Physical Vapor Deposition (PVD) is a vacuum-based thin-film coating process that involves the condensation of a material vapor onto a substrate to form a thin, durable layer. The process is carried out under high vacuum conditions and at relatively low temperatures, making it suitable for a wide range of applications. PVD involves several key steps, including the vaporization of the coating material, the migration of atoms or molecules, and the deposition of these particles onto the substrate. The process can include reactive gases to form compounds, and it often utilizes plasma to excite the material into a vapor state. The result is a high-quality, thin coating with excellent adhesion and uniformity.
Key Points Explained:
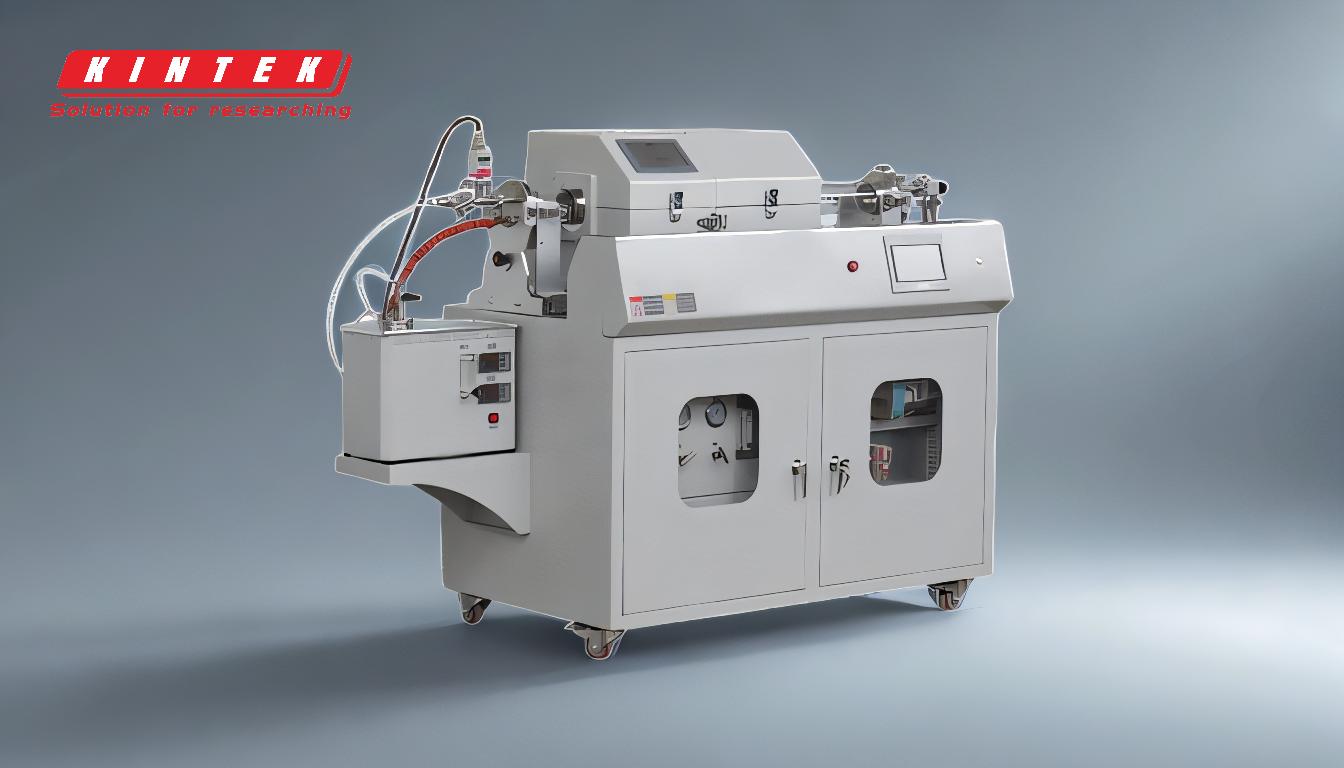
-
High Vacuum Environment:
- PVD is performed in a high vacuum environment to minimize contamination and ensure a clean deposition process.
- The low pressure helps in the efficient vaporization and migration of the coating material.
-
Vaporization of Coating Material:
- The solid precursor material is gasified using high-power electricity, a laser, or other energy sources.
- This step transforms the solid material into a vapor, which is essential for the subsequent deposition process.
-
Formation of Plasma:
- Plasma is often created from a gas using methods like inductively coupled plasma (ICP).
- The plasma excites the gas molecules, causing them to dissociate into atoms, which are then available for deposition.
-
Introduction of Reactive Gases:
- Reactive gases can be introduced into the chamber to form compounds with the vaporized material.
- This step is crucial for creating specific types of coatings, such as nitrides or oxides, depending on the desired properties.
-
Migration of Atoms or Molecules:
- The vaporized atoms or molecules migrate towards the substrate.
- During this migration, collisions and reactions can occur, especially if reactive gases are present, leading to the formation of compound coatings.
-
Deposition onto Substrate:
- The atoms or molecules condense onto the substrate, forming a thin, uniform layer.
- The substrate is typically at a lower temperature, which aids in the condensation process and ensures good adhesion of the coating.
-
Formation of Thin Film:
- The final step results in the formation of a thin film on the substrate.
- This film can have various properties, such as hardness, corrosion resistance, or optical characteristics, depending on the materials and processes used.
-
Low-Temperature Process:
- PVD is conducted at comparatively low temperatures, which is beneficial for substrates that are sensitive to high temperatures.
- This makes PVD suitable for a wide range of materials and applications, including electronics, optics, and decorative coatings.
-
Versatility and Applications:
- PVD is versatile and can be used to deposit a wide variety of materials, including metals, ceramics, and composites.
- It is widely used in industries such as aerospace, automotive, medical devices, and consumer electronics for applications requiring durable, high-performance coatings.
-
Quality and Uniformity:
- The PVD process results in coatings with excellent adhesion, uniformity, and quality.
- The high vacuum and controlled environment ensure that the coatings are free from defects and have consistent properties across the substrate.
In summary, the PVD manufacturing process is a sophisticated and highly controlled method for depositing thin films onto substrates. It involves several critical steps, including vaporization, plasma formation, reactive gas introduction, and deposition, all carried out under high vacuum and low-temperature conditions. This process is versatile, producing high-quality coatings with excellent adhesion and uniformity, suitable for a wide range of industrial applications.
Summary Table:
Key Aspect | Description |
---|---|
High Vacuum Environment | Ensures minimal contamination and efficient vaporization of coating materials. |
Vaporization | Solid material is gasified using high-power electricity or lasers. |
Plasma Formation | Excites gas molecules into atoms for deposition. |
Reactive Gases | Introduced to form compound coatings like nitrides or oxides. |
Migration & Deposition | Vaporized atoms condense onto the substrate, forming a thin, uniform layer. |
Low-Temperature Process | Suitable for temperature-sensitive substrates. |
Versatility | Deposits metals, ceramics, and composites for diverse applications. |
Quality & Uniformity | Produces defect-free, high-adhesion coatings with consistent properties. |
Discover how PVD can enhance your product performance—contact our experts today!