Sintering is a critical process in materials science and manufacturing, where powdered materials are transformed into dense, solid bodies without reaching their melting points. This is achieved through the application of heat and pressure, which facilitates the diffusion of atoms across particle boundaries, leading to the fusion of particles into a cohesive mass. Sintering is widely used in industries such as powder metallurgy, ceramics, and plastics, enabling the production of components with enhanced mechanical properties, structural integrity, and durability. The process typically involves three stages: forming a shaped green part with a bonding agent, removing the bonding agent through heating, and finally fusing the particles at elevated temperatures.
Key Points Explained:
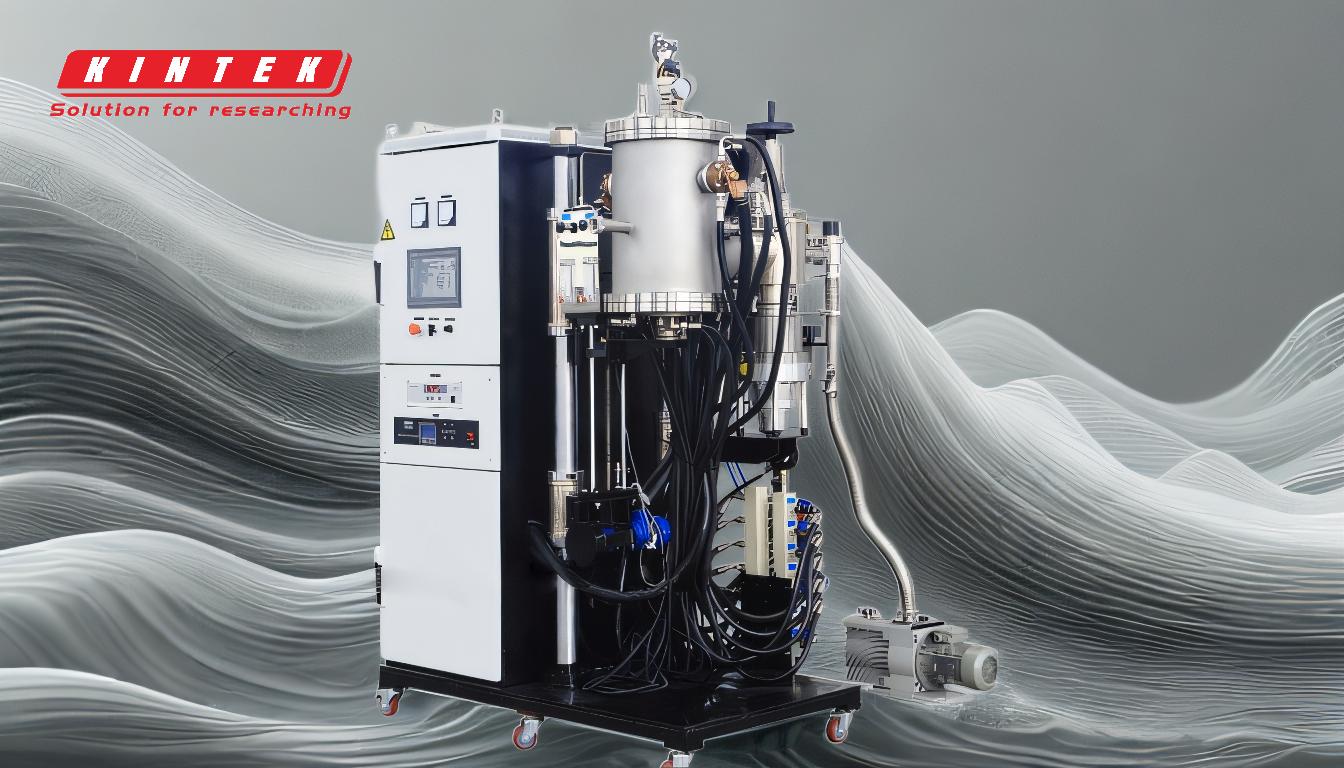
-
Definition and Purpose of Sintering:
- Sintering is a process that transforms powdered materials into dense, solid bodies by applying heat and pressure below the material's melting point.
- Its primary purpose is to create components with improved mechanical properties, such as strength, durability, and structural integrity, without liquefying the material.
-
Materials Suitable for Sintering:
- Sintering is applicable to a wide range of materials, including metals (e.g., tungsten, molybdenum), ceramics, plastics, and composite materials.
- It is particularly useful for materials with high melting points, where traditional melting and casting methods are impractical.
-
Stages of the Sintering Process:
-
Stage 1: Forming the Green Part:
- A blend of primary powder and a bonding agent (e.g., wax or polymer) is shaped into the desired form.
- The bonding agent temporarily holds the powder particles together.
-
Stage 2: Removal of the Bonding Agent:
- The green part is heated, causing the bonding agent to evaporate or burn away.
- This step prepares the material for particle fusion.
-
Stage 3: Particle Fusion:
- The temperature is increased to a point where particles begin to fuse at their surfaces.
- This can occur through surface melting or the use of an intermediate bonding agent (e.g., bronze) that melts and bonds the particles.
-
Stage 1: Forming the Green Part:
-
Mechanism of Sintering:
- Sintering relies on atomic diffusion, where atoms move across particle boundaries, creating strong bonds between adjacent particles.
- The process does not involve complete melting, ensuring that the material retains its original composition and properties.
-
Applications of Sintering:
-
Powder Metallurgy:
- Used to produce metal components with complex shapes and high precision, such as gears, bearings, and automotive parts.
-
Ceramics:
- Enables the creation of durable ceramic products, including tiles, insulators, and biomedical implants.
-
Plastics and Composites:
- Facilitates the production of lightweight, high-strength components for aerospace and consumer goods.
-
Powder Metallurgy:
-
Advantages of Sintering:
-
Cost-Effectiveness:
- Reduces material waste and allows for the use of less expensive raw materials.
-
Design Flexibility:
- Enables the production of complex geometries and intricate designs.
-
Enhanced Material Properties:
- Improves hardness, strength, and wear resistance of the final product.
-
Cost-Effectiveness:
-
Challenges and Considerations:
-
Control of Process Parameters:
- Precise control of temperature, pressure, and time is essential to achieve consistent results.
-
Material Compatibility:
- Not all materials are suitable for sintering, and some may require additional treatments or additives.
-
Dimensional Accuracy:
- Shrinkage during sintering can affect the final dimensions of the product, requiring careful design and calibration.
-
Control of Process Parameters:
In summary, sintering is a versatile and efficient process for transforming powdered materials into solid, high-performance components. By understanding its principles, stages, and applications, manufacturers can leverage sintering to produce advanced materials and products across various industries.
Summary Table:
Aspect | Details |
---|---|
Definition | Process of transforming powdered materials into dense, solid bodies using heat and pressure. |
Materials | Metals (e.g., tungsten, molybdenum), ceramics, plastics, and composites. |
Stages | 1. Forming the green part 2. Removing the bonding agent 3. Particle fusion. |
Applications | Powder metallurgy, ceramics, plastics, and composites. |
Advantages | Cost-effectiveness, design flexibility, enhanced material properties. |
Challenges | Precise control of parameters, material compatibility, dimensional accuracy. |
Discover how sintering can revolutionize your manufacturing process—contact us today!