Spark Plasma Sintering (SPS), also known as Field-Assisted Sintering Technique (FAST), is an advanced powder metallurgy process that combines pressure, electric current, and rapid heating to achieve high-density materials at lower temperatures and shorter times compared to conventional sintering. The process involves placing powder in a graphite mold, applying uniaxial pressure, and passing high-intensity electric pulses through the mold and powder. This generates localized high temperatures, plasma, and surface activation, which facilitate particle bonding and densification. The result is a material with over 99% density, achieved through mechanisms like Joule heating, discharge plasma, and plastic deformation.
Key Points Explained:
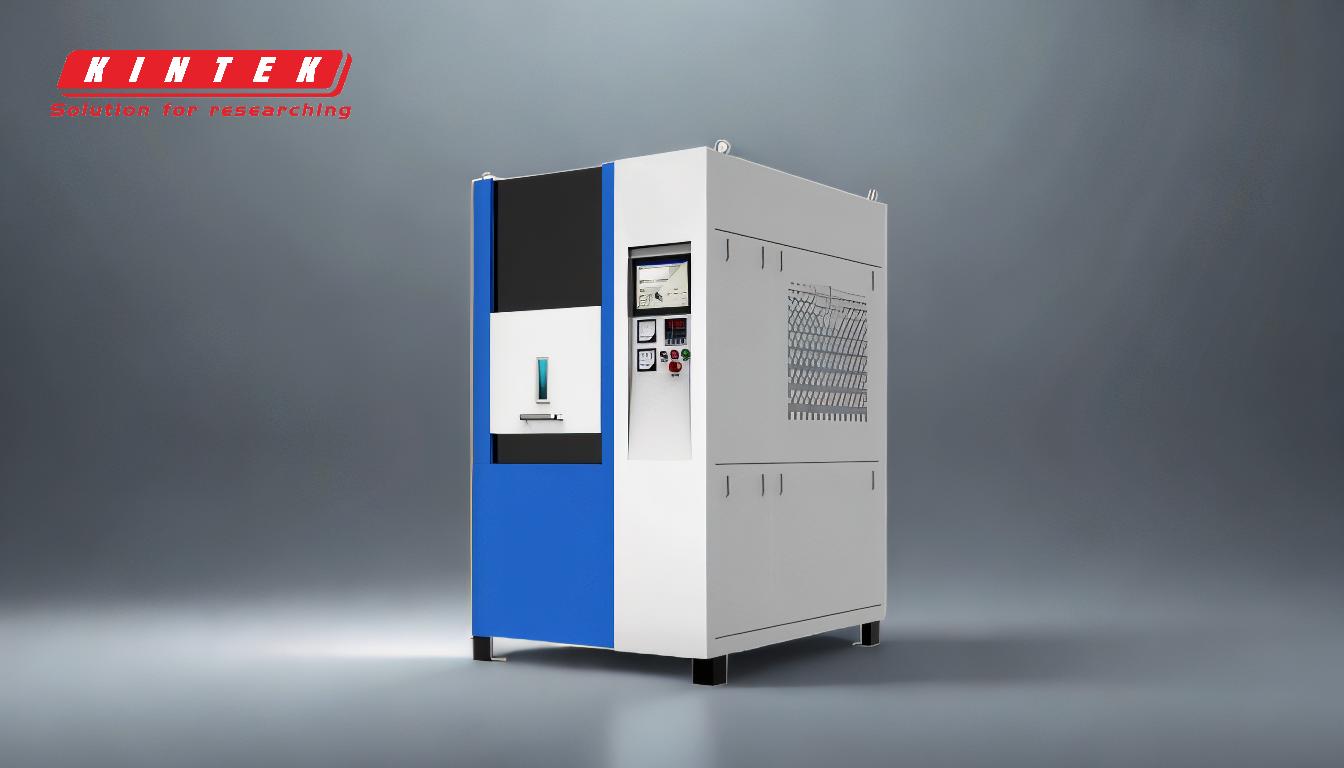
-
Setup and Initial Conditions:
- Graphite Mold: The powder is placed in a graphite mold, which acts as both a die and a heat source.
- Uniaxial Pressure: A pressure of around 200 MPa is applied to the powder compact, ensuring close contact between particles.
- Electric Current: A pulsed DC current is passed through the mold and, if conductive, the powder itself.
-
Heating Mechanism:
- Pulsed DC Current: High-energy pulsed current generates localized high temperatures (up to 10,000°C) between particles, causing spark discharge and plasma formation.
- Joule Heating: The resistance of the powder and mold to the electric current produces Joule heat, contributing to rapid heating.
- Rapid Heating Rates: Heating rates can reach up to 1,000°C per minute, significantly faster than conventional sintering methods.
-
Particle Bonding and Densification:
- Surface Activation: The electric discharge activates particle surfaces, reducing surface oxides and contaminants.
- Neck Formation: High temperatures cause particle surfaces to melt and fuse, forming necks between particles.
- Plastic Deformation: The applied pressure and localized heating induce plastic deformation, further closing gaps between particles.
-
Temperature and Time Control:
- High Temperatures: The mold and sample can reach temperatures up to 2,400°C, though sintering often occurs at lower temperatures than conventional methods.
- Short Holding Times: The process typically requires very short holding times at peak temperature, reducing energy consumption and processing time.
-
Densification and Final Properties:
- High Density: The combined effects of pressure, electric current, and rapid heating result in materials with densities exceeding 99%.
- Microstructural Control: The rapid heating and cooling rates allow for fine control over the microstructure, often resulting in finer grains and improved mechanical properties.
-
System Components:
- Axial Pressure Device: Applies and maintains the uniaxial pressure during sintering.
- Water-Cooled Punch Electrode: Ensures stable electrical contact and cooling during the process.
- Vacuum Chamber: Provides a controlled atmosphere, often under vacuum or inert gas, to prevent oxidation.
- Atmosphere Control System: Manages the environment within the chamber to ensure optimal sintering conditions.
- DC Pulse and Cooling Water: Delivers the pulsed current and manages heat dissipation.
- Displacement and Temperature Measurement: Monitors the progress of densification and temperature control.
- Safety Control Units: Ensures the safe operation of the system, particularly given the high temperatures and pressures involved.
-
Advantages Over Conventional Sintering:
- Lower Sintering Temperatures: SPS typically requires temperatures several hundred degrees lower than conventional sintering.
- Reduced Processing Time: The rapid heating and short holding times significantly reduce the overall processing time.
- Improved Material Properties: The fine microstructures and high densities achieved often result in superior mechanical, thermal, and electrical properties.
-
Applications:
- Ceramics and Metals: SPS is widely used for sintering both ceramic and metallic powders, including advanced materials like carbides, nitrides, and composites.
- Nanomaterials: The process is particularly effective for sintering nanomaterials, where conventional methods might lead to excessive grain growth.
- Complex Shapes: The ability to apply pressure during sintering allows for the production of complex shapes with high dimensional accuracy.
In summary, Spark Plasma Sintering is a highly efficient and versatile sintering technique that leverages electric current, pressure, and rapid heating to produce dense, high-quality materials with fine microstructures. Its advantages over conventional sintering methods make it particularly suitable for advanced materials and applications requiring precise control over material properties.
Summary Table:
Key Aspect | Details |
---|---|
Setup | Graphite mold, uniaxial pressure (200 MPa), pulsed DC current |
Heating Mechanism | Pulsed DC current, Joule heating, rapid heating rates (up to 1,000°C/min) |
Particle Bonding | Surface activation, neck formation, plastic deformation |
Temperature Control | High temperatures (up to 2,400°C), short holding times |
Final Properties | >99% density, fine microstructure, improved mechanical properties |
Advantages | Lower sintering temperatures, reduced processing time, superior properties |
Applications | Ceramics, metals, nanomaterials, complex shapes |
Transform your material processing with Spark Plasma Sintering—contact our experts today to learn more!