The principle of a sputter coater revolves around the process of sputtering, where high-energy particles, typically argon ions, bombard a target material in a vacuum environment. This bombardment causes atoms from the target material to be ejected and subsequently deposited onto a substrate, forming a thin film. The process is driven by a glow discharge, creating a plasma that accelerates cations toward the negatively charged target, facilitating the ejection of target material atoms. This method is widely used in various industries for coating substrates with thin, uniform layers of materials.
Key Points Explained:
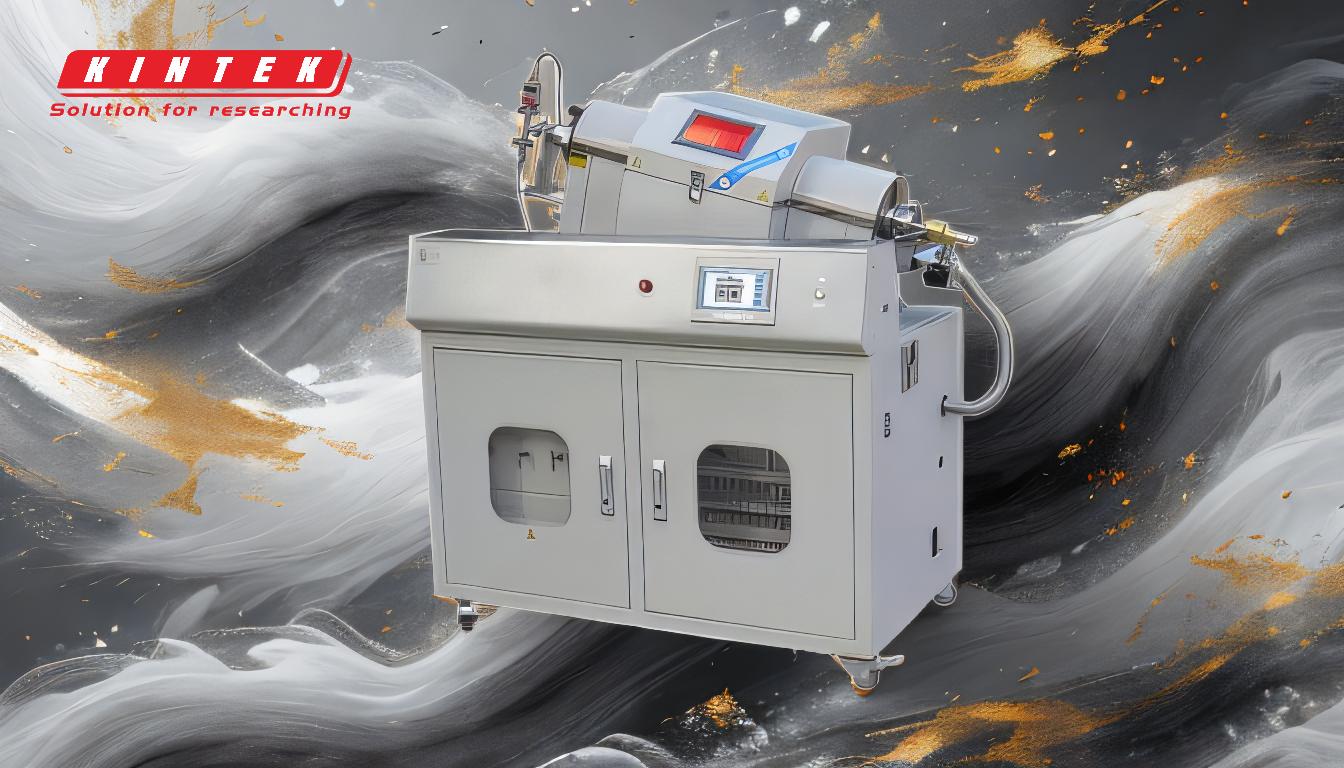
-
Vacuum Environment:
- Sputter coating requires a vacuum to ensure that the process is free from contaminants and to maintain the integrity of the thin film being deposited. The vacuum environment also allows for the efficient acceleration of argon ions toward the target material.
-
Glow Discharge and Plasma Formation:
- A glow discharge is created within the vacuum chamber by applying a high voltage between two electrodes. This discharge ionizes the argon gas, forming a plasma. The plasma consists of positively charged argon ions and free electrons.
-
Ion Bombardment:
- The positively charged argon ions in the plasma are accelerated toward the negatively charged target material (cathode) due to the electric field. When these high-energy ions strike the target surface, they transfer their energy to the target atoms.
-
Sputtering of Target Material:
- The energy transfer from the argon ions to the target atoms causes the latter to be ejected from the target surface. This phenomenon is known as sputtering. The ejected atoms travel through the vacuum and deposit onto the substrate.
-
Film Deposition:
- The ejected target atoms condense on the substrate, forming a thin, uniform film. The properties of the film, such as thickness, adhesion, and uniformity, can be controlled by adjusting parameters like the power applied, the pressure within the vacuum chamber, and the distance between the target and the substrate.
-
Applications of Sputter Coating:
- Sputter coating is used in various applications, including the production of thin films for semiconductors, optical coatings, and protective coatings. It is also employed in the preparation of samples for scanning electron microscopy (SEM) to enhance conductivity and improve image quality.
By understanding these key points, one can appreciate the intricate process of sputter coating and its significance in modern technology and material science. The ability to control and manipulate the deposition of thin films at the atomic level makes sputter coating a versatile and essential technique in numerous industries.
Summary Table:
Key Aspect | Description |
---|---|
Vacuum Environment | Ensures contamination-free deposition and efficient ion acceleration. |
Glow Discharge & Plasma | Forms plasma with argon ions and free electrons for ion bombardment. |
Ion Bombardment | High-energy argon ions eject target material atoms. |
Sputtering | Ejected atoms deposit onto a substrate, forming a thin film. |
Film Deposition | Thin films with controlled thickness, adhesion, and uniformity are created. |
Applications | Used in semiconductors, optical coatings, protective coatings, and SEM samples. |
Interested in sputter coating solutions for your industry? Contact our experts today to learn more!