Slow pyrolysis is a thermal decomposition process that involves gradually heating biomass or organic materials in the absence of oxygen over an extended period. This method is designed to maximize the production of biochar, a solid carbon-rich material, while minimizing the yield of volatile gases and liquids. The process is characterized by lower heating rates and longer residence times compared to fast pyrolysis, making it suitable for applications where high-quality biochar is the primary goal. Below is a detailed explanation of the slow pyrolysis process, broken down into key stages and considerations.
Key Points Explained:
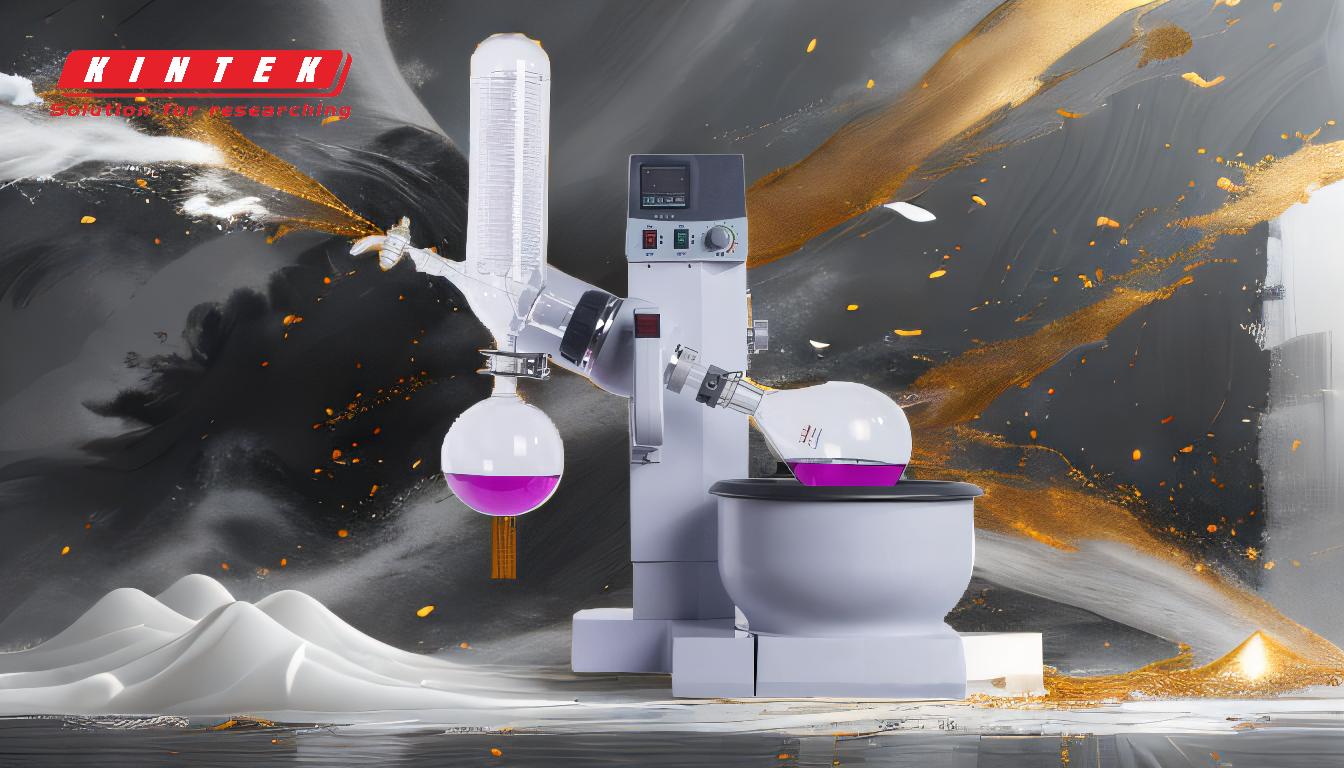
-
Feedstock Preparation
- The process begins with the selection and preparation of the feedstock, which is typically biomass such as wood, agricultural residues, or other organic materials.
- Pre-treatment steps include drying the feedstock to reduce moisture content and crushing or grinding it to achieve a uniform particle size. This ensures efficient heat transfer and consistent pyrolysis conditions.
- Removing impurities, such as dirt or inorganic materials, is also crucial to prevent contamination of the final products.
-
Loading and Heating
- The prepared feedstock is loaded into a pyrolysis reactor, which is designed to operate in an oxygen-free or low-oxygen environment. This prevents combustion and ensures that the material undergoes thermal decomposition rather than burning.
- The reactor is gradually heated to temperatures typically ranging from 200°C to 500°C. The heating rate is slow, often taking several hours, to allow for controlled decomposition of the organic material.
- The absence of oxygen ensures that the process is anaerobic, promoting the breakdown of complex organic molecules into simpler compounds.
-
Thermal Decomposition
- As the temperature rises, the biomass undergoes a series of chemical reactions. The long residence time in the reactor allows for the gradual breakdown of cellulose, hemicellulose, and lignin, the primary components of biomass.
- This stage is critical for the formation of biochar, as the slow heating rate and extended residence time favor the retention of carbon in the solid phase.
- Volatile gases and condensable vapors are also produced during this stage, but their yield is relatively low compared to fast pyrolysis.
-
Product Separation
- The pyrolysis process yields three main products: biochar, bio-oil, and syngas.
- Biochar: The solid residue, rich in carbon, settles at the bottom of the reactor. It is collected and cooled for further use as a soil amendment, carbon sequestration agent, or in other applications.
- Bio-oil: The condensable vapors are cooled and condensed into a liquid known as bio-oil. However, in slow pyrolysis, the yield of bio-oil is minimal due to the focus on biochar production.
- Syngas: Non-condensable gases, such as methane, hydrogen, and carbon monoxide, are collected and can be recycled to provide heat for the pyrolysis process or used as a fuel source.
- The pyrolysis process yields three main products: biochar, bio-oil, and syngas.
-
Post-Processing
- The biochar may undergo additional processing, such as sieving or grinding, to achieve the desired particle size and quality.
- The exhaust gases are often treated to remove particulate matter and harmful substances, ensuring compliance with environmental regulations.
- The bio-oil, if collected, may be refined for use as a fuel or chemical feedstock, though this is less common in slow pyrolysis.
-
Advantages of Slow Pyrolysis
- High-Quality Biochar: The primary advantage of slow pyrolysis is the production of high-quality biochar with excellent carbon content and stability.
- Carbon Sequestration: Biochar produced through slow pyrolysis can be used to sequester carbon in soils, contributing to climate change mitigation.
- Simplicity and Scalability: The process is relatively simple and can be scaled to suit small-scale or large-scale applications.
-
Applications of Slow Pyrolysis Products
- Biochar: Used in agriculture to improve soil fertility, water retention, and nutrient availability. It is also employed in environmental remediation and as a carbon-negative material.
- Syngas: Can be utilized as a renewable energy source for heating or electricity generation.
- Bio-oil: Although produced in smaller quantities, it can be refined for use as a liquid fuel or chemical precursor.
By understanding the slow pyrolysis process, purchasers of equipment and consumables can make informed decisions about the technology and materials needed to implement this sustainable method of biomass conversion. The focus on biochar production makes slow pyrolysis particularly valuable for applications in agriculture, environmental management, and carbon sequestration.
Summary Table:
Stage | Key Activities | Outcome |
---|---|---|
Feedstock Preparation | Drying, crushing, and removing impurities from biomass. | Uniform, moisture-free feedstock for efficient pyrolysis. |
Loading and Heating | Loading feedstock into an oxygen-free reactor; slow heating to 200°C–500°C. | Controlled thermal decomposition without combustion. |
Thermal Decomposition | Gradual breakdown of cellulose, hemicellulose, and lignin. | Formation of biochar with minimal volatile gases. |
Product Separation | Separation of biochar, bio-oil, and syngas. | High-quality biochar, minimal bio-oil, and syngas for energy or recycling. |
Post-Processing | Sieving biochar, treating exhaust gases, and refining bio-oil (if collected). | Ready-to-use biochar and environmentally compliant byproducts. |
Ready to implement slow pyrolysis for sustainable biochar production? Contact our experts today to get started!