Chemical Vapor Deposition (CVD) is a process used to produce high-quality, high-performance solid materials, often in the form of thin films. The process involves the chemical reaction of gaseous precursors on a substrate surface, leading to the deposition of a solid material. CVD is widely used in industries such as semiconductor manufacturing, coatings, and diamond synthesis. The process typically involves several key steps: precursor introduction, gas-phase reactions, surface reactions, and film growth. Each step is carefully controlled to ensure the desired material properties and purity.
Key Points Explained:
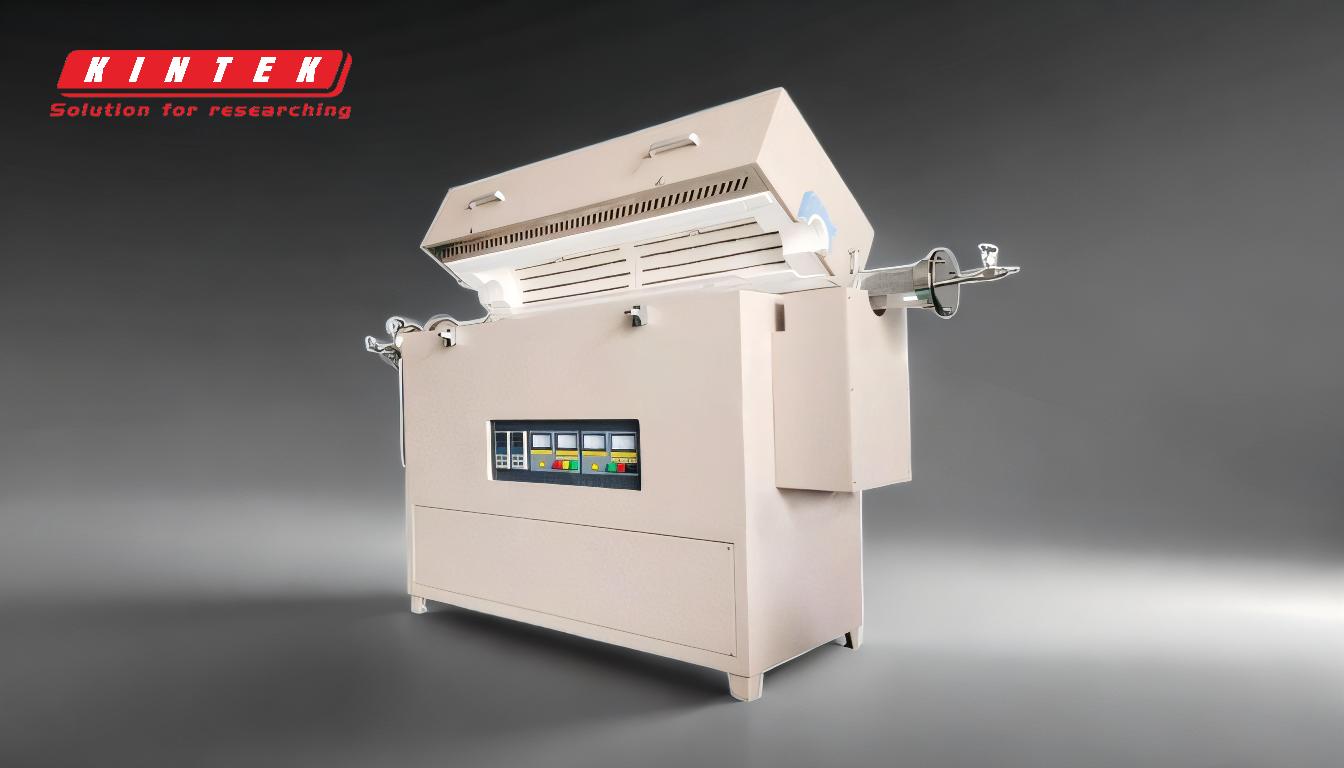
-
Precursor Introduction:
- In CVD, gaseous precursors are introduced into a reaction chamber. These precursors are typically volatile compounds that can decompose or react at elevated temperatures.
- The choice of precursor depends on the material to be deposited. For example, in diamond synthesis, methane (CH₄) is commonly used as a carbon source.
-
Gas-Phase Reactions:
- Once inside the reaction chamber, the precursors undergo gas-phase reactions. These reactions can include thermal decomposition, oxidation, or reduction, depending on the desired material and process conditions.
- The reaction environment is often controlled by adjusting parameters such as temperature, pressure, and gas flow rates. For instance, in diamond CVD, the temperature is maintained between 700°C to 1300°C to facilitate the decomposition of methane into carbon atoms.
-
Surface Reactions:
- The reactive species generated in the gas phase diffuse to the substrate surface, where they adsorb and undergo surface reactions.
- These surface reactions lead to the formation of the desired material on the substrate. In the case of diamond synthesis, carbon atoms deposit on the substrate and form a crystalline diamond structure.
-
Film Growth:
- The deposition process continues layer by layer, leading to the growth of a thin film on the substrate. The thickness and quality of the film depend on the deposition time, temperature, and precursor concentration.
- For example, in diamond CVD, the growth process can take several weeks, and the final diamond size is directly related to the growth time.
-
Vacuum and Pressure Control:
- CVD processes often operate under reduced pressure or vacuum conditions to control the reaction kinetics and improve the quality of the deposited material.
- The use of a vacuum system, such as in short path vacuum distillation, helps to lower the boiling points of compounds, reduce thermal degradation, and achieve higher purity.
-
Applications and Challenges:
- CVD is used in various applications, including the production of semiconductors, optical coatings, and synthetic diamonds.
- However, the process can be time-consuming and requires precise control over multiple parameters. For example, in diamond synthesis, the repeated removal of the graphite layer is necessary to form larger diamonds, making the process complex and labor-intensive.
In summary, the CVD process is a sophisticated method for depositing high-quality materials on substrates. It involves a series of controlled chemical reactions and surface processes, often conducted under vacuum or reduced pressure conditions to achieve the desired material properties. The process is widely used in various industries but requires careful optimization and control to ensure successful outcomes.
Summary Table:
Step | Description |
---|---|
Precursor Introduction | Gaseous precursors enter the reaction chamber and decompose at high temperatures. |
Gas-Phase Reactions | Precursors undergo thermal decomposition, oxidation, or reduction in the gas phase. |
Surface Reactions | Reactive species adsorb onto the substrate, forming the desired material. |
Film Growth | Layer-by-layer deposition creates a thin film with controlled thickness and quality. |
Vacuum/Pressure Control | Reduced pressure or vacuum conditions optimize reaction kinetics and material purity. |
Applications | Used in semiconductor manufacturing, coatings, and synthetic diamond production. |
Discover how CVD can enhance your material production—contact our experts today for tailored solutions!