Thermal evaporation is a widely used Physical Vapor Deposition (PVD) technique for depositing thin films onto substrates. It involves heating a source material in a vacuum chamber until it vaporizes, allowing the vaporized atoms to travel through the vacuum and condense on a substrate, forming a thin film. The process is simple, efficient, and suitable for a variety of materials. Heating methods include resistive heating, electron beams, or lasers, depending on the material's properties. The vacuum environment ensures minimal contamination and allows for precise control over film thickness and uniformity. Thermal evaporation is commonly used in industries such as electronics, optics, and coatings.
Key Points Explained:
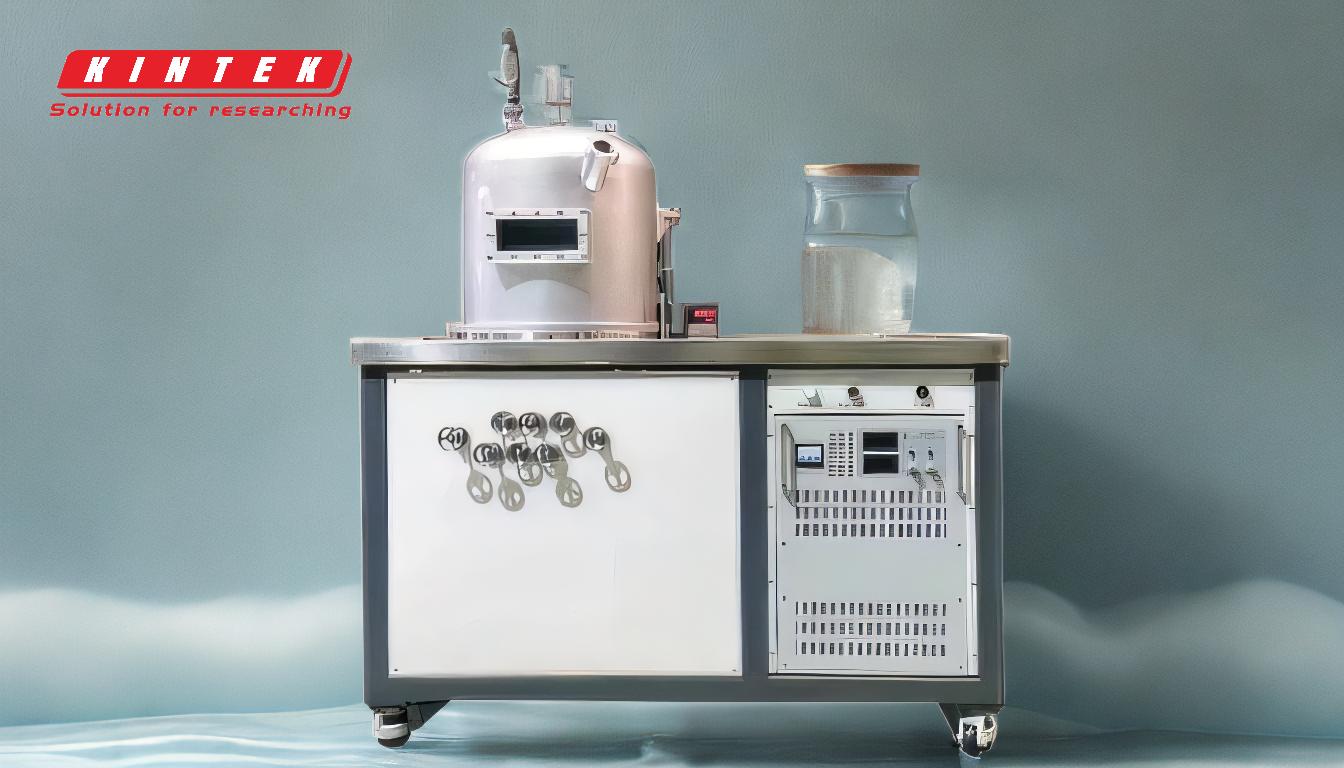
-
Overview of Thermal Evaporation in PVD:
- Thermal evaporation is a PVD technique used to deposit thin films on substrates.
- It involves heating a source material in a vacuum until it vaporizes, and the vapor condenses on the substrate to form a thin film.
- This method is simple, cost-effective, and versatile, making it suitable for a wide range of materials and applications.
-
Key Components of the Process:
- Vacuum Chamber: The process occurs in a high-vacuum environment to minimize contamination and ensure collision-free transport of vaporized atoms.
- Source Material: The material to be deposited is placed in the chamber and heated until it reaches its vaporization temperature.
- Substrate: The target surface where the thin film is deposited, typically positioned above the source material.
- Heating Mechanism: Various methods can be used to heat the source material, including resistive heating, electron beams, laser beams, or electric arcs.
-
Heating Methods:
- Resistive Heating: A common method where a filament or boat heats the material through electrical resistance.
- Electron Beam Heating: Uses a focused electron beam to heat the material, ideal for high-melting-point materials.
- Laser Heating: Utilizes a laser to vaporize the material, offering precise control and minimal contamination.
- Electric Arc Heating: Generates an electric arc to vaporize the material, suitable for conductive materials.
-
Process Steps:
-
Step 1: Preparation:
- The source material is loaded into the vacuum chamber.
- The substrate is cleaned and positioned above the source material.
-
Step 2: Evacuation:
- The chamber is evacuated to create a high-vacuum environment, typically at pressures of 10^-5 to 10^-7 Torr.
-
Step 3: Heating:
- The source material is heated using one of the methods mentioned above until it vaporizes.
-
Step 4: Deposition:
- The vaporized atoms travel through the vacuum and condense on the substrate, forming a thin film.
-
Step 5: Cooling:
- The substrate is allowed to cool, ensuring the film adheres properly.
-
Step 1: Preparation:
-
Advantages of Thermal Evaporation:
- Simplicity: The process is straightforward and easy to implement.
- High Purity: The vacuum environment minimizes contamination, resulting in high-purity films.
- Versatility: Suitable for a wide range of materials, including metals, alloys, and some compounds.
- Precision: Allows for precise control over film thickness and uniformity.
-
Challenges and Limitations:
- Material Limitations: Some materials, such as refractory metals, require specialized heating methods.
- Uniformity: Achieving uniform film thickness can be challenging for large or complex substrates.
- Adhesion: Poor adhesion may occur if the substrate is not properly cleaned or prepared.
- Cost: High-vacuum equipment and specialized heating methods can be expensive.
-
Applications:
- Electronics: Used to deposit conductive and insulating layers in semiconductor devices.
- Optics: Applied in the production of reflective and anti-reflective coatings for lenses and mirrors.
- Coatings: Used for decorative, protective, and functional coatings on various substrates.
- Research: Widely used in academic and industrial research for thin film development.
-
Comparison with Other PVD Techniques:
- Sputtering: Unlike thermal evaporation, sputtering uses energetic ions to dislodge atoms from a target material, offering better control over film composition and adhesion.
- Pulsed Laser Deposition (PLD): PLD uses a laser to ablate material, providing precise control but requiring more complex equipment.
- Chemical Vapor Deposition (CVD): CVD involves chemical reactions to deposit films, offering better conformal coverage but requiring higher temperatures and more complex processes.
-
Future Trends:
- Advanced Heating Methods: Development of more efficient and precise heating techniques, such as plasma-assisted evaporation.
- Hybrid Techniques: Combining thermal evaporation with other PVD or CVD methods to enhance film properties.
- Automation: Increasing use of automated systems for improved reproducibility and scalability.
- Sustainability: Focus on reducing energy consumption and environmental impact through optimized processes and materials.
By understanding the principles, methods, and applications of thermal evaporation, purchasers and users of equipment and consumables can make informed decisions to optimize their processes and achieve desired outcomes.
Summary Table:
Aspect | Details |
---|---|
Process | Heating a source material in a vacuum to deposit thin films on substrates. |
Heating Methods | Resistive, electron beam, laser, or electric arc heating. |
Advantages | Simple, high purity, versatile, precise control over film thickness. |
Applications | Electronics, optics, coatings, and research. |
Challenges | Material limitations, uniformity, adhesion, and equipment cost. |
Discover how thermal evaporation can enhance your thin film processes—contact our experts today for tailored solutions!