Electron beam deposition (E-Beam) is a sophisticated physical vapor deposition (PVD) technique used to create thin, uniform coatings on substrates. The process involves generating a focused electron beam to heat and evaporate a source material within a high-vacuum environment. The evaporated material then travels through the chamber and condenses onto the substrate, forming a thin film. This method is highly precise, allowing for controlled deposition of materials like metals and ceramics. The process can be enhanced with ion beams to improve coating adhesion and density, making it ideal for applications requiring high-performance optical or functional coatings.
Key Points Explained:
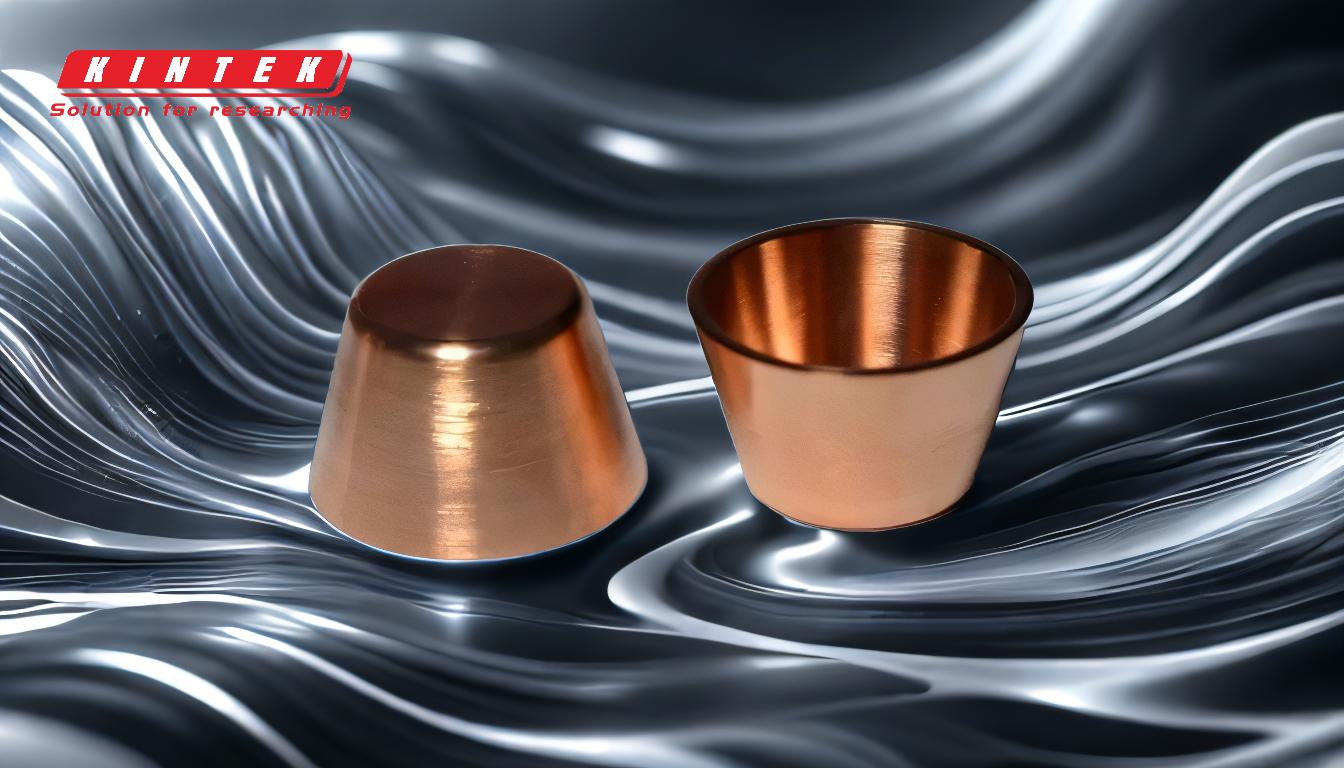
-
Electron Beam Generation and Focusing:
- A magnet is used to focus electrons into a high-energy beam.
- The electron beam is directed toward a crucible containing the source material (e.g., metals or ceramics).
- This step is critical for ensuring the energy is concentrated enough to evaporate the material.
-
Material Evaporation:
- The energy from the electron beam heats the source material, causing it to evaporate.
- Metals typically melt first and then evaporate, while ceramics sublimate directly from solid to vapor.
- The evaporation process occurs in a high-vacuum environment to minimize contamination and ensure efficient vapor travel.
-
Vapor Deposition:
- The evaporated material forms a vapor cloud that travels out of the crucible.
- The vapor condenses onto the substrate, forming a thin, uniform coating.
- The substrate's position, rotation, and temperature are precisely controlled to achieve the desired coating thickness and uniformity.
-
Enhancements with Ion Beam Assistance:
- An ion beam can be used to bombard the substrate during deposition.
- This increases the adhesion energy between the coating and the substrate, resulting in denser and more robust coatings.
- Ion beam assistance also reduces stress in the coating, improving its durability and performance.
-
Process Control and Precision:
- The entire process is controlled by precision computer systems.
- Parameters such as heating, vacuum levels, substrate location, and rotation are meticulously managed to achieve conformal coatings of pre-specified thicknesses.
- This level of control makes electron beam deposition suitable for high-precision applications like optical coatings.
-
Applications and Advantages:
- Electron beam deposition is widely used in industries requiring high-performance coatings, such as optics, semiconductors, and aerospace.
- The method offers excellent control over coating thickness, uniformity, and material properties.
- Enhanced adhesion and reduced stress make the coatings more durable and reliable for demanding applications.
By understanding these key points, a purchaser of equipment or consumables can appreciate the complexity and precision of electron beam deposition, ensuring they select the right tools and materials for their specific needs.
Summary Table:
Key Step | Description |
---|---|
Electron Beam Generation | Focused high-energy beam heats and evaporates source material in a vacuum. |
Material Evaporation | Source material evaporates, forming a vapor cloud for deposition. |
Vapor Deposition | Vapor condenses on the substrate, creating a thin, uniform coating. |
Ion Beam Assistance | Enhances coating adhesion and density for durable, high-performance films. |
Process Control | Precision systems manage heating, vacuum, and substrate parameters. |
Applications | Ideal for optics, semiconductors, and aerospace due to superior coating quality. |
Ready to elevate your coating process? Contact our experts today to learn more about electron beam deposition solutions!