A plastic pyrolysis plant is a facility designed to convert waste plastics into valuable products like fuel oil, carbon black, and syngas through a thermal decomposition process in the absence of oxygen. The process involves several key steps: preprocessing the plastic to meet size and moisture requirements, feeding it into a reactor, heating it to high temperatures (400-900°C), and then cooling and separating the resulting products. The oil gas produced is condensed into pyrolysis oil, while uncondensable gases are recycled to heat the reactor. Carbon black is collected after cooling, and the entire process is managed with safety and control systems to ensure efficiency and environmental compliance.
Key Points Explained:
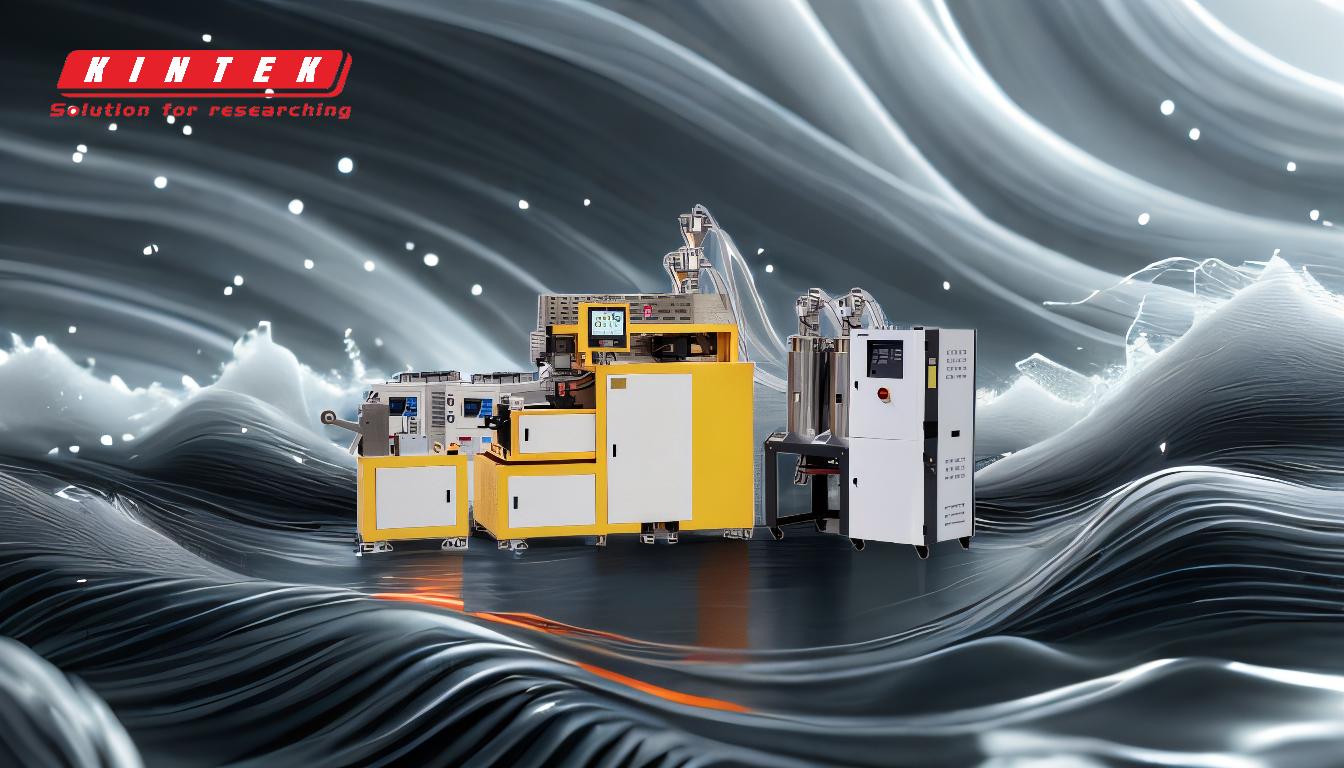
-
Preprocessing of Plastic Waste:
- Shredding: Plastic waste is shredded into smaller pieces to ensure uniformity and improve the efficiency of the pyrolysis process.
- Drying: The shredded plastic is dried to reduce moisture content, which can affect the quality of the pyrolysis oil.
- Separation: Non-plastic materials are separated to ensure that only plastic is fed into the reactor, enhancing the purity of the end products.
-
Feeding and Heating:
- Feeding: The preprocessed plastic is fed into the pyrolysis reactor. This is typically done using a conveyor system or a hopper.
- Heating: The reactor is heated to temperatures between 400-900°C in the absence of oxygen. This high-temperature environment causes the plastic to thermally decompose.
-
Pyrolysis Reaction:
- Thermal Decomposition: At high temperatures, the plastic molecules break down into smaller molecules, producing oil gas, carbon black, and syngas.
- Chemical Reactions: The process involves both chemical and physical reactions that transform the plastic waste into useful byproducts.
-
Cooling and Separation:
- Condensation: The oil gas produced is passed through a condensation system where it is cooled and converted into liquid pyrolysis oil.
- Gas Recycling: Uncondensable gases are recycled back into the reactor to maintain the heating process, making the system more energy-efficient.
- Carbon Black Collection: After the reactor cools down to below 40°C, carbon black is discharged and collected using a discharge device.
-
Product Refinement and Storage:
- Distillation and Purification: The pyrolysis oil may undergo further distillation and purification to improve its quality for various industrial applications.
- Storage: The final products, including pyrolysis oil, carbon black, and syngas, are stored in appropriate containers or tanks for dispatch or further use.
-
Safety and Control Systems:
- Monitoring: The entire process is monitored and controlled using advanced safety and control systems to ensure efficient operation and prevent accidents.
- Environmental Compliance: The plant is designed to minimize harmful emissions and comply with environmental regulations, making it a sustainable solution for plastic waste management.
By following these steps, a plastic pyrolysis plant effectively converts waste plastics into valuable resources, contributing to waste reduction and resource recovery.
Summary Table:
Step | Description |
---|---|
Preprocessing | Shredding, drying, and separating plastic waste for efficient pyrolysis. |
Feeding & Heating | Feeding preprocessed plastic into a reactor and heating to 400-900°C. |
Pyrolysis Reaction | Thermal decomposition breaks down plastic into oil gas, carbon black, and syngas. |
Cooling & Separation | Condensing oil gas into pyrolysis oil, recycling gases, and collecting carbon black. |
Refinement & Storage | Distilling and purifying pyrolysis oil, storing final products for use. |
Safety & Control | Monitoring and controlling the process for efficiency and environmental compliance. |
Transform your plastic waste into valuable resources—contact us today to learn more!