The process of PVD (Physical Vapor Deposition) evaporation involves converting a solid or liquid material into a vapor phase by applying heat in a high-vacuum environment. This vaporized material then diffuses through the vacuum and condenses onto a substrate, forming a thin film. The process is highly controllable, allowing for precise deposition of elements, alloys, or compounds, with film thicknesses ranging from nanometers to micrometers. Techniques like Cathodic Arc Evaporation and Multi-Source Evaporation are used to achieve specific film compositions and properties. The high-vacuum environment ensures minimal interference from other gas molecules, resulting in high-purity coatings.
Key Points Explained:
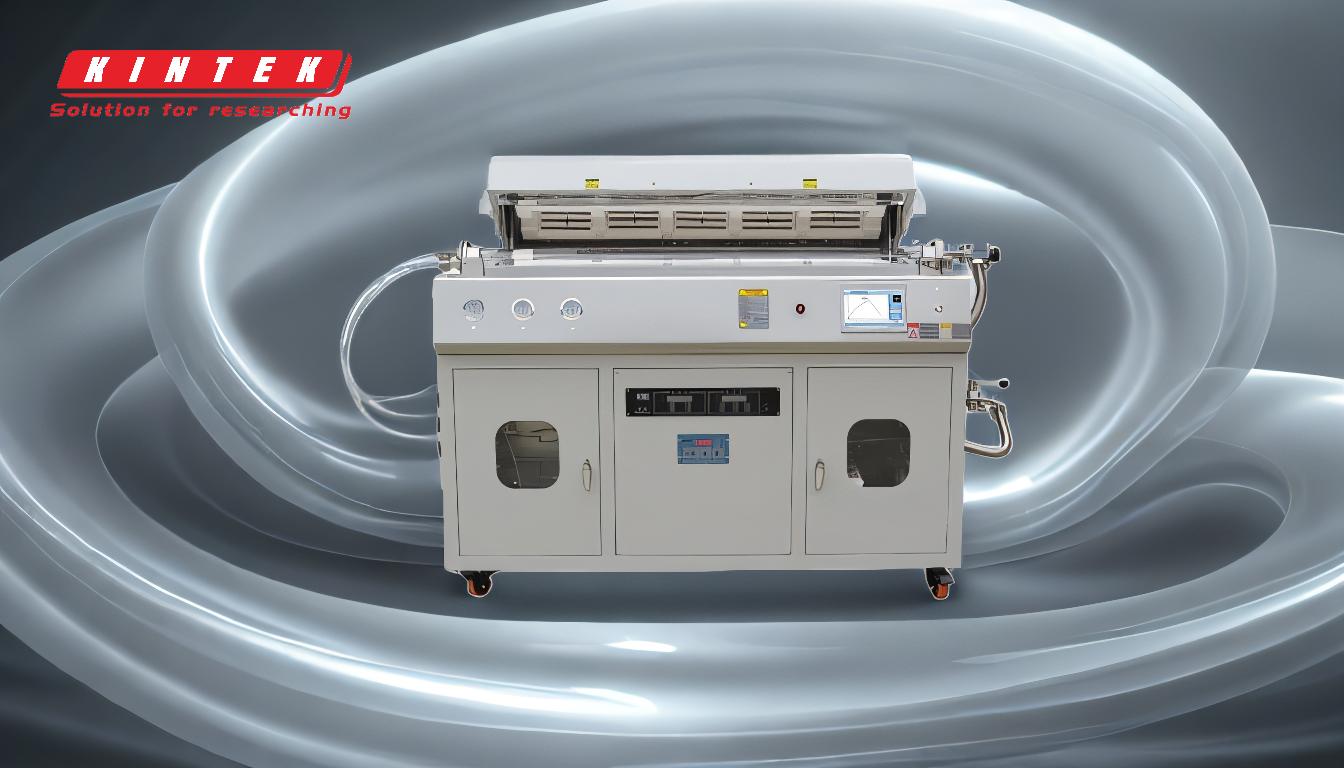
-
Material Vaporization:
- In PVD evaporation, the source material (solid or liquid) is heated until it reaches its vaporization point. This can be achieved through methods like resistive heating, electron beam heating, or laser heating. The high-vacuum environment ensures that the vaporized atoms or molecules travel to the substrate without significant collisions with other gas molecules, maintaining the purity of the deposition.
-
Transport Through Vacuum:
- Once vaporized, the material travels through the vacuum chamber to the substrate. The vacuum minimizes the presence of other gases, reducing contamination and ensuring that the vaporized material reaches the substrate in a controlled manner. This step is critical for achieving uniform and high-quality thin films.
-
Condensation on Substrate:
- Upon reaching the substrate, the vaporized material condenses, forming a thin film. The substrate's temperature, surface condition, and orientation can influence the film's adhesion, uniformity, and microstructure. Proper control of these parameters is essential for achieving the desired film properties.
-
Types of PVD Evaporation Techniques:
- Cathodic Arc Evaporation: In this method, an electric arc is used to evaporate the target material. The arc creates a highly ionized plasma, which is then directed toward the substrate. This technique is known for producing dense and adherent coatings, often used in applications requiring high wear resistance.
- Multi-Source Evaporation: This technique involves using multiple evaporation sources simultaneously. By controlling the strength and composition of each source, it is possible to create complex film compositions, such as alloys or multilayered structures. This method is particularly useful for applications requiring tailored material properties.
-
Advantages of PVD Evaporation:
- High Purity: The high-vacuum environment ensures minimal contamination, resulting in high-purity coatings.
- Precision Control: The process allows for precise control over film thickness, composition, and microstructure.
- Versatility: PVD evaporation can deposit a wide range of materials, including metals, ceramics, and composites, making it suitable for various applications in electronics, optics, and coatings.
-
Applications of PVD Evaporation:
- Electronics: Used for depositing conductive and insulating layers in semiconductor devices.
- Optics: Applied in the production of anti-reflective coatings, mirrors, and optical filters.
- Coatings: Utilized for wear-resistant, corrosion-resistant, and decorative coatings on tools, automotive parts, and consumer goods.
In summary, PVD evaporation is a versatile and precise method for depositing thin films, offering high purity and control over film properties. Techniques like Cathodic Arc Evaporation and Multi-Source Evaporation further enhance its capabilities, making it a valuable process in various industries.
Summary Table:
Key Aspect | Details |
---|---|
Material Vaporization | Solid/liquid material is heated to vaporize in a high-vacuum environment. |
Transport Through Vacuum | Vaporized material travels through vacuum, minimizing contamination. |
Condensation on Substrate | Material condenses on the substrate, forming a thin film. |
Techniques | Cathodic Arc Evaporation, Multi-Source Evaporation. |
Advantages | High purity, precision control, and versatility. |
Applications | Electronics, optics, and wear-resistant coatings. |
Discover how PVD evaporation can enhance your projects—contact our experts today for more information!