Chemical vapor deposition (CVD) is a versatile and precise method used to create thin films and coatings on substrates through chemical reactions in the gas phase. It is widely employed in industries such as electronics, optics, and materials science due to its ability to produce ultra-thin, high-quality layers with excellent control over composition and thickness. The process involves transporting gaseous reactants to a substrate, where they undergo surface reactions to form a solid film. CVD is particularly valued for its precision, versatility, and ability to deposit materials at the atomic or molecular level, making it essential for applications like semiconductor manufacturing, protective coatings, and advanced material synthesis.
Key Points Explained:
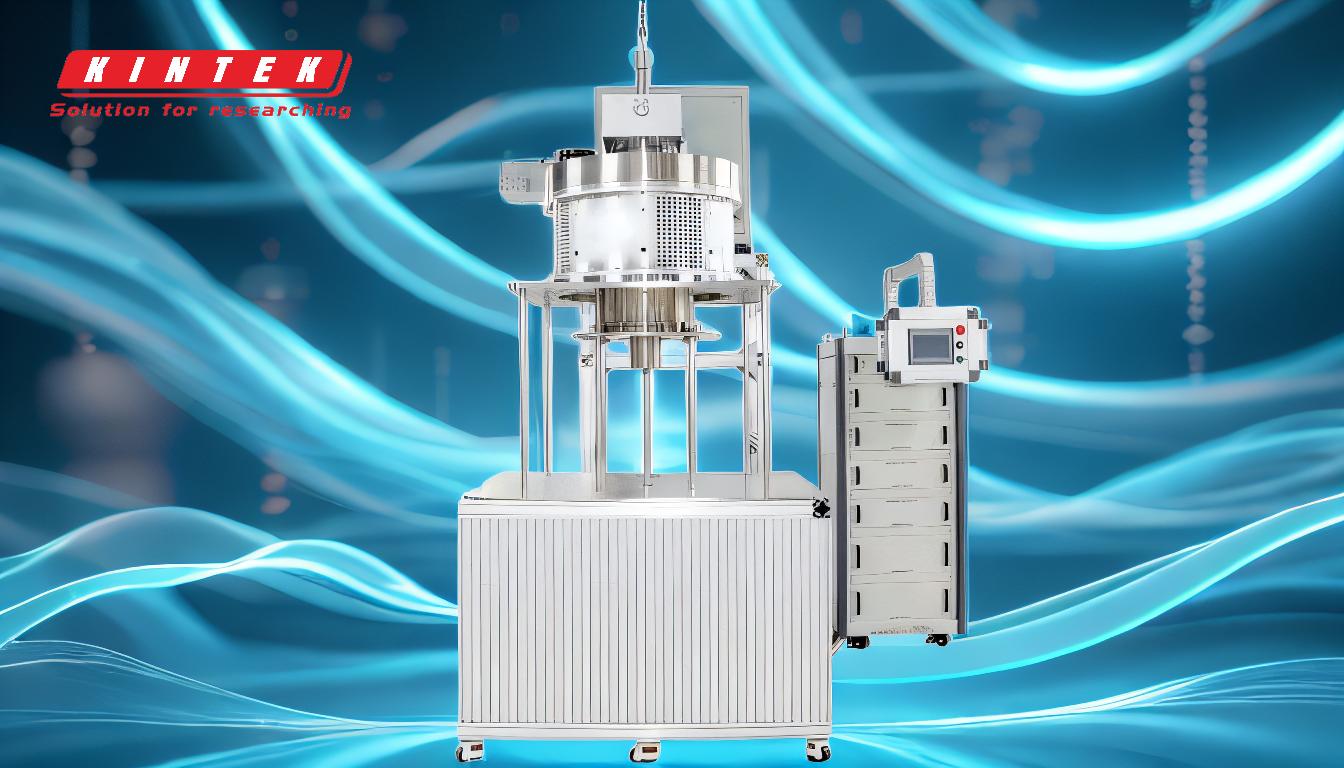
-
Purpose of Chemical Vapor Deposition (CVD):
- The primary purpose of chemical vapor deposition is to produce thin films and coatings on substrates through controlled chemical reactions in the gas phase. This method is highly precise and versatile, making it suitable for a wide range of applications, including electronics, optics, and advanced materials.
-
Advantages of CVD:
- Versatility: CVD relies on chemical reactions, allowing it to deposit a wide variety of materials, including metals, semiconductors, and ceramics.
- Precision: The process offers full control over the timing and conditions, enabling the creation of ultra-thin layers with precise thickness and composition.
- High-Quality Films: CVD produces films with excellent uniformity, purity, and adherence to the substrate, making it ideal for applications requiring high-performance materials.
-
Steps in the CVD Process:
- Transport of Reacting Gaseous Species: Gaseous reactants are transported to the substrate surface.
- Adsorption: The reactants adsorb onto the substrate surface.
- Surface Reactions: Heterogeneous, surface-catalyzed reactions occur, leading to the formation of a solid film.
- Surface Diffusion: Reactants diffuse across the surface to growth sites.
- Nucleation and Growth: The film nucleates and grows layer by layer.
- Desorption and Transport of Byproducts: Gaseous reaction byproducts desorb from the surface and are transported away.
-
Applications of CVD:
- Semiconductor Manufacturing: CVD is widely used to deposit thin films of silicon, silicon dioxide, and other materials in the production of integrated circuits and microelectronics.
- Protective Coatings: It is used to create wear-resistant, corrosion-resistant, and thermal barrier coatings on tools, components, and machinery.
- Optical and Electronic Devices: CVD is essential for producing thin films in solar cells, LEDs, and optical coatings.
- Advanced Materials: The process is used to synthesize nanomaterials, graphene, and other cutting-edge materials.
-
Importance in Modern Technology:
- CVD plays a critical role in advancing technology by enabling the production of high-performance materials and devices. Its ability to deposit materials at the atomic or molecular level makes it indispensable for innovations in electronics, energy, and materials science.
By understanding the purpose, advantages, and steps involved in CVD, it becomes clear why this process is a cornerstone of modern manufacturing and material science. Its precision and versatility make it an invaluable tool for creating the advanced materials and devices that drive technological progress.
Summary Table:
Aspect | Details |
---|---|
Purpose | Produce thin films and coatings through controlled gas-phase reactions. |
Advantages | Versatility, precision, and high-quality films with excellent uniformity. |
Key Steps | Transport, adsorption, surface reactions, diffusion, nucleation, desorption. |
Applications | Semiconductors, protective coatings, optical devices, advanced materials. |
Importance | Essential for innovations in electronics, energy, and materials science. |
Learn how CVD can revolutionize your material science projects—contact our experts today!