Pyrolysis is a thermochemical decomposition process where organic materials are heated to high temperatures (typically 200-900°C) in the absence of oxygen, breaking them down into smaller molecules. This process yields three main products: gases (syngas), liquids (bio-oil), and solids (bio-char). The exact composition of these products depends on the feedstock and process conditions. Pyrolysis is widely used in labs and industries to convert biomass, plastics, and other waste materials into valuable outputs such as fuels and chemicals. The process involves several steps, including feedstock preparation, heating in a controlled environment, and separation of the resulting products.
Key Points Explained:
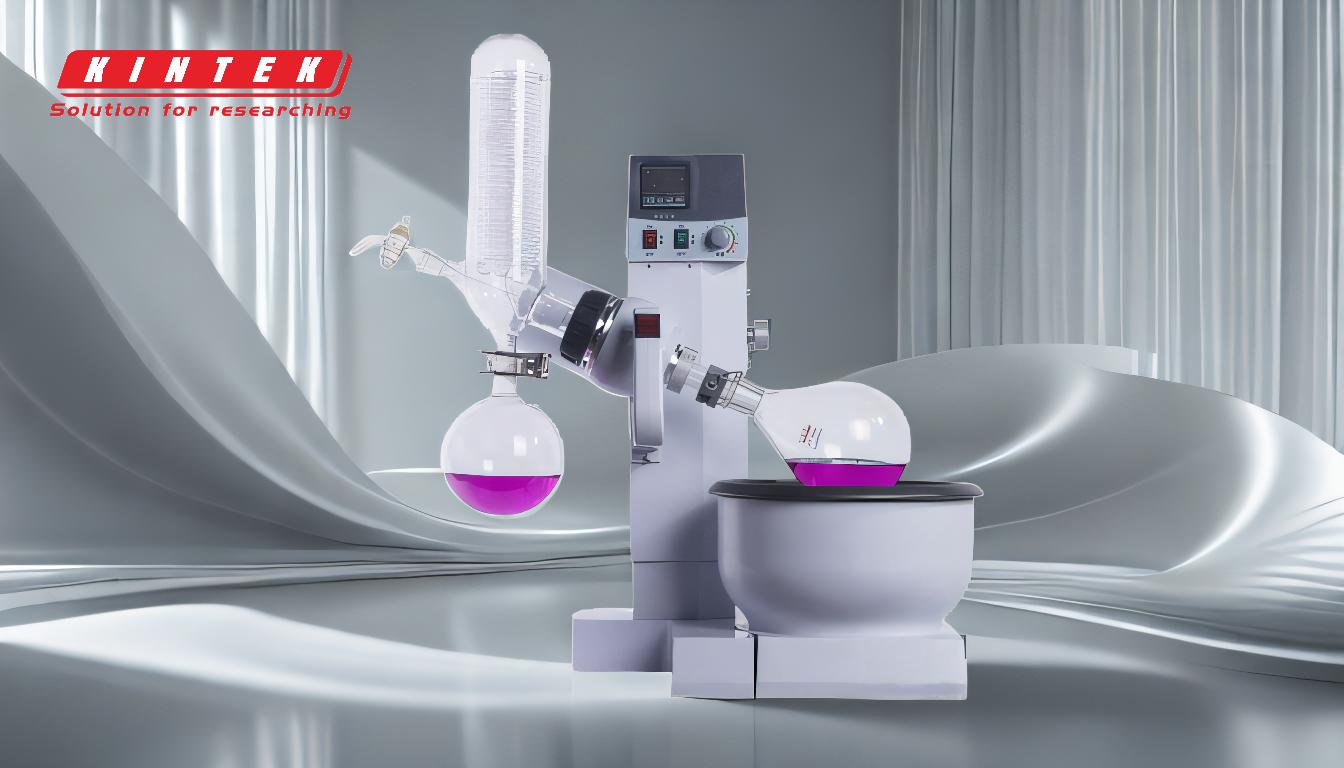
-
Definition and Purpose of Pyrolysis:
- Pyrolysis is a thermochemical decomposition process that occurs when organic materials are heated in the absence of oxygen.
- The purpose of pyrolysis is to break down complex organic materials into simpler molecules, producing gases, liquids, and solids that can be used as fuels, chemicals, or other valuable products.
-
Key Steps in the Pyrolysis Process:
-
Feedstock Preparation:
- The material to be pyrolyzed (e.g., biomass, plastic waste) is first pre-treated to remove impurities.
- The feedstock is then ground or shredded to the required size to ensure uniform heating and efficient decomposition.
-
Loading and Heating:
- The prepared feedstock is loaded into a pyrolysis chamber, often with the addition of a catalyst to enhance the reaction.
- The chamber is heated to a temperature range of 200-900°C, depending on the material and desired products.
-
Decomposition:
- As the material is heated, it undergoes thermal decomposition, breaking down into smaller molecules.
- This process generates gases (syngas), liquids (bio-oil), and solids (bio-char).
-
Product Separation:
- The gases and vapors produced are condensed to form liquid bio-oil.
- The remaining solids (bio-char) settle at the bottom of the chamber.
- Non-condensable gases (syngas) can be recycled back into the system to provide heat for the process.
-
Feedstock Preparation:
-
Types of Pyrolysis:
-
Slow Pyrolysis:
- Involves heating the material at lower temperatures (300-500°C) with a longer residence time.
- Produces more bio-char and less bio-oil.
-
Fast Pyrolysis:
- Involves rapid heating at higher temperatures (500-900°C) with a short residence time.
- Produces more bio-oil and less bio-char.
-
Flash Pyrolysis:
- A variant of fast pyrolysis with even shorter residence times and higher heating rates.
- Maximizes the production of bio-oil.
-
Slow Pyrolysis:
-
Products of Pyrolysis:
-
Syngas:
- A mixture of gases, including hydrogen, carbon monoxide, and methane.
- Can be used as a fuel or further processed into chemicals.
-
Bio-oil:
- A liquid mixture of water and volatile organic compounds.
- Can be refined and used as a fuel or feedstock for chemical production.
-
Bio-char:
- A carbon-rich solid residue.
- Can be used as a soil amendment, in carbon sequestration, or as a fuel.
-
Syngas:
-
Applications of Pyrolysis:
-
Waste Management:
- Pyrolysis is used to convert plastic waste, tires, and other non-biodegradable materials into useful products, reducing landfill waste.
-
Energy Production:
- The syngas and bio-oil produced can be used as alternative fuels, reducing reliance on fossil fuels.
-
Chemical Production:
- Bio-oil can be further refined to produce chemicals and other valuable substances.
-
Soil Improvement:
- Bio-char can be used to improve soil fertility and sequester carbon, contributing to sustainable agriculture.
-
Waste Management:
-
Challenges and Considerations:
-
Energy Intensity:
- Pyrolysis is an energy-intensive process, requiring significant heat input to achieve the necessary temperatures.
-
Process Control:
- Precise control of temperature, heating rate, and residence time is crucial to optimize product yields and quality.
-
Feedstock Variability:
- The composition and quality of the feedstock can significantly affect the pyrolysis process and the properties of the resulting products.
-
Environmental Impact:
- While pyrolysis can reduce waste and produce valuable products, it must be managed carefully to minimize emissions and other environmental impacts.
-
Energy Intensity:
-
Laboratory-Scale Pyrolysis:
- In a lab setting, pyrolysis is often conducted in small-scale reactors to study the process and optimize conditions.
- Lab experiments allow for precise control of variables such as temperature, heating rate, and feedstock composition.
- The results from lab-scale pyrolysis can be scaled up for industrial applications.
By understanding the pyrolysis process and its key steps, researchers and engineers can optimize the conditions to produce desired products efficiently. This process not only helps in waste management but also contributes to the production of renewable energy and valuable chemicals, making it a crucial technology in the transition to a more sustainable future.
Summary Table:
Aspect | Details |
---|---|
Definition | Thermochemical decomposition of organic materials in the absence of oxygen. |
Temperature Range | 200-900°C |
Main Products | Syngas, bio-oil, bio-char |
Applications | Waste management, energy production, chemical synthesis, soil improvement |
Types of Pyrolysis | Slow, fast, flash |
Challenges | Energy intensity, process control, feedstock variability, environmental impact |
Discover how pyrolysis can transform waste into valuable resources—contact our experts today!