The process of making biomass pellets involves several key steps, starting from raw material preparation to the final packaging of the pellets. Biomass pellets are a sustainable and efficient form of energy, typically made from organic materials like wood, agricultural residues, or other plant-based waste. The process begins with the collection and preparation of raw materials, followed by drying, grinding, pelletizing, cooling, and packaging. Each step is crucial to ensure the quality, durability, and energy efficiency of the final product. The pelletizing process compresses the biomass under high pressure and temperature, transforming it into dense, uniform pellets that are easy to transport and burn efficiently.
Key Points Explained:
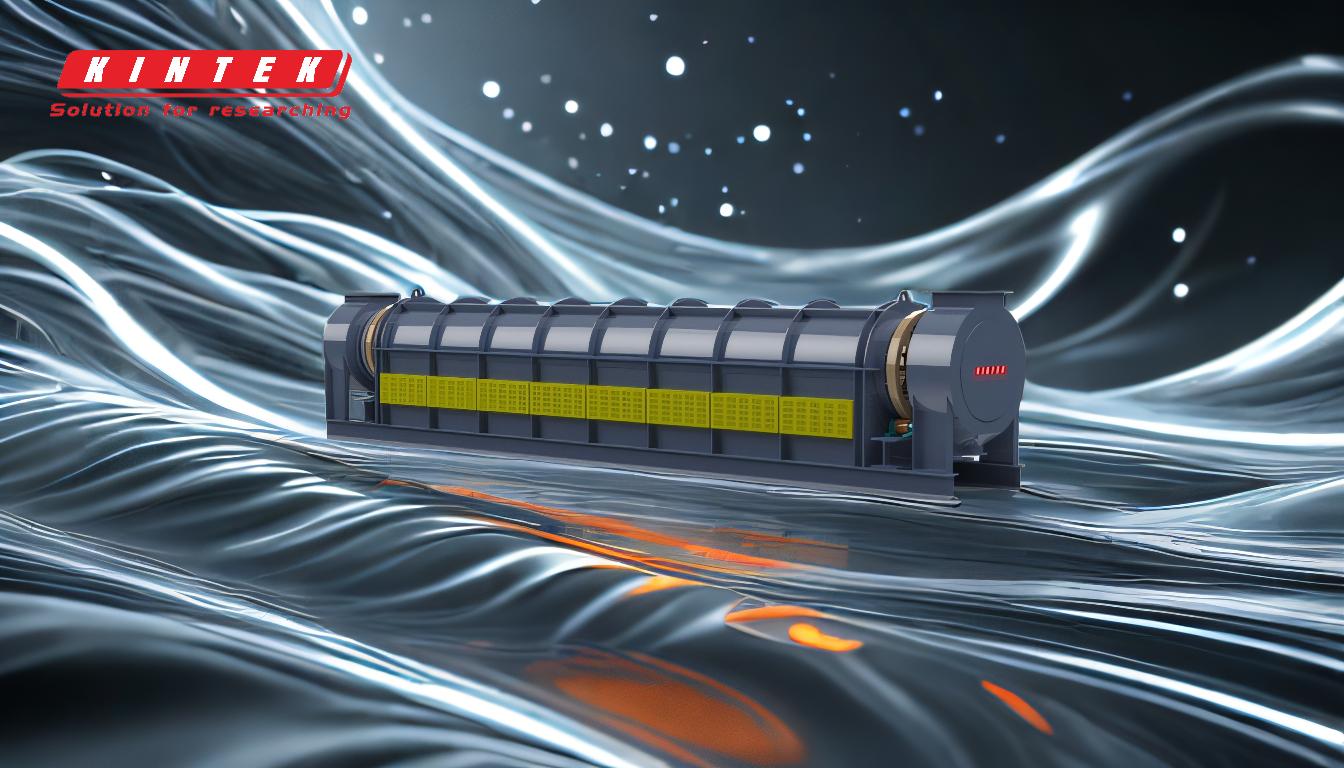
-
Raw Material Collection and Preparation:
- Biomass materials such as wood chips, sawdust, straw, or agricultural residues are collected.
- The raw materials are cleaned to remove impurities like dirt, stones, or metals.
- The size of the raw materials is reduced to ensure uniformity, which is critical for the pelletizing process.
-
Drying:
- The moisture content of the raw materials is reduced to an optimal level, typically around 10-15%.
- Excess moisture can hinder the pelletizing process and reduce the quality of the pellets.
- Industrial dryers, such as rotary or belt dryers, are used to achieve the desired moisture content.
-
Grinding:
- The dried materials are further ground into a fine powder using hammer mills or grinders.
- This step ensures that the particles are small and uniform, which is essential for creating high-quality pellets.
- The consistency of the ground material affects the density and durability of the final pellets.
-
Pelletizing:
- The ground biomass is fed into a pellet mill, where it is compressed under high pressure and temperature.
- The pellet mill typically consists of a die and rollers that force the biomass through small holes, shaping it into pellets.
- The heat generated during this process activates the natural lignin in the biomass, acting as a binder to hold the pellets together.
-
Cooling:
- The freshly made pellets are hot and soft, so they need to be cooled to harden and stabilize.
- Cooling is done using a pellet cooler, which reduces the temperature of the pellets and removes excess moisture.
- Proper cooling ensures that the pellets are durable and less prone to breaking during handling and transportation.
-
Screening and Packaging:
- The cooled pellets are screened to remove any fines or broken pieces, ensuring only high-quality pellets are packaged.
- The pellets are then packed into bags or stored in bulk, ready for distribution.
- Packaging is done using automated systems to ensure consistency and efficiency.
-
Quality Control:
- Throughout the process, quality control measures are implemented to ensure the pellets meet industry standards.
- Parameters such as pellet density, moisture content, and durability are monitored.
- High-quality pellets burn more efficiently and produce less ash, making them more desirable for energy production.
By following these steps, biomass pellets are produced as a sustainable and efficient energy source, suitable for heating, power generation, and other applications. The process is designed to maximize energy output while minimizing environmental impact, making biomass pellets a key component of renewable energy strategies.
Summary Table:
Step | Description |
---|---|
Raw Material Preparation | Collect and clean biomass materials like wood chips, sawdust, or agricultural residues. Reduce size for uniformity. |
Drying | Reduce moisture content to 10-15% using industrial dryers. |
Grinding | Grind dried materials into fine powder for consistent pellet quality. |
Pelletizing | Compress biomass under high pressure and temperature to form dense pellets. |
Cooling | Cool pellets to harden and stabilize them for durability. |
Screening and Packaging | Remove fines and package high-quality pellets for distribution. |
Quality Control | Monitor parameters like density, moisture, and durability to ensure standards. |
Ready to produce high-quality biomass pellets? Contact us today to learn more about our solutions!