Pyrolysis is a thermal decomposition process that breaks down organic materials at high temperatures in the absence of oxygen. It is widely used to convert waste materials like plastics, biomass, and other organic compounds into valuable byproducts such as bio-oil, syngas, and biochar. The procedure typically involves several stages, including feedstock preparation, pyrolysis reaction, and product separation and collection. Each step is critical to ensure efficient decomposition and the recovery of usable products. The process can vary slightly depending on the type of feedstock and the desired end products, but the core principles remain consistent.
Key Points Explained:
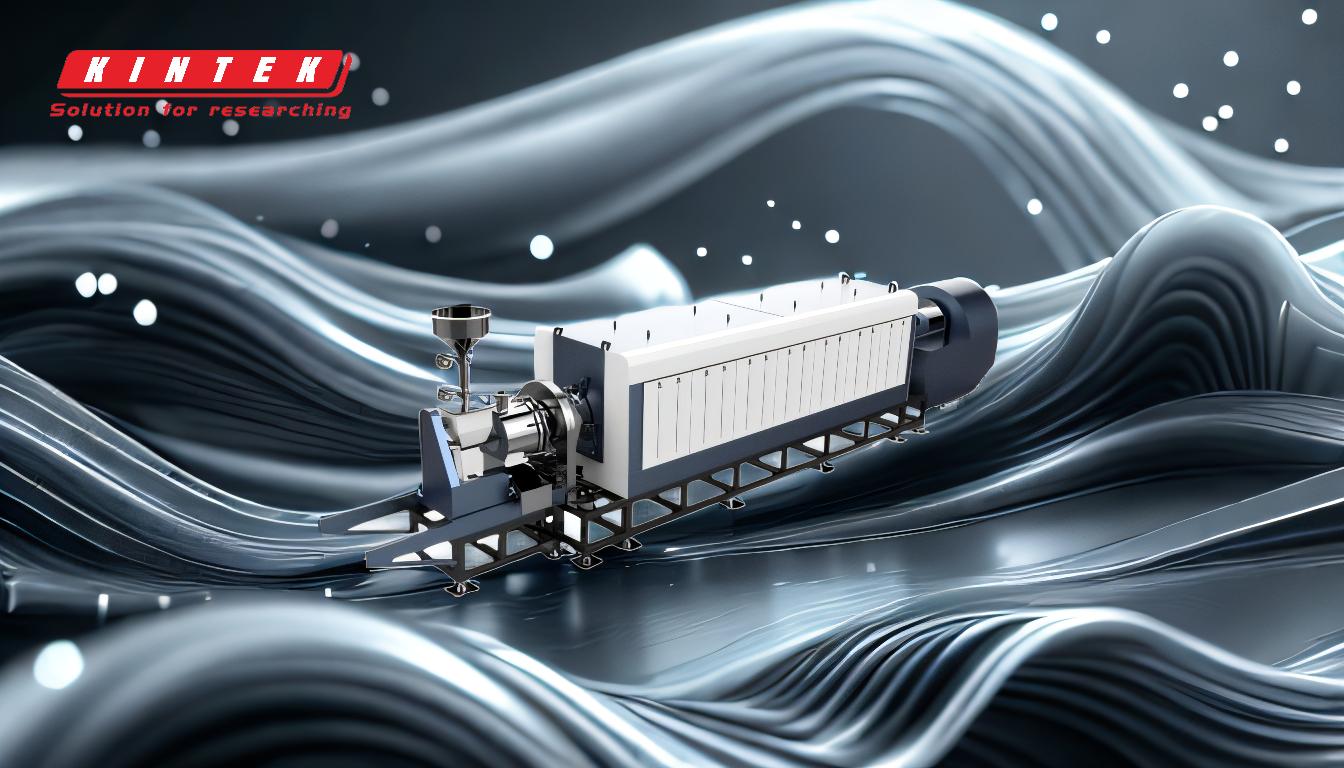
-
Feedstock Preparation:
- Drying: The feedstock, whether plastic waste, biomass, or other organic materials, is dried to remove moisture. This step is crucial because moisture can interfere with the pyrolysis reaction and reduce the efficiency of the process.
- Pre-treatment: Impurities such as metals, dirt, or non-organic materials are removed from the feedstock. This ensures that the pyrolysis process is not contaminated and that the final products are of higher quality.
- Grinding/Size Reduction: The feedstock is ground or crushed to a specific size to ensure uniform heating and efficient decomposition during pyrolysis.
-
Loading and Heating:
- Loading into Pyrolysis Chamber: The prepared feedstock is loaded into a pyrolysis reactor or chamber. In some cases, a catalyst may be added to enhance the breakdown of the material.
- Heating: The feedstock is heated to temperatures ranging from 200°C to 900°C, depending on the type of material and the desired products. The heating is done in the absence of oxygen to prevent combustion and ensure that the material decomposes rather than burns.
- Transformation: At high temperatures, the chemical bonds in the feedstock break down, leading to the formation of smaller molecules. This results in the production of volatile gases, liquid products (bio-oil), and solid residues (biochar).
-
Condensation and Collection:
- Condensation: The volatile gases produced during pyrolysis are condensed into liquid form, typically bio-oil. This is done by cooling the gases, often using a condenser or quenching system.
- Collection of Biochar: The solid residue, known as biochar, settles at the bottom of the reactor and is collected for further use. Biochar can be used as a soil amendment or for other industrial applications.
- Gas Separation: Non-condensable gases, such as syngas, are separated and can be recycled back into the combustion chamber to provide heat for the pyrolysis process or used as a fuel.
-
Refining and Final Product Use:
- Refining: The condensed bio-oil may undergo further refining to remove impurities and improve its quality. This step is particularly important if the bio-oil is intended for use as fuel.
- End Products: The final products of pyrolysis include bio-oil, which can be used as a renewable fuel; biochar, which has applications in agriculture and carbon sequestration; and syngas, which can be used for energy generation.
-
Environmental Considerations:
- Exhaust Gas Treatment: The exhaust gases from the pyrolysis process are often treated to remove harmful substances before being released into the atmosphere. This step is crucial for minimizing environmental impact.
- Energy Efficiency: The pyrolysis process is designed to be energy-efficient, with heat recovery systems often integrated to reuse the energy generated during the process.
-
Industrial Applications:
- Large-Scale Pyrolysis: In industrial settings, the process is optimized for continuous operation, with automated feeding systems, advanced temperature control, and efficient product separation mechanisms.
- Versatility: Pyrolysis can be adapted to process a wide range of feedstocks, including plastics, biomass, and rubber, making it a versatile technology for waste management and resource recovery.
In summary, the pyrolysis procedure is a multi-step process that involves preparing the feedstock, heating it in an oxygen-free environment, and then collecting and refining the resulting products. Each stage is carefully controlled to maximize efficiency and product quality, making pyrolysis a valuable tool for converting waste materials into useful resources.
Summary Table:
Stage | Key Steps | Purpose |
---|---|---|
Feedstock Preparation | Drying, Pre-treatment, Grinding/Size Reduction | Remove moisture, impurities, and ensure uniform heating. |
Loading and Heating | Loading into chamber, Heating (200°C–900°C), Transformation | Break down feedstock into gases, bio-oil, and biochar in an oxygen-free environment. |
Condensation and Collection | Condensation of gases, Collection of biochar, Gas separation | Convert gases to bio-oil, collect biochar, and separate syngas for reuse. |
Refining and Final Use | Refining bio-oil, Producing biochar and syngas | Improve product quality for fuel, agriculture, or energy generation. |
Environmental Considerations | Exhaust gas treatment, Energy efficiency | Minimize environmental impact and optimize energy use. |
Industrial Applications | Large-scale pyrolysis, Versatility in feedstock processing | Adapt the process for continuous, automated waste-to-resource conversion. |
Discover how pyrolysis can revolutionize your waste management—contact our experts today for a tailored solution!