Sintering in ceramics is a critical heat treatment process that transforms powdered ceramic materials into dense, strong, and functional components. By heating the material below its melting point, sintering facilitates particle bonding, reduces porosity, and enhances mechanical properties such as hardness, toughness, and precision. This process is essential for creating complex shapes and geometries that are difficult to achieve through traditional manufacturing methods. Sintering also enables cost-effective mass production while maintaining high precision and repeatability, making it indispensable in industries requiring advanced ceramic materials with specific properties.
Key Points Explained:
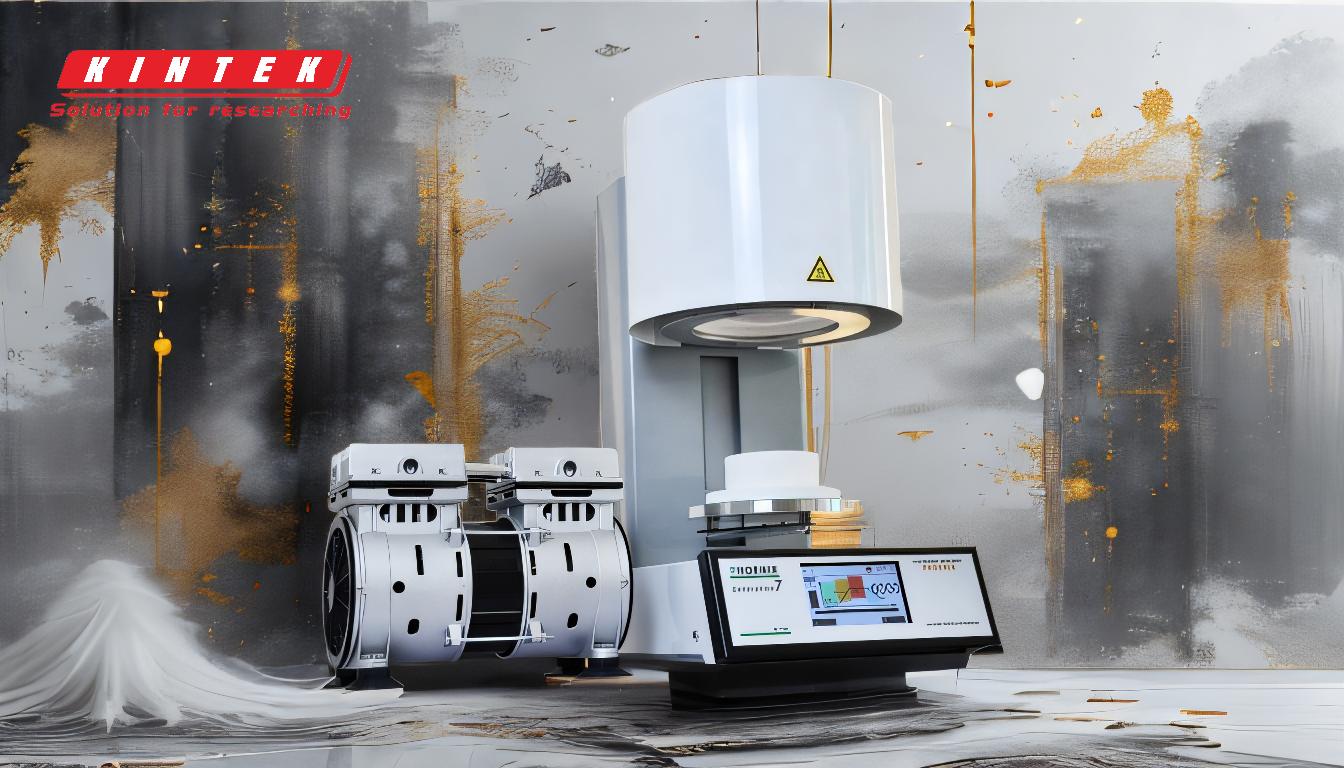
-
Transformation of Powdered Material into Dense Bodies:
- Sintering converts loose ceramic powder or "green" compacts into solid, dense polycrystalline materials. This is achieved through diffusion and mass transfer mechanisms, which bond particles together without melting the material.
- The process eliminates pores and reduces volume shrinkage, resulting in a uniform microstructure and stable shape.
-
Enhancement of Mechanical Properties:
- Sintering significantly improves the mechanical properties of ceramics, including hardness, toughness, and strength. These properties are crucial for applications requiring durability and precision.
- The controlled cooling rate during sintering allows for fine-tuning of material properties, ensuring the final product meets specific performance requirements.
-
Creation of Complex Shapes and Geometries:
- Sintering enables the production of intricate shapes and geometries that are challenging to achieve with conventional manufacturing techniques. This is particularly valuable in industries such as aerospace, automotive, and electronics.
- The process allows for the combination of multiple material properties, such as toughness and abrasion resistance, in a single component.
-
Cost-Effectiveness and Efficiency:
- Sintering is a cost-effective method for manufacturing ceramic components, as it requires lower-cost tooling compared to other processes.
- The ability to achieve rapid mass production while maintaining precision and repeatability makes sintering highly efficient for industrial applications.
-
Versatility Across Industries:
- Sintering is widely used in various industries to produce components such as gears, bearings, electrical contacts, and rotors. Its versatility stems from its ability to create materials with tailored properties for specific applications.
- The process is essential for producing advanced ceramics used in high-performance environments, such as thermal insulation, cutting tools, and biomedical implants.
-
Optimization of Physical Properties:
- An optimized sintering process ensures the achievement of desired physical properties, such as density, porosity, and microstructure. This optimization is critical for meeting the performance standards required in advanced applications.
- The controlled atmosphere during sintering prevents contamination and ensures consistent quality across batches.
-
Role in Material Science and Engineering:
- Sintering plays a pivotal role in material science by enabling the development of new ceramic materials with enhanced properties. This includes materials with improved thermal, electrical, and mechanical characteristics.
- The process contributes to the advancement of technologies in fields such as energy storage, electronics, and environmental protection.
By understanding the purpose and mechanisms of sintering, manufacturers can leverage this process to produce high-quality ceramic components that meet the demands of modern industrial applications.
Summary Table:
Key Aspect | Description |
---|---|
Transforms Powdered Material | Converts loose ceramic powder into dense, solid polycrystalline materials. |
Enhances Mechanical Properties | Improves hardness, toughness, and strength for durability and precision. |
Creates Complex Shapes | Enables intricate geometries, ideal for aerospace, automotive, and electronics. |
Cost-Effective Production | Lowers tooling costs and supports rapid mass production with high precision. |
Versatile Applications | Used in gears, bearings, cutting tools, and biomedical implants. |
Optimizes Physical Properties | Ensures desired density, porosity, and microstructure for advanced applications. |
Ready to enhance your ceramic manufacturing process? Contact our experts today to learn more about sintering solutions!