Sintering is a thermal process that transforms powdery materials into dense, solid bodies by applying heat and pressure below the material's melting point. This process relies on solid-state diffusion, where atoms migrate across particle boundaries, fusing them into a cohesive structure. Key factors influencing sintering include temperature, heating rate, pressure, particle size, composition, and the sintering atmosphere. These factors collectively determine the kinetics, densification, and final properties of the sintered material. Smaller particles and homogeneous compositions enhance densification, while higher temperatures and pressures improve particle rearrangement and eliminate porosity. Sintering is widely used in powder metallurgy and ceramic manufacturing to produce durable, high-performance materials.
Key Points Explained:
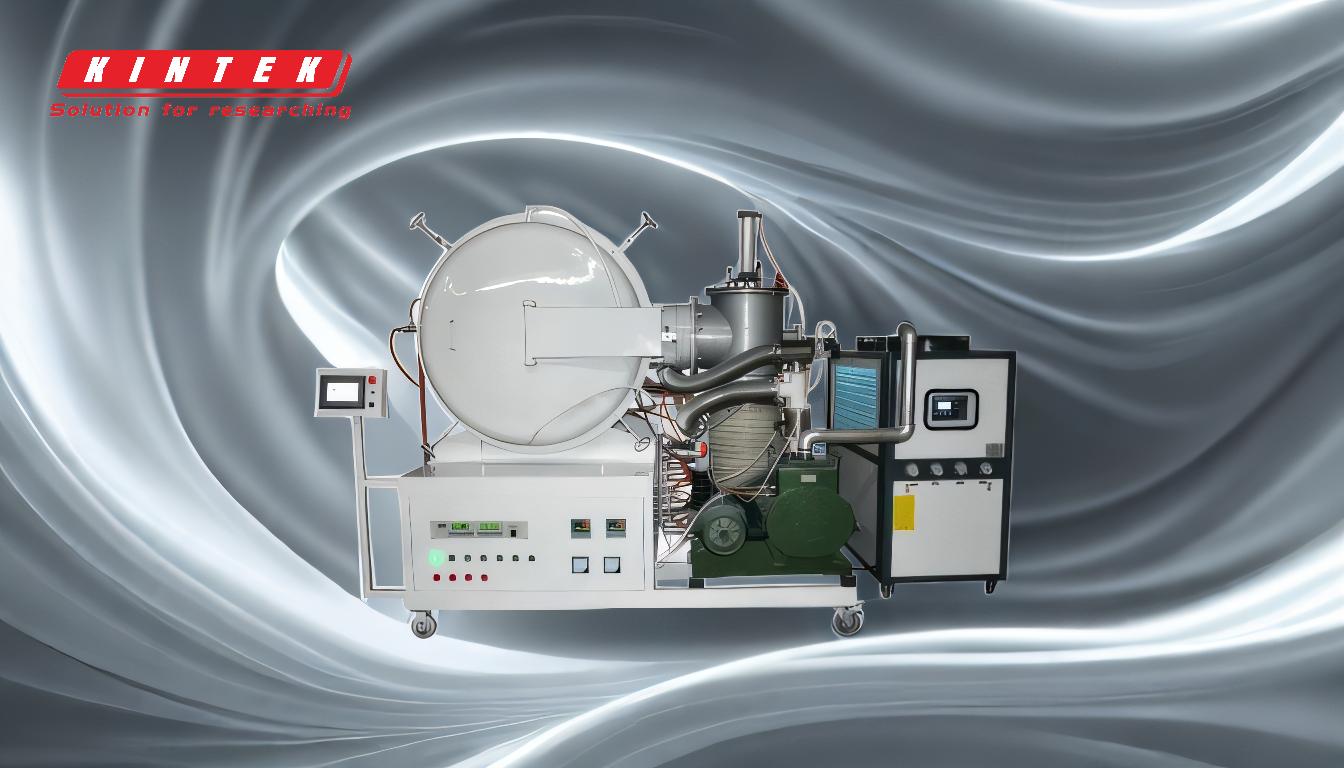
-
Principle of Sintering:
- Sintering involves the application of heat and pressure to powdery materials, causing particles to bond through solid-state diffusion without reaching the material's melting point.
- The process results in densification, where porosity is reduced, and the material becomes a cohesive, solid mass.
- It is commonly used in industries like powder metallurgy and ceramic manufacturing to produce durable and high-performance components.
-
Key Factors Affecting Sintering:
-
Temperature:
- Determines the kinetics of sintering and the final material properties.
- Higher temperatures accelerate atomic diffusion, enhancing particle bonding and densification.
- However, excessively high temperatures can lead to unwanted grain growth or material degradation.
-
Heating Rate:
- Influences the uniformity of densification.
- A controlled heating rate ensures even temperature distribution, preventing defects like warping or cracking.
-
Pressure:
- Enhances particle rearrangement and reduces porosity by forcing particles into closer contact.
- Applied pressure can also improve the mechanical properties of the sintered material.
-
Particle Size:
- Smaller particles have a higher surface area-to-volume ratio, promoting faster diffusion and better densification.
- Uniform particle size distribution ensures consistent sintering behavior.
-
Composition:
- Homogeneous compositions lead to more predictable sintering outcomes.
- The presence of alloying elements or impurities can alter diffusion rates and material properties.
-
Sintering Atmosphere:
- The environment (e.g., air, vacuum, or inert gases like argon or nitrogen) affects oxidation, contamination, and diffusion rates.
- Controlled atmospheres are crucial for materials sensitive to oxidation or requiring specific chemical reactions during sintering.
-
Temperature:
-
Applications of Sintering:
-
Powder Metallurgy:
- Used to produce metal components with complex shapes and high strength, such as gears, bearings, and automotive parts.
-
Ceramic Manufacturing:
- Enables the production of high-performance ceramics for applications like cutting tools, electrical insulators, and biomedical implants.
-
High-Melting-Point Materials:
- Essential for processing materials like tungsten and molybdenum, which are difficult to melt and cast conventionally.
-
Powder Metallurgy:
-
Advantages of Sintering:
- Produces materials with superior mechanical properties, such as hardness, strength, and durability.
- Allows for the creation of complex shapes and near-net-shape components, reducing the need for extensive machining.
- Enables the use of materials with extremely high melting points, expanding the range of feasible applications.
-
Challenges and Considerations:
- Achieving uniform densification requires precise control of temperature, pressure, and heating rates.
- Residual porosity can affect the mechanical properties of the sintered material, necessitating post-sintering treatments like hot isostatic pressing (HIP).
- The choice of sintering atmosphere and composition must align with the material's properties and intended application to avoid defects or contamination.
By understanding the principles and factors influencing sintering, manufacturers can optimize the process to produce high-quality materials tailored to specific applications.
Summary Table:
Key Factors | Impact on Sintering |
---|---|
Temperature | Accelerates atomic diffusion; higher temps improve bonding but risk grain growth. |
Heating Rate | Ensures uniform densification; prevents defects like warping or cracking. |
Pressure | Enhances particle rearrangement and reduces porosity; improves mechanical properties. |
Particle Size | Smaller particles promote faster diffusion and better densification. |
Composition | Homogeneous compositions lead to predictable outcomes; impurities alter properties. |
Sintering Atmosphere | Controlled environments prevent oxidation and contamination; crucial for material quality. |
Optimize your sintering process for superior results—contact our experts today!