Calcination is a thermal treatment process primarily used to induce thermal decomposition, remove volatile substances, or cause phase transitions in materials. It is commonly applied in industries such as metallurgy, ceramics, and chemistry to prepare raw materials for further processing or to achieve desired properties. The process typically involves heating a substance to high temperatures in the absence or limited supply of air or oxygen, which prevents combustion. Calcination is essential for producing materials like lime from limestone, activating catalysts, or removing impurities from ores. It plays a critical role in enhancing the physical and chemical properties of materials, making them suitable for specific industrial applications.
Key Points Explained:
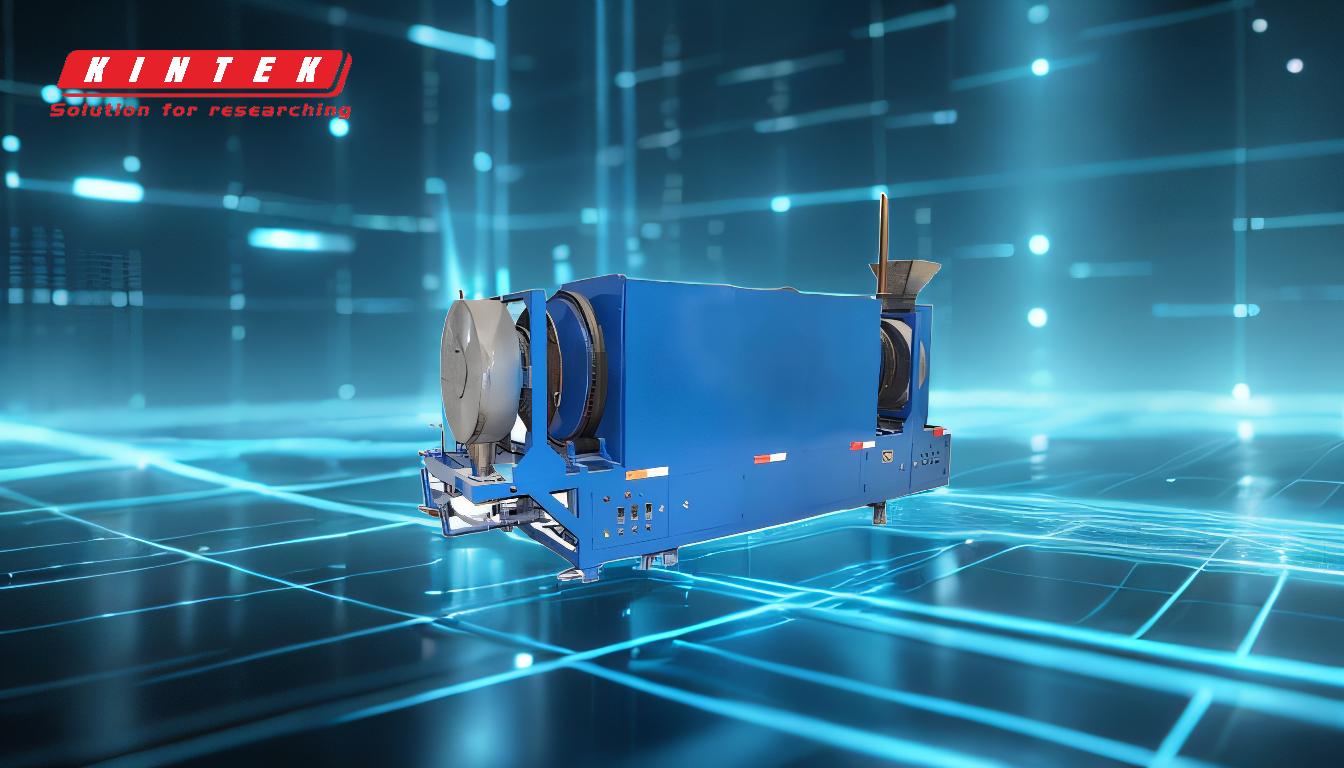
-
Definition and Purpose of Calcination:
- Calcination is a thermal treatment process where materials are heated to high temperatures, typically in the absence or limited supply of oxygen, to achieve specific chemical or physical changes.
- The primary purposes include:
- Thermal Decomposition: Breaking down compounds into simpler substances, such as converting calcium carbonate (limestone) into calcium oxide (lime) and carbon dioxide.
- Removal of Volatile Components: Eliminating water, carbon dioxide, or other volatile impurities from raw materials.
- Phase Transitions: Altering the crystalline structure of materials to improve their properties.
-
Applications in Various Industries:
-
Metallurgy:
- Calcination is used to remove impurities from ores, such as driving off moisture or decomposing carbonates in metal ores.
- Example: Roasting sulfide ores to convert them into oxides for easier extraction of metals.
-
Ceramics and Cement Production:
- In ceramics, calcination is used to prepare raw materials like clay by removing water and organic matter.
- In cement production, limestone is calcined to produce lime, a key ingredient in cement.
-
Chemical Industry:
- Calcination is employed to activate catalysts or produce chemicals like alumina from bauxite.
-
Metallurgy:
-
Process Conditions:
- Temperature: Calcination typically occurs at temperatures ranging from 500°C to 1200°C, depending on the material and desired outcome.
- Atmosphere: The process is often carried out in an inert or oxygen-limited environment to prevent combustion or unwanted oxidation.
- Equipment: Common equipment used includes rotary kilns, muffle furnaces, and fluidized bed reactors.
-
Benefits of Calcination:
- Improved Material Properties: Calcination enhances the porosity, reactivity, and purity of materials, making them more suitable for industrial use.
- Energy Efficiency: By removing volatile components, the calcined material becomes lighter and easier to transport and process.
- Environmental Impact: In some cases, calcination can reduce waste and emissions by converting raw materials into more usable forms.
-
Challenges and Considerations:
- Energy Consumption: Calcination requires significant energy input due to the high temperatures involved.
- Material Loss: Some volatile components, such as carbon dioxide, are lost during the process, which can affect the overall yield.
- Equipment Maintenance: High-temperature operations can lead to wear and tear on equipment, requiring regular maintenance.
-
Examples of Calcination in Practice:
- Lime Production: Limestone (CaCO₃) is calcined to produce quicklime (CaO), which is used in construction, water treatment, and chemical manufacturing.
- Catalyst Activation: In the petrochemical industry, catalysts are calcined to remove impurities and enhance their activity.
- Ceramic Glaze Preparation: Raw materials like kaolin are calcined to improve their stability and performance in glazes.
By understanding the purpose and process of calcination, industries can optimize material preparation and achieve desired outcomes efficiently. This thermal treatment is a cornerstone in transforming raw materials into valuable products across various sectors.
Summary Table:
Aspect | Details |
---|---|
Primary Purpose | Induce thermal decomposition, remove volatile substances, cause phase transitions. |
Key Applications | Metallurgy, ceramics, cement production, chemical industry. |
Temperature Range | 500°C to 1200°C. |
Atmosphere | Absence or limited supply of oxygen to prevent combustion. |
Common Equipment | Rotary kilns, muffle furnaces, fluidized bed reactors. |
Benefits | Improved material properties, energy efficiency, reduced environmental impact. |
Challenges | High energy consumption, material loss, equipment maintenance. |
Learn how calcination can optimize your industrial processes—contact our experts today!