Vacuum vapor deposition is a sophisticated process used to create thin films on substrates by depositing material in a vacuum environment. This method is widely used in industries such as electronics, optics, and coatings due to its ability to produce high-purity, uniform, and adherent films. The process involves creating a vacuum to eliminate interfering gases, preparing the substrate, evaporating or sputtering the coating material, and depositing it onto the substrate. The choice of deposition method, such as Physical Vapor Deposition (PVD) or Chemical Vapor Deposition (CVD), depends on the desired film properties and application requirements. The process ensures precise control over film thickness, microstructure, and purity, making it essential for advanced manufacturing and material science applications.
Key Points Explained:
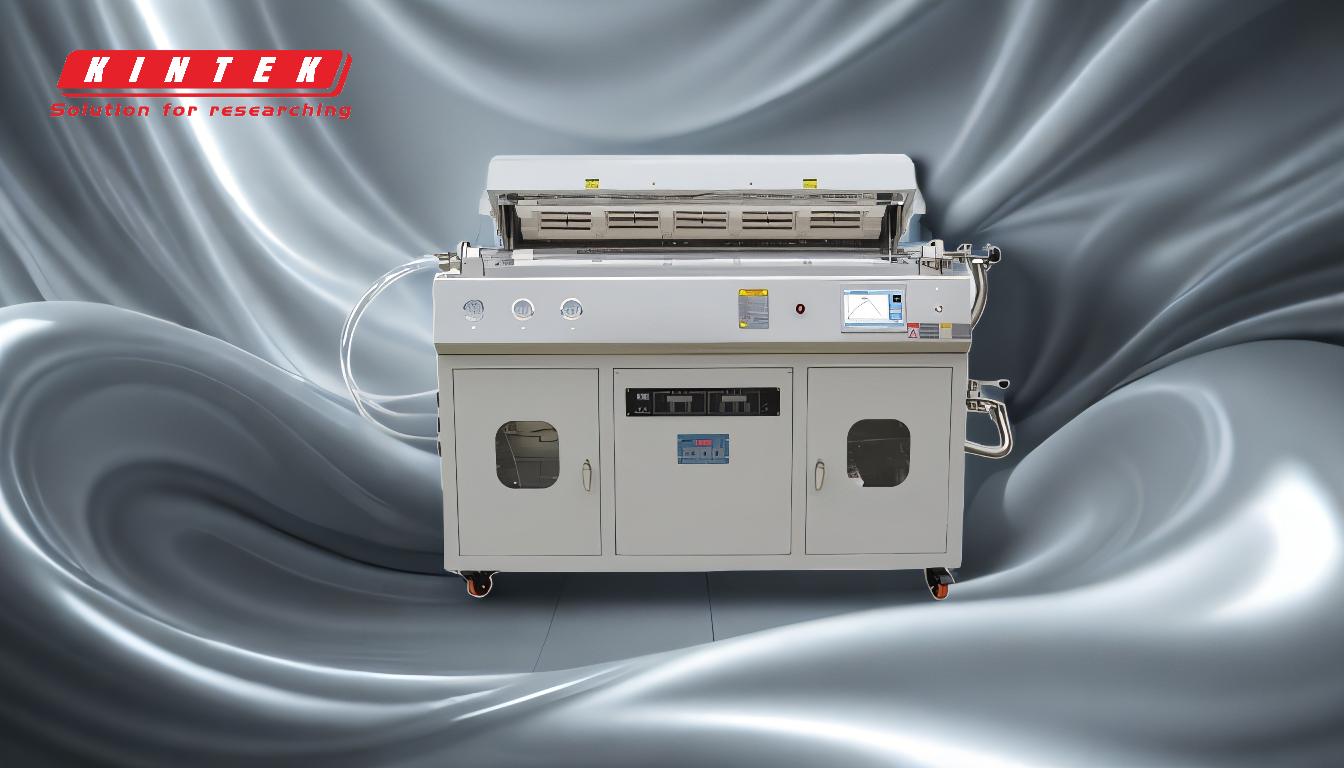
-
Creating a Vacuum Environment:
- The first step in vacuum vapor deposition is to create a vacuum inside the deposition chamber. This is done to remove air and other gases that could interfere with the deposition process. A vacuum pump is used to evacuate the chamber, ensuring a controlled environment free from contaminants. This step is crucial for achieving high-quality, uniform thin films.
-
Substrate Preparation:
- Before deposition, the substrate must be thoroughly cleaned and treated to ensure proper adhesion of the thin film. This may involve chemical cleaning, plasma treatment, or other surface modification techniques. Proper substrate preparation is essential for achieving a strong bond between the film and the substrate, which affects the film's durability and performance.
-
Evaporation or Sputtering of Coating Material:
- The coating material is either evaporated or sputtered to create a vapor. In evaporation, the material is heated until it turns into vapor, while in sputtering, ions are used to knock atoms off a target material. Both methods produce a vapor that can be deposited onto the substrate. The choice between evaporation and sputtering depends on the material properties and the desired film characteristics.
-
Deposition of Material onto the Substrate:
- The vaporized material is then deposited onto the substrate, forming a thin film. This step involves precise control over parameters such as temperature, pressure, and deposition rate to ensure uniformity and adherence of the film. The deposition process can be influenced by the substrate's orientation and the geometry of the deposition chamber.
-
Cooling and Venting the System:
- After the deposition is complete, the system is cooled down, and the chamber is vented to return to atmospheric pressure. Cooling is often achieved by introducing inert gases like argon, which help to prevent chemical reactions and ensure the stability of the deposited film. Proper cooling and venting are essential for maintaining the integrity of the thin film and preparing the system for the next deposition cycle.
-
Choice of Deposition Method:
- The selection of the deposition method (PVD, CVD, or others) depends on the specific requirements of the application, such as film thickness, purity, microstructure, and deposition rate. Each method has its advantages and limitations, and the choice is influenced by factors such as the material being deposited, the substrate, and the desired film properties.
-
Applications and Importance:
- Vacuum vapor deposition is critical in various industries, including electronics (for semiconductor devices), optics (for anti-reflective coatings), and coatings (for wear-resistant and decorative finishes). The ability to produce high-quality, uniform thin films with precise control over properties makes this process indispensable in advanced manufacturing and material science.
By understanding these key steps and considerations, one can appreciate the complexity and precision involved in vacuum vapor deposition, making it a vital process in modern technology and industry.
Summary Table:
Step | Description |
---|---|
1. Creating a Vacuum | Remove air and gases using a vacuum pump to ensure a contamination-free chamber. |
2. Substrate Preparation | Clean and treat the substrate for proper adhesion of the thin film. |
3. Evaporation/Sputtering | Heat or ionize the coating material to create a vapor for deposition. |
4. Deposition | Deposit the vaporized material onto the substrate to form a thin film. |
5. Cooling & Venting | Cool the system and vent the chamber to stabilize the deposited film. |
6. Deposition Method | Choose PVD, CVD, or other methods based on application requirements. |
7. Applications | Used in electronics, optics, and coatings for high-purity, uniform films. |
Learn how vacuum vapor deposition can enhance your manufacturing process—contact our experts today!