Sintered metal manufacturing is a multi-step process that transforms powdered metal into solid, durable components. It begins with the selection of a metal powder composition, which is then compacted under high pressure to form a "green" part. This part is subsequently sintered in a furnace at high temperatures, allowing the particles to bond and achieve structural integrity. Post-sintering, the part may undergo additional machining or assembly processes to meet specific requirements. The process is widely used in industries requiring high precision and material efficiency, such as automotive, aerospace, and medical devices.
Key Points Explained:
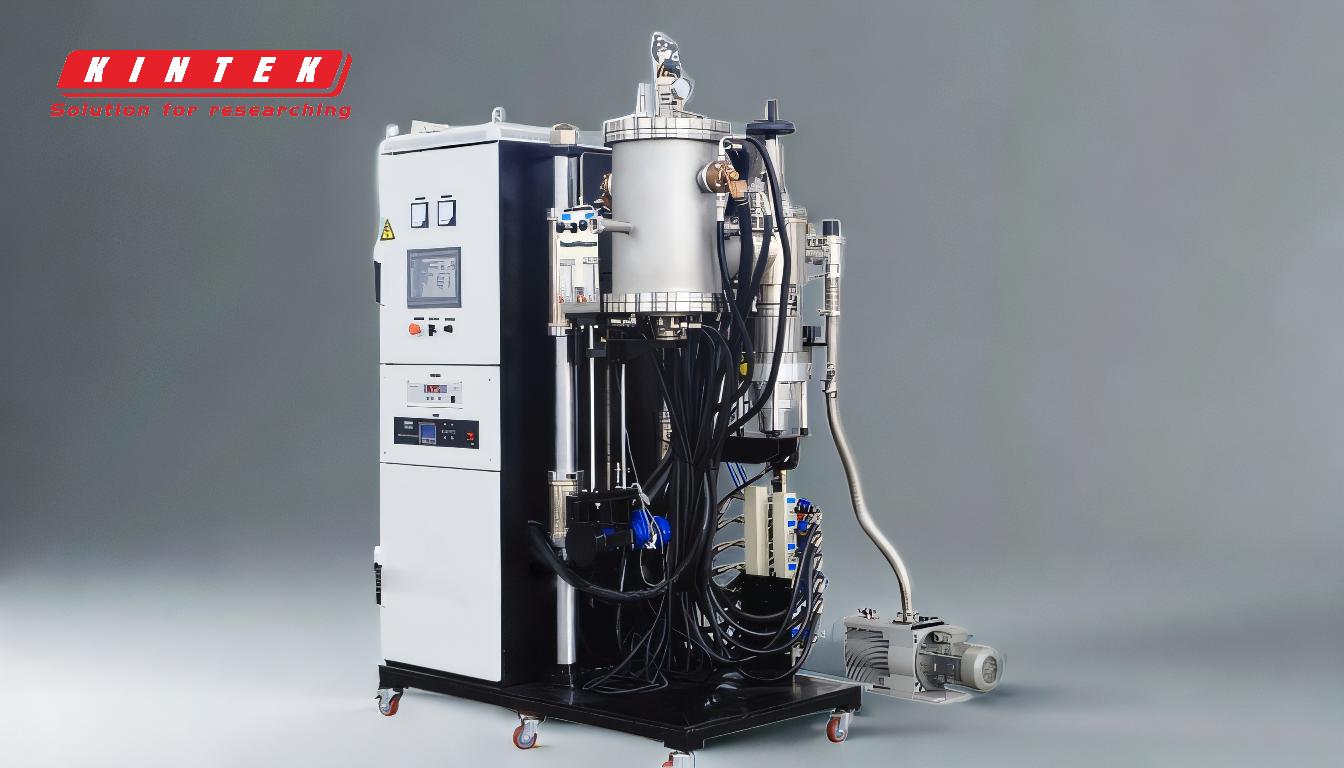
-
Powder Composition Selection:
- The process begins with choosing the appropriate metal powder composition. Common metals used include iron, nickel, molybdenum, and copper. Lubricants may also be added to facilitate compaction.
- The choice of materials depends on the desired properties of the final product, such as strength, hardness, and thermal conductivity.
-
Compaction:
- The selected metal powder is placed into a mold or die, often at room temperature but sometimes preheated.
- High pressure is applied to compact the powder, forming a "green" part. This part has initial strength but is still fragile and porous.
- The compaction process ensures the powder particles are closely packed, which is crucial for achieving the desired shape and density.
-
Sintering:
- The green part is transferred to a sintering furnace, where it is heated to a specific temperature below the melting point of the metal.
- During sintering, several physical and chemical changes occur:
- Removal of Lubricants: Any lubricants added during compaction are burned off.
- Reduction of Oxides: Metal oxides are reduced, enhancing the purity and bonding of the particles.
- Particle Bonding: The metal particles begin to bond at their contact points, leading to densification and increased strength.
- Cooling: After sintering, the part is cooled, solidifying the bonds and achieving the final structural integrity.
-
Post-Sintering Processes:
- Machining: Depending on the application, the sintered part may undergo additional machining. This can include precision cutting, drilling, or grinding, often using diamond tools or ultrasonic methods to achieve the required tolerances and surface finish.
- Assembly: In some cases, sintered parts are assembled with other components. This may involve metallization (applying a metal coating) and brazing (joining with a filler metal) to create complex assemblies.
-
Quality Control and Final Inspection:
- Throughout the process, quality control measures are implemented to ensure the final product meets specifications. This includes checking dimensions, density, and mechanical properties.
- Final inspection may involve non-destructive testing methods such as X-ray or ultrasonic inspection to detect any internal defects.
-
Applications and Advantages:
- Sintered metal parts are used in a wide range of industries due to their high precision, material efficiency, and ability to produce complex shapes.
- The process is particularly advantageous for manufacturing components that require high strength-to-weight ratios, such as gears, bearings, and filters.
By following these steps, sintered metal manufacturing produces components that are both durable and precise, making it a vital process in modern engineering and manufacturing.
Summary Table:
Step | Description |
---|---|
Powder Composition | Choose metal powders (e.g., iron, nickel) and lubricants for desired properties. |
Compaction | Compact powder under high pressure to form a fragile "green" part. |
Sintering | Heat the green part in a furnace to bond particles and achieve strength. |
Post-Sintering | Machine or assemble parts to meet specific requirements. |
Quality Control | Inspect dimensions, density, and properties to ensure quality. |
Applications | Used in automotive, aerospace, and medical devices for precision components. |
Ready to explore sintered metal solutions for your industry? Contact our experts today!