Plasma sintering, specifically spark plasma sintering (SPS), is an advanced sintering technique that combines plasma activation, hot pressing, and resistance heating to achieve rapid densification of materials. The process involves the application of a pulsed direct current (DC) through a conductive die and the material, generating Joule heat and plasma discharge between particles. This localized heating activates and purifies particle surfaces, leading to rapid bonding and densification at lower temperatures compared to conventional sintering methods. The process is characterized by its ability to produce high-density materials with fine microstructures in a fraction of the time required by traditional sintering techniques.
Key Points Explained:
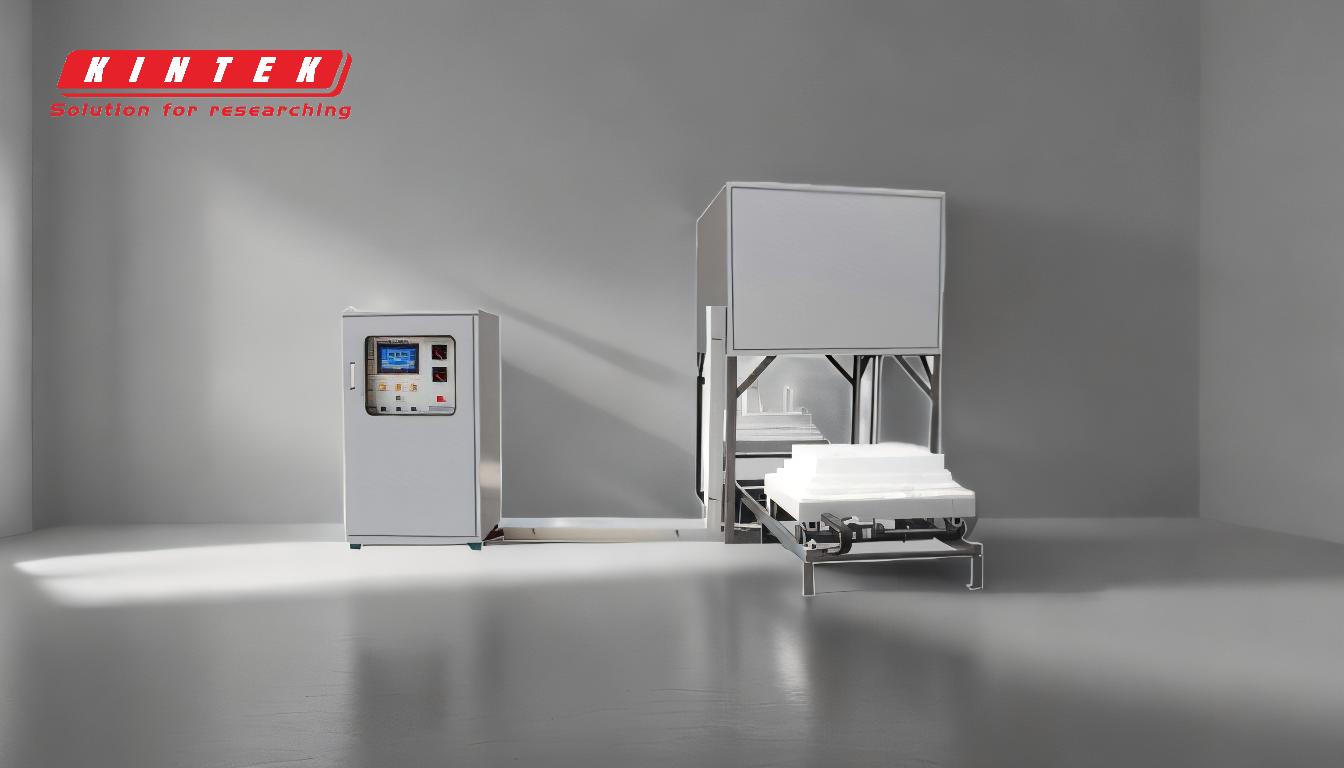
-
Integration of Plasma Activation, Hot Pressing, and Resistance Heating:
- SPS combines three key mechanisms: plasma activation, hot pressing, and resistance heating. The plasma activation occurs due to the discharge between powder particles, which momentarily heats the particle surfaces to several thousand degrees Celsius. This heating is uniformly distributed, purifying and activating the surfaces by vaporizing impurities.
- The hot pressing applies pressure to the powder compact, aiding in densification through plastic deformation.
- Resistance heating is generated by the Joule effect, where the electrical current passing through the material and die produces heat internally and externally.
-
Stages of the SPS Process:
- Preparation of the Powder Compact: The material is prepared in the form of a powder compact, which can be achieved through cold welding, 3D printing, or pressing tools. The compact is placed in a controlled atmosphere to ensure uniformity.
- Heating and Consolidation: The material is heated to just below its melting point using the spark plasma sintering furnace. This stage activates the martensitic crystalline microstructures and initiates particle bonding.
- Particle Merging: Under the combined effect of heat and pressure, the particles densify and merge. This process can be accelerated using liquid phase sintering (LPS), where a liquid phase forms at the grain boundaries, enhancing material flow and densification.
- Solidification: After the desired density is achieved, the material is cooled, allowing it to solidify into a single, unified mass with a fine-grained microstructure.
-
Advantages of SPS:
- Rapid Heating and Cooling Rates: SPS allows for very fast heating and cooling, reducing the overall processing time significantly.
- Lower Sintering Temperatures: The process achieves densification at temperatures several hundred degrees lower than conventional sintering, preserving the material's microstructure and properties.
- Enhanced Material Properties: The rapid sintering process results in materials with high density, fine grain size, and improved mechanical properties.
-
Applications of SPS:
- SPS is widely used in the fabrication of advanced ceramics, metals, and composites. It is particularly beneficial for materials that are difficult to sinter using conventional methods, such as nanostructured materials, functionally graded materials, and materials with high melting points.
-
Comparison with Other Sintering Techniques:
- Unlike traditional sintering methods, which rely solely on thermal energy, SPS utilizes electrical discharge and pressure to achieve densification. This results in a more efficient process with better control over the material's microstructure.
- Compared to hot pressing, SPS offers faster heating rates and lower sintering temperatures, making it a more energy-efficient and cost-effective method.
-
Mechanisms of SPS:
- Discharge Plasma: The plasma generated during SPS is a highly ionized gas with temperatures ranging from 4000 to 10999°C. This plasma is highly activated, promoting rapid surface reactions and bonding between particles.
- Joule Heating: The electrical current passing through the material and die generates heat internally, ensuring uniform heating throughout the sample.
- Pressure Application: The applied pressure aids in particle rearrangement and plastic deformation, enhancing densification.
In summary, spark plasma sintering is a highly efficient and versatile sintering technique that leverages plasma activation, resistance heating, and pressure to achieve rapid densification of materials. Its ability to operate at lower temperatures and shorter processing times makes it an attractive option for the fabrication of advanced materials with superior properties.
Summary Table:
Aspect | Details |
---|---|
Key Mechanisms | Plasma activation, hot pressing, and resistance heating |
Process Stages | Preparation, heating and consolidation, particle merging, solidification |
Advantages | Rapid heating/cooling, lower sintering temperatures, enhanced properties |
Applications | Advanced ceramics, metals, composites, nanostructured materials |
Comparison | More efficient than traditional sintering, faster than hot pressing |
Mechanisms | Discharge plasma, Joule heating, pressure application |
Ready to explore the benefits of spark plasma sintering for your materials? Contact us today to learn more!