Pyrolysis is a thermochemical process that converts biomass into biochar, bio-oil, and syngas by heating organic materials in the absence of oxygen. The process involves several stages, including pre-treatment of biomass, pyrolysis under controlled temperature and residence time, and post-treatment of the resulting products. Slow pyrolysis, characterized by lower temperatures and longer residence times, is particularly effective for producing biochar. The process is energy-intensive but can be self-sustaining by utilizing the gaseous byproducts for heat generation. Biochar has applications in agriculture, carbon sequestration, and as a renewable energy source, making pyrolysis a valuable technology for sustainable waste management and resource recovery.
Key Points Explained:
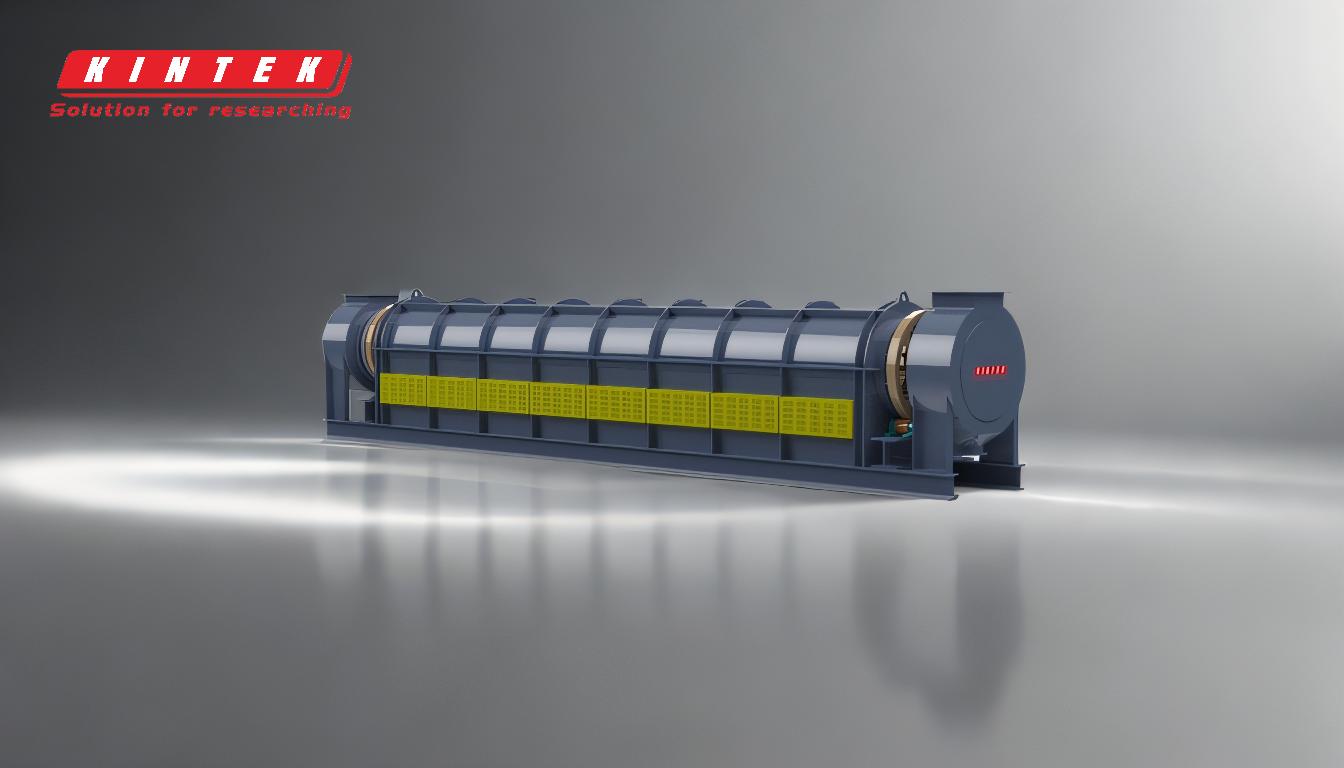
-
Definition and Purpose of Pyrolysis:
- Pyrolysis is a thermochemical decomposition process that converts biomass into biochar, bio-oil, and syngas in the absence of oxygen.
- The primary goal is to produce biochar, a stable form of carbon that can be used for soil amendment, carbon sequestration, and renewable energy.
-
Types of Pyrolysis:
- Slow Pyrolysis: Operates at lower temperatures (around 400 °C) with longer residence times, favoring biochar production.
- Fast Pyrolysis: Operates at higher temperatures (500-900 °C) with shorter residence times, favoring bio-oil production.
- Gasification: A related process that produces syngas and minimal biochar.
-
Steps in the Pyrolysis Process:
-
Pre-treatment:
- Biomass is dried and mechanically comminuted (crushed or ground) to ensure uniform heating and efficient pyrolysis.
-
Pyrolysis:
- The pre-treated biomass is heated in a pyrolysis chamber to temperatures between 200-900 °C, depending on the desired products.
- In slow pyrolysis, temperatures around 400 °C are maintained for several hours to maximize biochar yield.
-
Post-treatment:
- The biochar is cooled and discharged from the reactor.
- Exhaust gases are cleaned (de-dusted) to reduce harmful emissions.
-
Pre-treatment:
-
Product Composition:
- Biochar: A solid product rich in carbon, used for soil improvement and carbon sequestration.
- Bio-oil: A liquid product that can be refined for use as fuel or chemical feedstock.
- Syngas: A gaseous mixture of hydrogen, carbon monoxide, and methane, used for heat generation or as a fuel.
-
Energy Requirements and Sustainability:
- Pyrolysis is energy-intensive, requiring significant heat input to reach the necessary temperatures.
- The process can be partially self-sustaining by utilizing the syngas produced during pyrolysis to generate heat.
-
Applications of Biochar:
- Agriculture: Improves soil fertility, water retention, and microbial activity.
- Carbon Sequestration: Reduces greenhouse gas emissions by locking carbon in a stable form.
- Renewable Energy: Can be used as a fuel source or converted into activated carbon for filtration.
-
Challenges and Considerations:
- Feedstock Variability: The composition and quality of biomass can affect the pyrolysis process and product yield.
- Process Optimization: Requires precise control of temperature, residence time, and heating rate to maximize desired product yields.
- Environmental Impact: Proper management of exhaust gases and byproducts is essential to minimize pollution.
-
Economic and Environmental Benefits:
- Waste Reduction: Converts agricultural, forestry, and municipal waste into valuable products.
- Circular Economy: Supports the reuse and recycling of organic materials, reducing reliance on fossil fuels.
- Climate Mitigation: Biochar production contributes to carbon sequestration, helping to mitigate climate change.
By understanding the pyrolysis process and its key components, stakeholders can better evaluate its potential for sustainable biochar production and its broader applications in environmental and economic contexts.
Summary Table:
Aspect | Details |
---|---|
Definition | Thermochemical process converting biomass into biochar, bio-oil, and syngas. |
Types of Pyrolysis | Slow (400°C, biochar), Fast (500-900°C, bio-oil), Gasification (syngas). |
Process Steps | Pre-treatment, pyrolysis, post-treatment. |
Products | Biochar (soil improvement), bio-oil (fuel), syngas (heat generation). |
Applications | Agriculture, carbon sequestration, renewable energy. |
Challenges | Feedstock variability, process optimization, environmental impact. |
Benefits | Waste reduction, circular economy, climate mitigation. |
Discover how pyrolysis can transform your biomass into sustainable resources—contact us today for expert guidance!