Vapor deposition is a process used to create thin films or coatings on a substrate by depositing material in vapor form. It is widely used in industries such as semiconductors, optics, and protective coatings. The two main types of vapor deposition are Chemical Vapor Deposition (CVD) and Physical Vapor Deposition (PVD). CVD involves chemical reactions between gaseous precursors and the substrate to form a thin film, while PVD relies on physical processes like evaporation, sputtering, or plasma excitation to deposit material onto the substrate. Both methods require precise control of temperature, pressure, and gas flow to achieve uniform and high-quality coatings.
Key Points Explained:
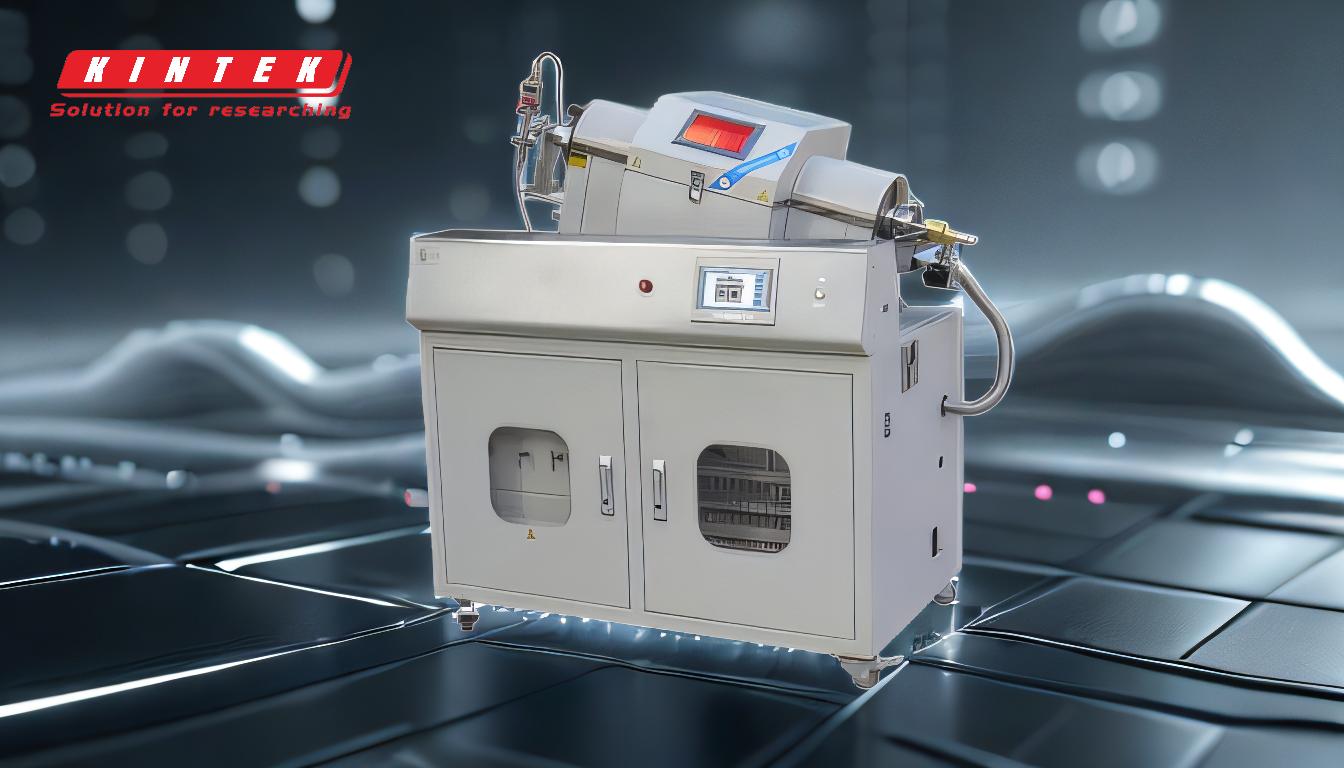
-
Chemical Vapor Deposition (CVD):
- Process Overview: In CVD, the substrate is placed in a chamber filled with organometallic or reactive gases. The gas molecules react with the substrate surface, forming a thin film through chemical reactions.
-
Steps Involved:
- Transport of reacting gaseous species to the substrate surface.
- Adsorption of the species onto the surface.
- Surface-catalyzed reactions leading to film growth.
- Desorption of byproducts and their removal from the chamber.
- Applications: CVD is used for creating high-purity and high-performance coatings, such as silicon dioxide in semiconductor manufacturing or diamond-like carbon coatings.
-
Physical Vapor Deposition (PVD):
- Process Overview: PVD involves the physical transfer of material from a source (target) to the substrate. This is achieved through processes like sputtering, evaporation, or plasma excitation.
-
Steps Involved:
- Vaporization of the coating material through methods like sputtering or evaporation.
- Migration of vaporized atoms or molecules to the substrate.
- Deposition of the material onto the substrate to form a thin film.
- Applications: PVD is commonly used for decorative coatings, wear-resistant coatings, and optical films.
-
Sputtering Deposition:
- Process Overview: A specific type of PVD where high-energy ions (usually argon) bombard the target material, ejecting its atoms, which then deposit onto the substrate.
- Advantages: Sputtering allows for precise control over film thickness and composition, making it ideal for applications like thin-film solar cells and magnetic storage media.
-
Key Differences Between CVD and PVD:
- Mechanism: CVD relies on chemical reactions, while PVD is based on physical processes.
- Temperature: CVD often requires higher temperatures compared to PVD.
- Film Quality: CVD typically produces films with better step coverage and conformality, whereas PVD films are more directional.
-
Factors Influencing Vapor Deposition:
- Substrate Preparation: The substrate must be clean and properly prepared to ensure good adhesion of the deposited film.
- Process Parameters: Temperature, pressure, gas flow rates, and power input must be carefully controlled to achieve the desired film properties.
- Post-Deposition Treatments: Annealing or heat treatment may be required to improve film properties like adhesion, stress, or crystallinity.
-
Applications of Vapor Deposition:
- Semiconductors: Used for depositing insulating, conducting, and semiconducting layers in microelectronics.
- Optics: Produces anti-reflective, reflective, or filter coatings for lenses and mirrors.
- Protective Coatings: Enhances wear resistance, corrosion resistance, and thermal stability of tools and components.
By understanding the principles and steps involved in vapor deposition, manufacturers can select the appropriate method for their specific application, ensuring high-quality and durable coatings.
Summary Table:
Aspect | Chemical Vapor Deposition (CVD) | Physical Vapor Deposition (PVD) |
---|---|---|
Mechanism | Chemical reactions between gaseous precursors and the substrate. | Physical processes like evaporation, sputtering, or plasma excitation. |
Temperature | Higher temperatures required. | Lower temperatures compared to CVD. |
Film Quality | Better step coverage and conformality. | More directional films. |
Applications | High-purity coatings (e.g., silicon dioxide, diamond-like carbon). | Decorative, wear-resistant, and optical coatings. |
Key Steps | Transport, adsorption, surface reaction, desorption. | Vaporization, migration, deposition. |
Need help selecting the right vapor deposition method for your application? Contact our experts today!