Sintering coating is a specialized process used to create dense, durable, and functional coatings on substrates by fusing particles together without melting the base material. This process involves preparing a powder mixture, compacting it into the desired shape, and applying heat and pressure to bond the particles. The result is a cohesive, low-porosity coating with enhanced mechanical properties. Sintering is widely used in industries like powder metallurgy, ceramics, and additive manufacturing to produce coatings with high strength, wear resistance, and thermal stability. Below, the key steps and principles of the sintering coating process are explained in detail.
Key Points Explained:
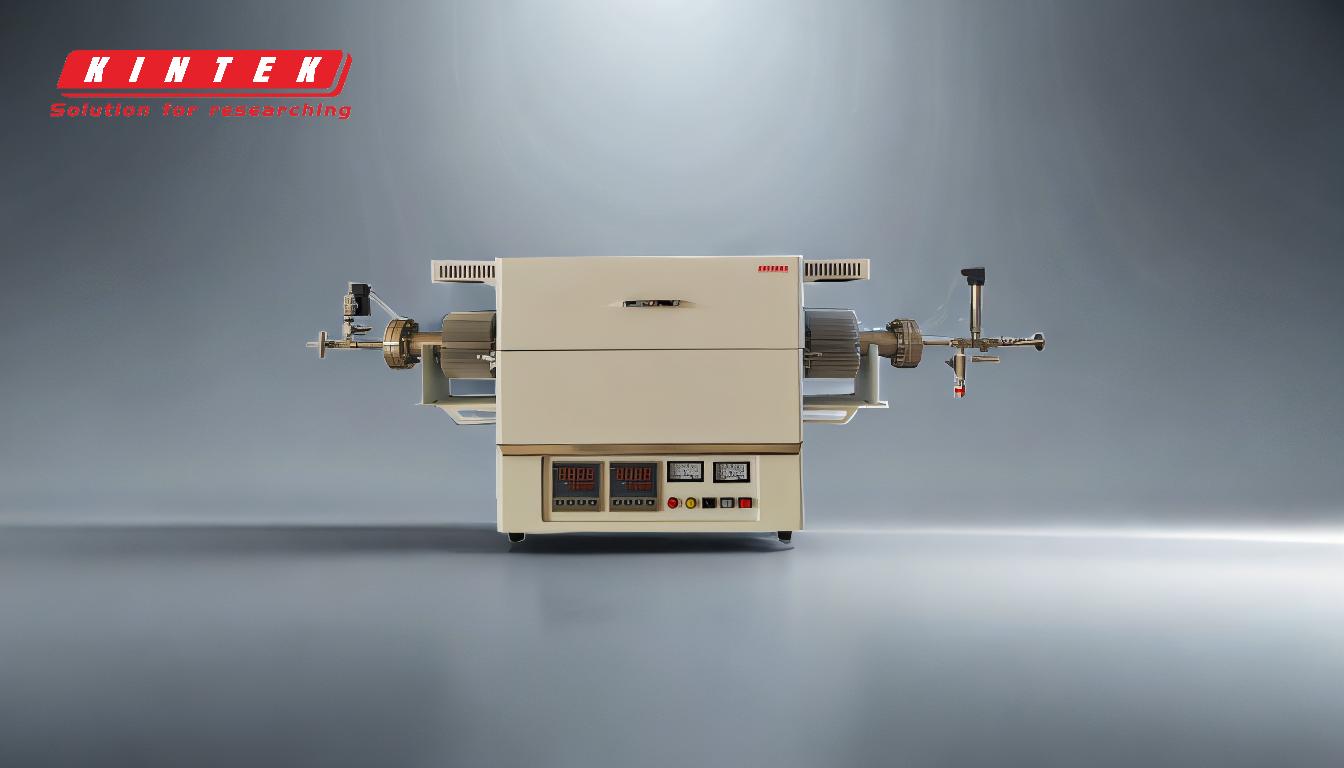
-
Preparation of the Powder Mixture
- The process begins with the preparation of a powder mixture, which typically includes the primary material (e.g., metal, ceramic, or plastic) and a bonding agent (e.g., wax or polymer).
- The bonding agent helps the powder particles adhere to each other during the initial shaping stage.
- The powder mixture is often tailored to achieve specific properties in the final coating, such as hardness, thermal conductivity, or corrosion resistance.
-
Compaction and Shaping
- The powder mixture is compacted into the desired shape using methods like pressing tools, cold welds, or 3D-printed lasers.
- This step ensures the powder particles are densely packed and uniformly distributed, which is critical for achieving a homogeneous coating.
- Compaction is typically performed in a controlled atmosphere to prevent contamination and oxidation.
-
Heating and Consolidation
- The compacted powder is heated to a temperature just below the melting point of the primary material.
- This heating activates the diffusion of atoms across particle boundaries, causing the particles to merge and densify.
- In some cases, liquid phase sintering (LPS) is used, where a secondary material with a lower melting point melts and fills the gaps between particles, accelerating the bonding process.
-
Removal of the Bonding Agent
- As the temperature rises, the bonding agent evaporates or burns away, leaving behind a porous structure of the primary material.
- This step is crucial for ensuring that the final coating is free of impurities and has a uniform composition.
-
Particle Fusion and Densification
- At higher temperatures, the primary particles begin to fuse at their surfaces, forming a solid mass with reduced porosity.
- The fusion process is driven by atomic diffusion, which strengthens the bonds between particles and enhances the coating's mechanical properties.
- The result is a dense, cohesive coating that adheres firmly to the substrate.
-
Cooling and Solidification
- After the fusion process is complete, the material is allowed to cool and solidify into a unified mass.
- Controlled cooling is essential to prevent thermal stresses and ensure the coating retains its desired properties.
- The final product is a hard, durable coating with improved strength, wear resistance, and thermal stability.
-
Applications of Sintering Coatings
- Sintering coatings are widely used in industries such as aerospace, automotive, and electronics for applications requiring high-performance materials.
- Examples include wear-resistant coatings for cutting tools, thermal barrier coatings for engine components, and corrosion-resistant coatings for industrial equipment.
- The process is also used in additive manufacturing to create complex, high-strength parts with precise geometries.
-
Advantages of Sintering Coatings
- The sintering process allows for the creation of coatings with tailored properties, such as hardness, porosity, and thermal conductivity.
- It is cost-effective for producing large quantities of high-quality coatings.
- The process can be used with a wide range of materials, including metals, ceramics, and composites.
By following these steps, sintering coatings achieve a balance of strength, durability, and functionality, making them a valuable solution for a variety of industrial applications.
Summary Table:
Step | Description |
---|---|
1. Preparation of Powder | Mix primary material (e.g., metal, ceramic) with a bonding agent (e.g., wax). |
2. Compaction and Shaping | Compact powder into desired shape using pressing tools or 3D-printed lasers. |
3. Heating and Consolidation | Heat to below melting point, enabling particle bonding and densification. |
4. Removal of Bonding Agent | Bonding agent evaporates, leaving a porous structure of the primary material. |
5. Particle Fusion | Particles fuse at surfaces, forming a dense, cohesive coating. |
6. Cooling and Solidification | Controlled cooling ensures the coating retains strength and durability. |
7. Applications | Used in aerospace, automotive, and electronics for wear-resistant coatings. |
8. Advantages | Tailored properties, cost-effective, and compatible with metals, ceramics, etc. |
Discover how sintering coatings can enhance your industrial applications—contact us today!