vapor phase, which is then deposited onto a substrate to form a thin film.
- The process is conducted in a vacuum chamber to prevent contamination and ensure controlled deposition conditions.
- The key steps include vaporization of the target material, transportation of the vapor through the chamber, and condensation onto the substrate.
-
Vaporization Methods:
- Thermal Evaporation: The target material is heated to high temperatures until it sublimes or evaporates. This is often achieved using electron beams, resistive heating, or laser beams.
- Sputtering: High-energy ions (usually argon) bombard the target material, knocking atoms off its surface and into the vapor phase.
- Arc Discharge: A high-intensity, low-voltage electric arc is used to vaporize the target material, producing highly ionized particles.
-
Transportation and Deposition:
- The vaporized material travels through the vacuum chamber and is directed toward the substrate.
- A potential difference or electric field may be applied to accelerate the ionized particles toward the substrate, ensuring uniform deposition.
- The vapor condenses on the substrate surface, forming a thin, adherent coating.
-
Advantages of PVD:
- High-Quality Coatings: PVD produces thin films with excellent adhesion, uniformity, and density.
- Material Versatility: It can handle materials with high melting points and create coatings for a wide range of applications.
- Durability: PVD coatings are highly durable, corrosion-resistant, and capable of withstanding high temperatures.
-
Applications of PVD:
- Industrial Coatings: Used for wear-resistant and corrosion-resistant coatings on tools, machinery, and automotive components.
- Optical and Electronic Devices: PVD is employed in the production of thin films for semiconductors, solar panels, and displays.
- Decorative Coatings: Used for aesthetic finishes on jewelry, watches, and consumer electronics.
-
Process Parameters:
- Vacuum Environment: Essential for preventing contamination and ensuring controlled deposition.
- Temperature: Typically ranges from 50 to 600 degrees Celsius, depending on the material and application.
- Line-of-Sight Deposition: Atoms travel in a straight line from the target to the substrate, requiring proper alignment for uniform coating.
-
Sub-Methods of PVD:
- Evaporation: Involves heating the target material until it evaporates and condenses on the substrate.
- Sputtering: Uses ion bombardment to dislodge atoms from the target, which then deposit onto the substrate.
- Arc Deposition: Utilizes an electric arc to vaporize the target material, producing a highly ionized plasma for deposition.
-
Challenges and Considerations:
- Complexity: PVD requires specialized equipment and precise control of process parameters.
- Cost: The initial investment in PVD equipment and maintenance can be high.
- Scalability: While suitable for small to medium-sized components, scaling up for large-scale production can be challenging.
By understanding these key points, one can appreciate the versatility and precision of PVD as a coating technology, making it a preferred choice for high-performance applications across various industries.
Summary Table:
Aspect | Details |
---|---|
Process Principle | Transforms solid material into vapor, deposits it onto a substrate. |
Vaporization Methods | Thermal Evaporation, Sputtering, Arc Discharge. |
Advantages | High-quality, durable, corrosion-resistant, and high-temperature coatings. |
Applications | Industrial, optical, electronic, and decorative coatings. |
Process Parameters | Vacuum environment, 50-600°C temperature, line-of-sight deposition. |
Challenges | High cost, complexity, and scalability limitations. |
Discover how PVD can enhance your projects—contact our experts today!