The Chemical Vapor Deposition (CVD) process is a sophisticated method used to produce high-quality, high-performance solid materials, typically in the form of thin films or coatings. It involves a series of well-defined steps that ensure the precise deposition of materials onto a substrate. The process begins with the introduction of gaseous reactants into a reaction chamber, where they undergo chemical reactions to form the desired material. This material is then deposited onto a substrate, where it forms a thin film or coating. The process is carefully controlled to ensure the quality and characteristics of the deposited material, with factors such as temperature, pressure, and reactant flow rate playing crucial roles.
Key Points Explained:
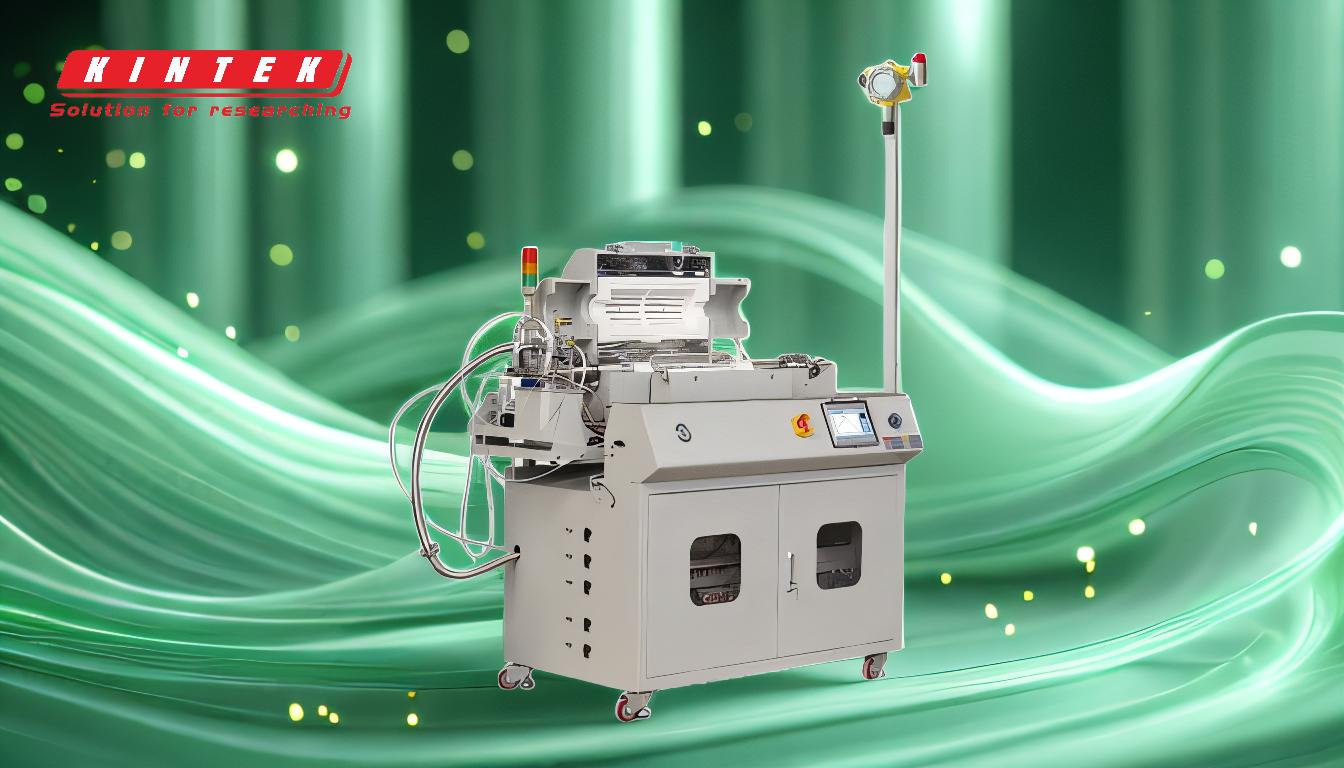
-
Introduction of Reactants:
- The CVD process starts with the introduction of gaseous precursors into a reaction chamber. These precursors are typically volatile compounds that can be easily vaporized and transported into the chamber.
- The reactants are chosen based on the desired material to be deposited. For example, if silicon dioxide is to be deposited, a silicon-containing gas like silane (SiH4) and an oxygen source like oxygen gas (O2) might be used.
-
Activation of Reactants:
- Once inside the reaction chamber, the gaseous precursors need to be activated to initiate the chemical reactions. Activation can be achieved through various methods, including thermal energy, plasma, or catalysts.
- Thermal activation involves heating the reactants to a high temperature, typically between 500°C to 1200°C, depending on the material being deposited. This high temperature provides the necessary energy for the reactants to decompose and react.
- Plasma activation uses an electric field to ionize the gas, creating a plasma that enhances the reactivity of the precursors. This method is often used in Plasma-Enhanced Chemical Vapor Deposition (PECVD).
- Catalytic activation involves using a catalyst to lower the activation energy required for the reaction, allowing it to proceed at lower temperatures.
-
Surface Reaction and Deposition:
- The activated precursors react at the surface of the substrate to form the desired material. This reaction can occur in the gas phase or directly on the substrate surface.
- In the gas phase, the reactants undergo chemical reactions to form intermediate species, which then adsorb onto the substrate surface. These adsorbed species undergo further reactions to form the final material.
- The reaction can also occur directly on the substrate surface, where the reactants adsorb and react to form the material. This process is known as surface reaction or heterogeneous reaction.
- The deposited material forms a thin film or coating on the substrate. The quality of the film depends on factors such as the uniformity of the deposition, the adhesion of the film to the substrate, and the absence of defects.
-
Removal of Byproducts:
- During the CVD process, various byproducts are generated, including volatile gases and non-volatile residues. These byproducts need to be removed from the reaction chamber to prevent contamination and ensure the purity of the deposited material.
- Volatile byproducts are typically removed by flowing an inert gas, such as nitrogen or argon, through the chamber. This gas carries the byproducts out of the chamber and into a exhaust system.
- Non-volatile residues may require additional cleaning steps, such as etching or chemical treatment, to remove them from the substrate surface.
-
Control of Process Parameters:
- The success of the CVD process depends on the precise control of various parameters, including temperature, pressure, and reactant flow rate.
- Temperature: The substrate temperature is a critical parameter that affects the rate of the chemical reactions and the quality of the deposited material. Too high a temperature can lead to excessive decomposition of the precursors, while too low a temperature may result in incomplete reactions.
- Pressure: The pressure inside the reaction chamber influences the mean free path of the gas molecules and the rate of diffusion. Lower pressures can enhance the uniformity of the deposition, while higher pressures may increase the deposition rate.
- Reactant Flow Rate: The flow rate of the reactants determines the concentration of the precursors in the reaction chamber. Proper control of the flow rate ensures a consistent supply of reactants and prevents the formation of unwanted byproducts.
-
Applications of CVD:
- CVD is widely used in various industries for the deposition of thin films and coatings. Some common applications include:
- Semiconductor Manufacturing: CVD is used to deposit silicon dioxide, silicon nitride, and other materials onto silicon wafers to create integrated circuits.
- Optical Coatings: CVD is used to deposit anti-reflective coatings, protective coatings, and other optical films onto lenses and mirrors.
- Protective Coatings: CVD is used to deposit hard, wear-resistant coatings onto cutting tools, molds, and other components to extend their service life.
- Energy Storage: CVD is used to deposit materials for batteries, fuel cells, and solar cells, enhancing their performance and durability.
- CVD is widely used in various industries for the deposition of thin films and coatings. Some common applications include:
In conclusion, the CVD process is a highly controlled and versatile method for depositing thin films and coatings onto substrates. By carefully managing the introduction of reactants, activation methods, surface reactions, and removal of byproducts, the CVD process can produce high-quality materials with precise properties. The control of process parameters such as temperature, pressure, and reactant flow rate is essential for achieving the desired results. With its wide range of applications, CVD continues to be a critical technology in various industries.
Summary Table:
Step | Description |
---|---|
Introduction of Reactants | Gaseous precursors are introduced into the reaction chamber. |
Activation of Reactants | Reactants are activated using thermal energy, plasma, or catalysts. |
Surface Reaction & Deposition | Activated precursors react to form a thin film on the substrate. |
Removal of Byproducts | Volatile and non-volatile byproducts are removed to ensure material purity. |
Control of Parameters | Temperature, pressure, and reactant flow rate are precisely controlled. |
Applications | Used in semiconductor manufacturing, optical coatings, and energy storage. |
Discover how CVD can revolutionize your material production—contact our experts today!