Thermal evaporation thin film deposition is a widely used physical vapor deposition (PVD) technique that involves heating a source material in a high-vacuum environment until it vaporizes. The vaporized material then condenses onto a substrate, forming a thin film. This process is simple, cost-effective, and does not require complex precursors or reactive gases, making it suitable for applications such as OLEDs and thin-film transistors. The quality of the thin film depends on factors like vacuum pressure, source material properties, and substrate conditions. Below, the process and key factors influencing thermal evaporation deposition are explained in detail.
Key Points Explained:
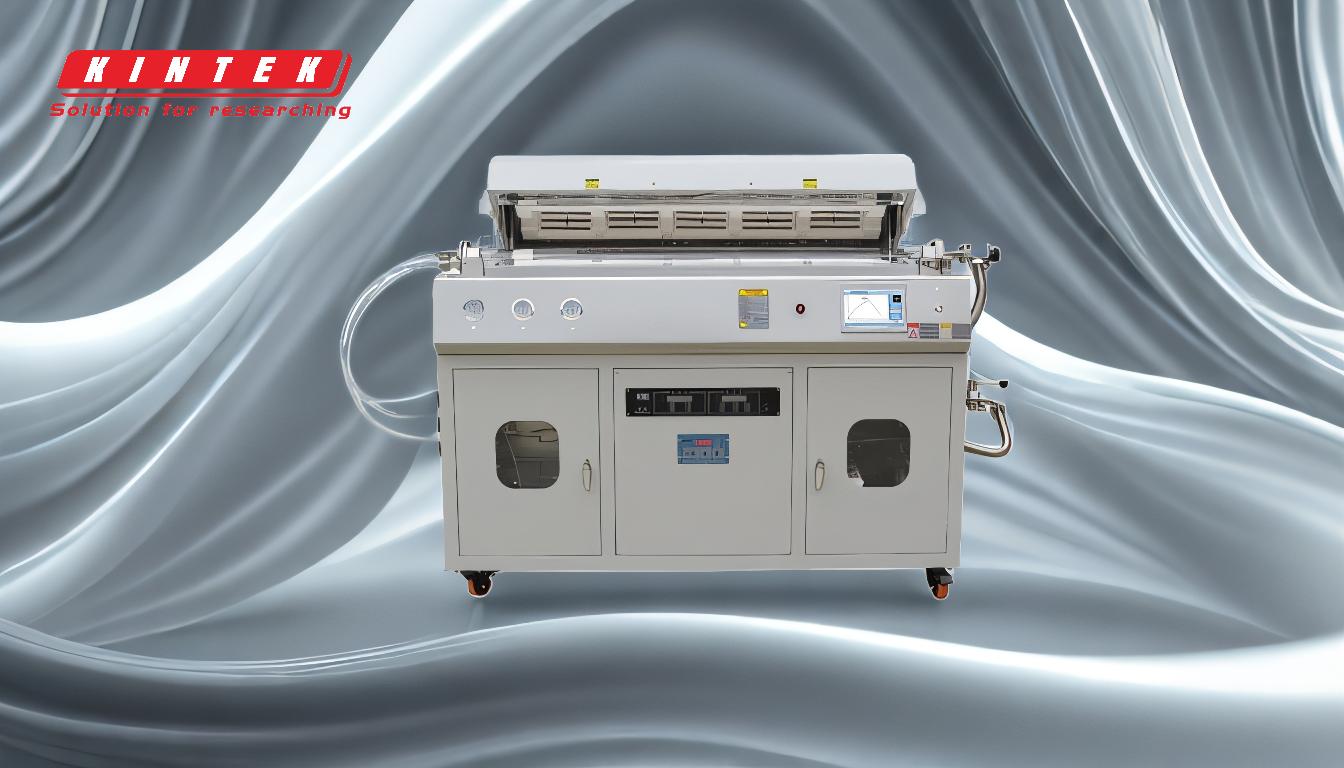
-
High-Vacuum Environment
- A high-vacuum environment is essential for thermal evaporation deposition to minimize contamination and ensure a clean deposition process.
- The vacuum reduces the presence of impurities and increases the mean free path of the vaporized material, allowing it to travel unimpeded to the substrate.
- The pressure in the vacuum chamber plays a critical role in determining the quality of the thin film. Higher vacuum levels improve film uniformity and reduce defects.
-
Heating the Source Material
- The source material, often referred to as the target, is heated to its evaporation temperature using a resistive heat source.
- The material is contained in a high-temperature-resistant boat, basket, or coil, which ensures uniform heating and evaporation.
- The evaporation rate depends on the material's molecular weight and the temperature applied. Proper control of these parameters is crucial for achieving consistent film thickness.
-
Vaporization and Condensation
- Once the source material reaches its evaporation temperature, it turns into vapor and forms a stream that travels toward the substrate.
- The vapor condenses on the substrate surface, forming a solid thin film. The substrate is typically positioned at a specific angle and distance from the source to ensure uniform deposition.
- The rotation speed of the substrate holder can be adjusted to enhance film uniformity, especially for large or complex substrates.
-
Substrate Preparation
- The substrate surface must be clean and smooth to ensure proper adhesion and uniformity of the thin film.
- Rough or contaminated surfaces can lead to non-uniform deposition, defects, or poor adhesion.
- Pre-treatment processes, such as cleaning or polishing, are often employed to prepare the substrate.
-
Post-Deposition Processes
- After deposition, the thin film may undergo annealing or heat treatment to improve its structural and electrical properties.
- The film is then analyzed for properties such as thickness, uniformity, and adhesion to determine if any adjustments to the deposition process are needed.
-
Advantages of Thermal Evaporation
- Thermal evaporation is a simple and cost-effective method that does not require complex precursors or reactive gases.
- It is suitable for depositing a wide range of materials, including pure metals, non-metals, and compounds like oxides and nitrides.
- The process is highly controllable, allowing for precise tuning of film thickness and properties.
-
Applications of Thermal Evaporation
- This technique is widely used in the production of OLEDs, thin-film transistors, and other electronic devices.
- It is also employed in optical coatings, solar cells, and protective coatings due to its ability to produce high-purity films.
For more detailed information on thermal evaporation, refer to the linked topic. This process remains one of the most reliable and versatile methods in the thin film industry, offering a balance of simplicity, cost-effectiveness, and high-quality results.
Summary Table:
Key Factor | Description |
---|---|
High-Vacuum Environment | Minimizes contamination, ensures clean deposition, and improves film uniformity. |
Heating the Source Material | Controlled heating of the target material for consistent evaporation. |
Vaporization and Condensation | Vaporized material condenses on the substrate to form a thin film. |
Substrate Preparation | Clean and smooth surfaces ensure proper adhesion and uniformity. |
Post-Deposition Processes | Annealing or heat treatment improves film properties. |
Advantages | Simple, cost-effective, and highly controllable process. |
Applications | OLEDs, thin-film transistors, optical coatings, and solar cells. |
Discover how thermal evaporation can enhance your thin film production—contact our experts today!