Physical Vapor Deposition (PVD) is a sophisticated process used to deposit thin films of material onto a substrate in a vacuum environment. The process involves several key steps: gasification of a solid precursor material, transportation of the gasified atoms to a reaction chamber, and deposition of these atoms onto the substrate to form a thin film. This method is widely used in various industries for creating high-performance coatings with excellent adhesion, uniformity, and durability.
Key Points Explained:
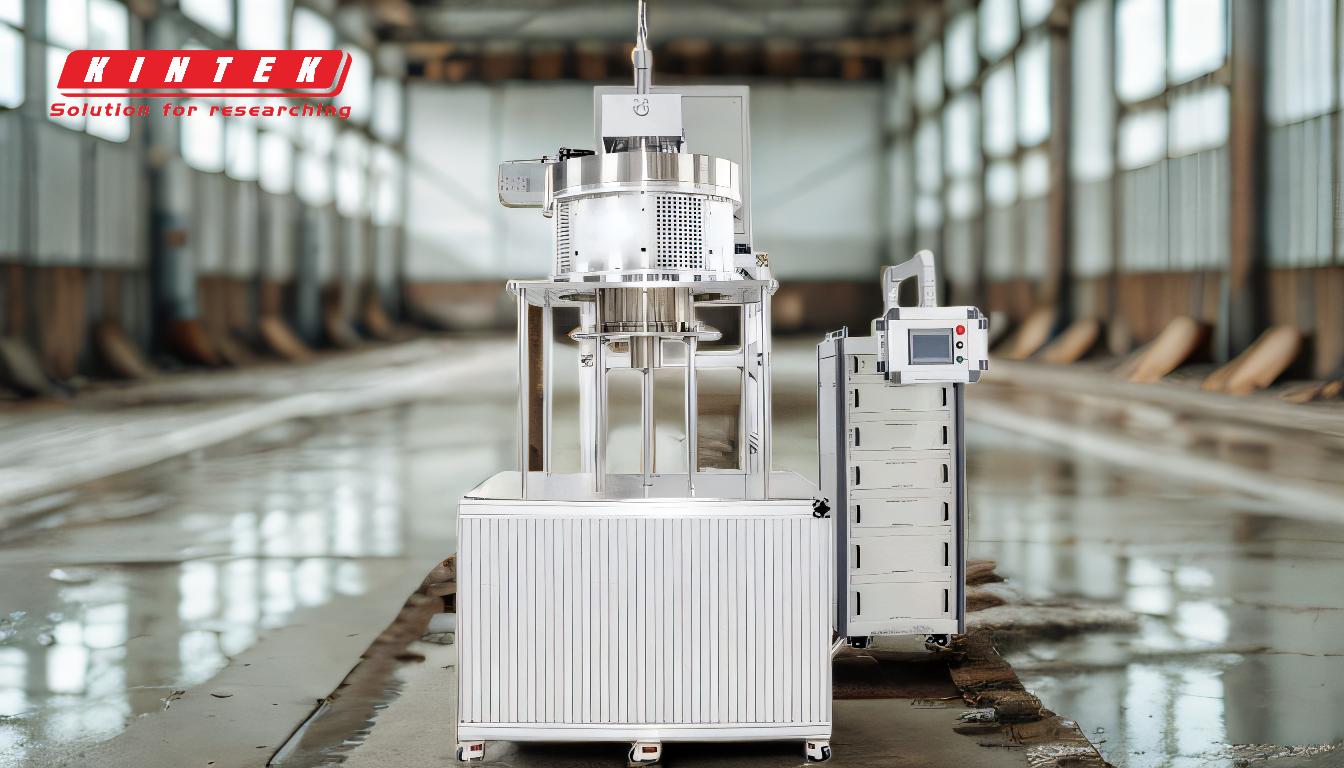
-
Gasification of the Precursor Material:
- The PVD process begins with the gasification of a solid precursor material. This is typically achieved using high-power electricity or a laser. The energy input causes the solid material to vaporize, forming a cloud of gas atoms. This step is crucial as it prepares the material for transportation to the substrate.
-
Transportation of Gasified Atoms:
- Once the precursor material is gasified, the atoms are transported to a reaction chamber where the substrate is located. This transportation occurs in a vacuum environment, which ensures that the atoms can move freely without interference from air molecules. The vacuum also helps in maintaining the purity of the deposited material.
-
Deposition onto the Substrate:
- In the reaction chamber, the gasified atoms adhere to the surface of the substrate. This deposition process is controlled to ensure that the atoms form a uniform thin film. The substrate is often heated to facilitate better adhesion and to improve the quality of the deposited film. The result is a thin, durable coating that can enhance the substrate's properties, such as hardness, corrosion resistance, or electrical conductivity.
-
Formation of Plasma:
- In some PVD processes, plasma is created from a gas, typically using an inductively coupled plasma (ICP). The gas is ionized, and high-energy electrons collide with gas molecules, causing them to dissociate into atoms. These atoms are then deposited onto the substrate, where they condense to form a thin film. This step is particularly important in processes where reactive gases are used to form compounds with the vaporized material.
-
Introduction of Reactive Gaseous Species:
- In certain PVD techniques, a reactive gaseous species is introduced into the reaction chamber. This gas reacts with the vaporized material to form a compound, which is then deposited onto the substrate. This method is used to create coatings with specific chemical compositions and properties, such as nitrides or oxides.
-
Annealing or Heat Treatment:
- After the deposition process, the thin film may undergo annealing or heat treatment. This step helps to improve the film's mechanical properties, such as hardness and adhesion, by allowing the atoms to rearrange into a more stable crystalline structure. The heat treatment process is carefully controlled to avoid damaging the substrate or the deposited film.
-
Analysis and Process Modification:
- The final step in the PVD process involves analyzing the properties of the deposited film. This analysis can include measurements of thickness, uniformity, adhesion, and other relevant properties. Based on the results, the deposition process may be modified to improve the quality of the film or to achieve specific performance characteristics.
In summary, the PVD deposition process is a multi-step procedure that involves the gasification of a precursor material, transportation of the gasified atoms to a substrate, and deposition of these atoms to form a thin film. The process is highly controlled and can be tailored to produce coatings with specific properties, making it a valuable technique in various industrial applications. For more information on related processes, you can explore the chemical vapor deposition system.
Summary Table:
Step | Description |
---|---|
1. Gasification | Solid precursor material is vaporized using high-power electricity or a laser. |
2. Transportation | Gasified atoms are transported to the reaction chamber in a vacuum environment. |
3. Deposition | Atoms adhere to the substrate, forming a uniform thin film. |
4. Plasma Formation | Plasma is created from gas, ionizing atoms for deposition. |
5. Reactive Gaseous Species | Reactive gases form compounds with vaporized material for specific coatings. |
6. Annealing/Heat Treatment | Improves film properties like hardness and adhesion through controlled heating. |
7. Analysis & Modification | Film properties are analyzed, and the process is refined for optimal results. |
Discover how PVD deposition can enhance your materials—contact our experts today for tailored solutions!