Low-pressure chemical vapor deposition (LPCVD) is a specialized form of chemical vapor deposition (CVD) that operates under reduced pressure conditions to deposit thin films on substrates. This process enhances film uniformity and quality by minimizing unwanted gas-phase reactions and improving step coverage. The LPCVD process involves several key steps, including the transport of gaseous reactants to the substrate surface, adsorption, chemical reactions, film nucleation, and desorption of by-products. These steps are carefully controlled to ensure precise deposition of materials such as silicon dioxide, silicon nitride, and polysilicon, which are critical in semiconductor manufacturing and other high-tech applications.
Key Points Explained:
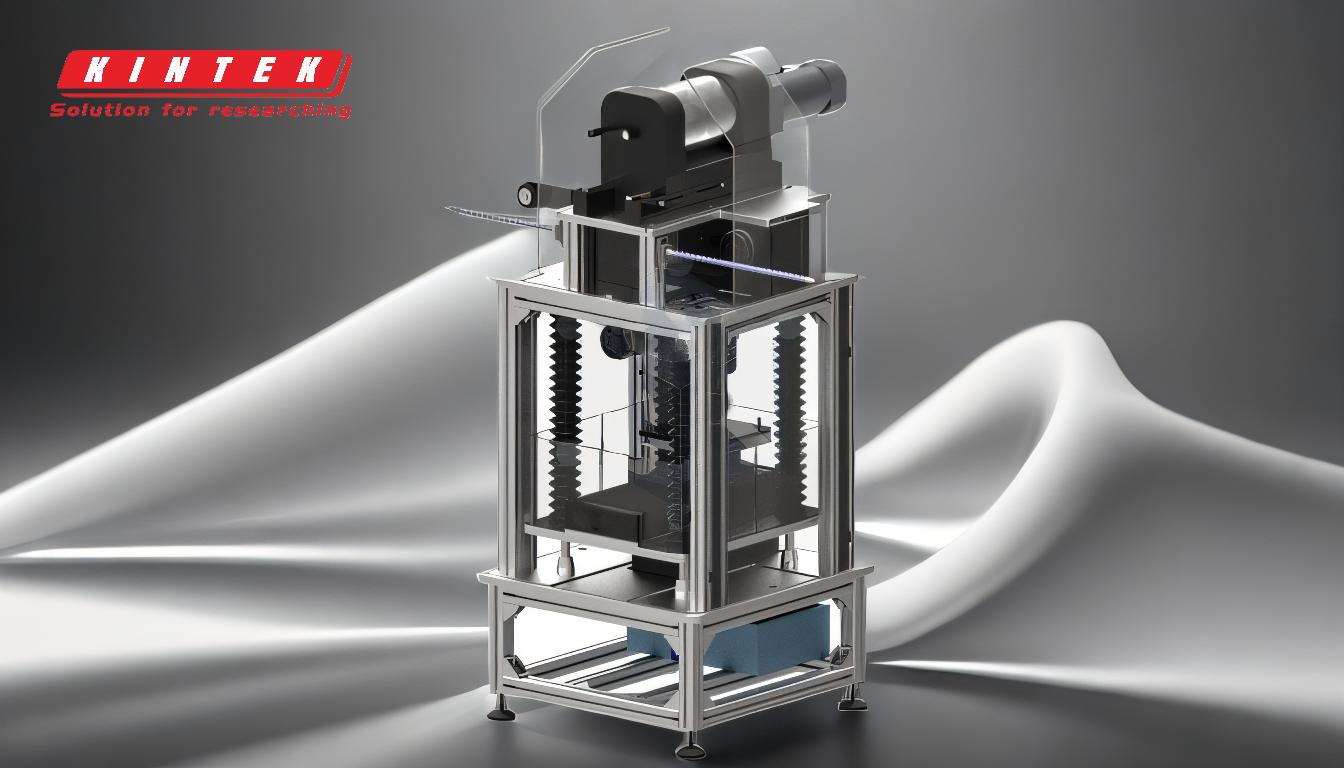
-
Transport of Reacting Gaseous Species to the Surface:
- In LPCVD, volatile precursor gases are introduced into a vacuum chamber. The low-pressure environment ensures that these gases are transported efficiently to the substrate surface without significant gas-phase reactions. This step is crucial for achieving uniform film deposition.
-
Adsorption of the Species on the Surface:
- Once the gaseous species reach the substrate, they adsorb onto its surface. Adsorption is influenced by factors such as temperature, pressure, and the chemical nature of the substrate. Proper adsorption ensures that the reactants are in close proximity to the surface, facilitating the subsequent chemical reactions.
-
Heterogeneous Surface-Catalyzed Reactions:
- The adsorbed species undergo chemical reactions on the substrate surface, often catalyzed by the substrate itself. These reactions transform the gaseous precursors into solid film material. For example, in the deposition of silicon dioxide, silane (SiH₄) and oxygen (O₂) react to form SiO₂.
-
Surface Diffusion of the Species to Growth Sites:
- After the initial reactions, the species diffuse across the substrate surface to reach growth sites where the film nucleates and grows. Surface diffusion is critical for achieving uniform film thickness and minimizing defects.
-
Nucleation and Growth of the Film:
- Nucleation involves the formation of small clusters of the deposited material, which then grow into a continuous film. The growth rate and film quality depend on factors such as temperature, pressure, and the concentration of reactants.
-
Desorption of Gaseous Reaction Products and Transportation Away from the Surface:
- As the film grows, gaseous by-products are generated. These by-products must desorb from the surface and be transported away from the reaction zone to prevent contamination and ensure the purity of the deposited film. Efficient removal of by-products is facilitated by the low-pressure environment in LPCVD.
-
Advantages of LPCVD:
- LPCVD offers several advantages over atmospheric pressure CVD, including better film uniformity, higher purity, and improved step coverage. The reduced pressure minimizes unwanted gas-phase reactions, leading to higher-quality films with fewer defects.
-
Applications of LPCVD:
- LPCVD is widely used in the semiconductor industry for depositing thin films of materials such as silicon dioxide, silicon nitride, and polysilicon. These films are essential for manufacturing integrated circuits, MEMS devices, and other microelectronic components.
By carefully controlling each step of the LPCVD process, manufacturers can produce high-quality thin films with precise thickness and composition, making LPCVD a critical technology in modern electronics and materials science.
Summary Table:
Step | Description |
---|---|
1. Transport of Gaseous Species | Volatile precursor gases are introduced into a vacuum chamber for efficient transport to the substrate. |
2. Adsorption on the Surface | Gaseous species adsorb onto the substrate surface, influenced by temperature, pressure, and chemistry. |
3. Surface-Catalyzed Reactions | Adsorbed species undergo chemical reactions, transforming into solid film material (e.g., SiO₂). |
4. Surface Diffusion to Growth Sites | Species diffuse across the substrate to growth sites, ensuring uniform film thickness. |
5. Nucleation and Growth | Small clusters form and grow into a continuous film, controlled by temperature and reactant concentration. |
6. Desorption of By-Products | Gaseous by-products desorb and are transported away, maintaining film purity. |
7. Advantages of LPCVD | Better uniformity, higher purity, and improved step coverage compared to atmospheric pressure CVD. |
8. Applications | Used in semiconductor manufacturing for depositing silicon dioxide, silicon nitride, and polysilicon. |
Discover how LPCVD can enhance your manufacturing process—contact our experts today for more information!