Chemical vapor deposition (CVD) is a versatile and widely used technique in modern manufacturing and material science. Its primary purpose is to deposit thin films of metallic, ceramic, and semiconducting materials onto a substrate through chemical reactions in the vapor or gas phase. This process is essential for creating high-performance materials with precise compositions and thicknesses, down to a single atomic layer. CVD is favored for its ability to produce uniform coatings without line-of-sight restrictions, making it indispensable in industries such as semiconductors, electronics, and packaging. It enables the production of advanced devices, including microelectronics, artificial intelligence technologies, and even functional coatings for everyday items like potato chip bags.
Key Points Explained:
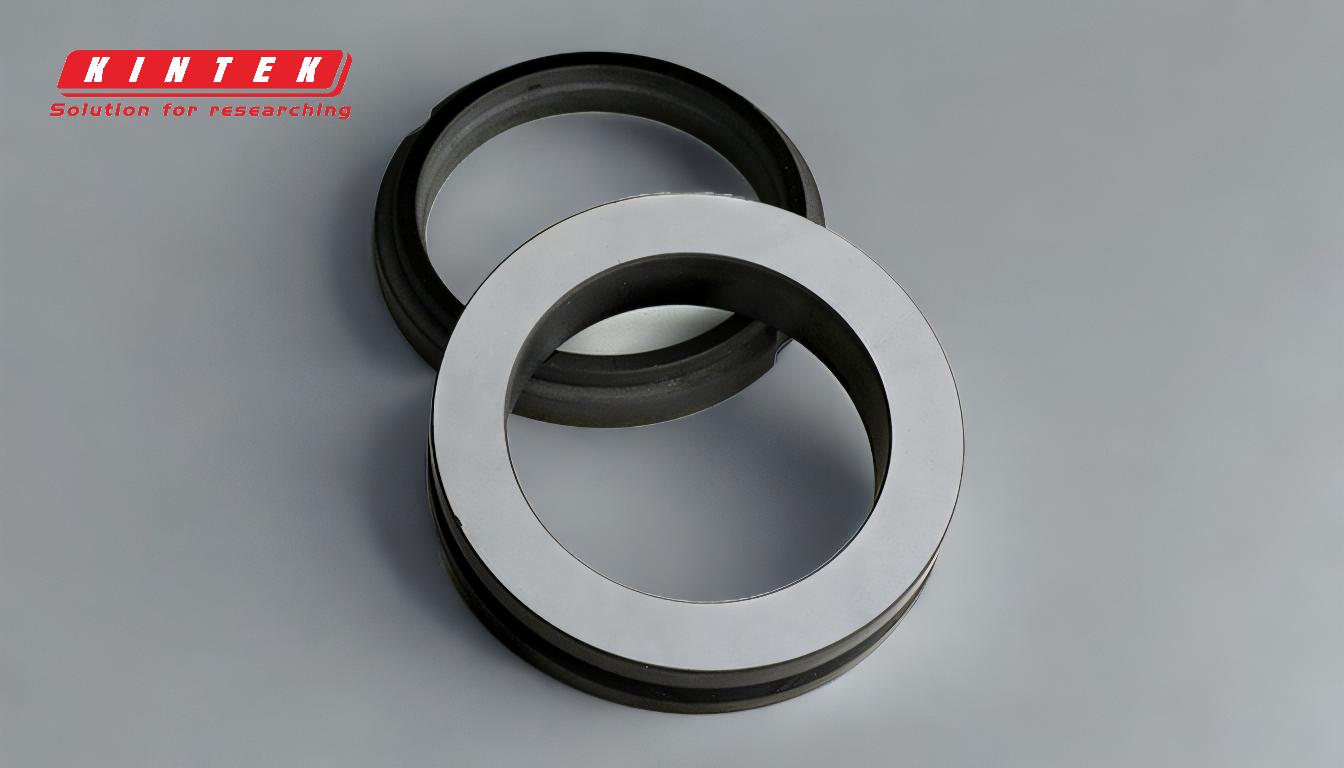
-
Deposition of Thin Films:
- CVD is primarily used to deposit thin films of metallic, ceramic, and semiconducting materials onto a substrate. These films can range from a few nanometers to micrometers in thickness and are critical for creating functional surfaces with specific properties.
- The process involves chemical reactions in the vapor or gas phase, which result in the deposition of solid material onto a heated surface. This allows for precise control over the composition and structure of the deposited film.
-
Versatility in Material Deposition:
- CVD is capable of depositing a wide variety of materials, including polymers like poly(paraxylene), metals, ceramics, and semiconductors. This versatility makes it suitable for diverse applications across multiple industries.
- The technique can produce films with different compositions and thicknesses, enabling the creation of materials tailored to specific functional requirements.
-
Non-Line-of-Sight Deposition:
- Unlike physical vapor deposition (PVD) methods such as sputtering and evaporation, CVD does not require line-of-sight deposition. This means it can uniformly coat complex geometries and surfaces with intricate features, making it ideal for advanced manufacturing processes.
-
Growth of Low-Dimensional Materials:
- CVD is widely used for the efficient growth of low-dimensional materials, such as graphene and other 2D materials. These materials are crucial for next-generation electronics, sensors, and energy storage devices due to their unique electrical, thermal, and mechanical properties.
-
Applications in Advanced Technologies:
- CVD plays a critical role in the semiconductor industry, enabling the production of microelectronics, integrated circuits, and artificial intelligence technologies. It is also used in creating functional coatings for packaging materials, such as aluminum films on potato chip bags.
- The technique is essential for developing advanced devices that require precise material properties, such as high conductivity, durability, or optical transparency.
-
Scalability and Precision:
- CVD is a scalable process that can be adapted for both laboratory research and large-scale industrial production. Its ability to deposit materials with atomic-level precision makes it a cornerstone of modern nanotechnology and materials science.
-
Role in Modern Manufacturing:
- Without CVD, many industries, including electronics, aerospace, and energy, would struggle to achieve the same level of productivity and innovation. The technique enables the creation of small, powerful, and highly functional devices that drive technological progress.
In summary, CVD is a foundational technology that underpins modern manufacturing and material science. Its ability to deposit high-quality thin films with precise control over composition and structure makes it indispensable for a wide range of applications, from everyday packaging to cutting-edge electronics and artificial intelligence.
Summary Table:
Key Aspect | Description |
---|---|
Primary Purpose | Deposits thin films of metallic, ceramic, and semiconducting materials. |
Versatility | Deposits polymers, metals, ceramics, and semiconductors for diverse applications. |
Non-Line-of-Sight Deposition | Uniformly coats complex geometries without line-of-sight restrictions. |
Low-Dimensional Materials | Enables growth of graphene and 2D materials for next-gen electronics. |
Applications | Used in microelectronics, AI technologies, and functional coatings. |
Scalability | Adaptable for lab research and large-scale industrial production. |
Role in Manufacturing | Essential for creating advanced devices in electronics, aerospace, and energy. |
Learn how CVD can revolutionize your manufacturing process—contact our experts today!