Vacuum heat treatment is a specialized process used to enhance the mechanical and chemical properties of metals by heating them in a vacuum environment. This method prevents oxidation, minimizes distortion, and ensures precise control over heating and cooling parameters. It is particularly effective for materials like super-alloys, reactive metals, and stainless steel, improving their hardness, strength, and wear resistance. Additionally, vacuum heat treatment is safer and environmentally friendly, as it eliminates the use of flammable gases and harmful contaminants. This makes it ideal for industries requiring high-performance materials with superior durability and dimensional stability.
Key Points Explained:
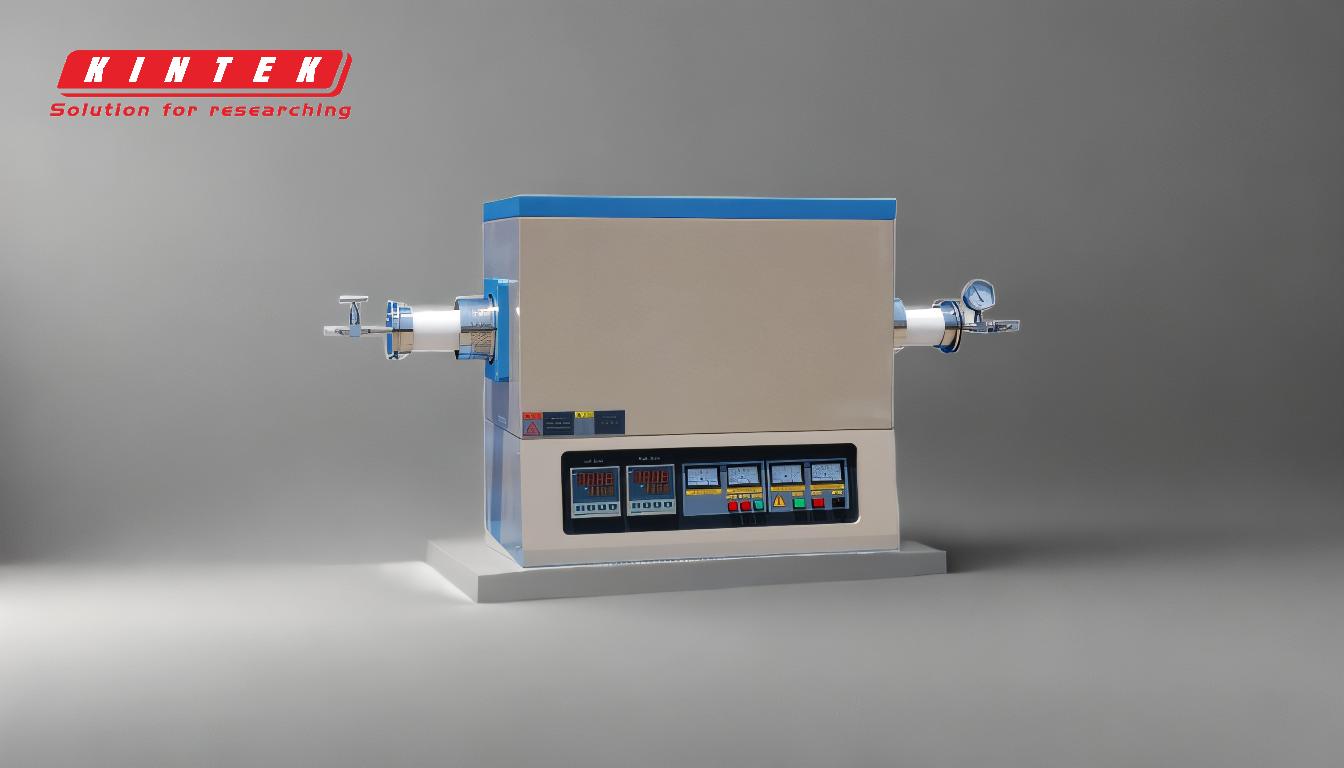
-
Prevention of Oxidation and Contamination:
- Vacuum heat treatment occurs in a sealed chamber where air is removed using a vacuum pump. This eliminates oxygen, preventing oxidation and contamination of the metal surfaces.
- The absence of oxygen ensures that the treated materials retain their original properties, such as surface finish and chemical composition, leading to enhanced durability.
-
Improved Mechanical Properties:
- By exposing metals to controlled heating and cooling cycles in a vacuum, the crystalline structure of the material is optimized. This results in:
- Increased hardness and strength.
- Enhanced wear resistance, making the components suitable for demanding applications.
- Improved elasticity and shear strength, which are critical for high-performance uses.
- By exposing metals to controlled heating and cooling cycles in a vacuum, the crystalline structure of the material is optimized. This results in:
-
Minimized Distortion and Dimensional Stability:
- The uniform heating and cooling process in a vacuum environment reduces thermal stress, minimizing the risk of distortion.
- This ensures that the treated parts maintain their dimensional accuracy, which is crucial for precision components in industries like aerospace and automotive.
-
Suitability for Specialized Materials:
- Vacuum heat treatment is particularly effective for materials that are sensitive to oxidation or require precise control over their properties. These include:
- Super-alloys (e.g., nickel, iron-nickel, and cobalt-nickel-based materials).
- Reactive and refractory metals (e.g., titanium and Haynes alloys).
- Stainless steel and certain grades of brass and bronze used in musical instruments.
- Vacuum heat treatment is particularly effective for materials that are sensitive to oxidation or require precise control over their properties. These include:
-
Environmental and Safety Benefits:
- Unlike traditional heat treatment methods, vacuum heat treatment does not rely on flammable gases or produce harmful by-products.
- The process is pollution-free and complies with OSHA safety standards, ensuring a safer working environment for employees.
-
Precision and Control:
- The vacuum environment allows for meticulous control over heating and cooling rates, enabling manufacturers to tailor the process to specific material requirements.
- This precision ensures consistent results, making vacuum heat treatment ideal for high-performance applications where reliability is critical.
-
Expanded Applications:
- The improvements in chemical and mechanical properties, such as corrosion resistance and hardness, broaden the potential uses of treated metals.
- Components treated with vacuum heat treatment are suitable for industries like aerospace, medical devices, tooling, and energy, where durability and performance are paramount.
In summary, vacuum heat treatment is a versatile and advanced process that enhances the performance and longevity of metals. Its ability to prevent oxidation, improve mechanical properties, and ensure dimensional stability makes it indispensable for industries requiring high-quality, durable materials.
Summary Table:
Key Benefits | Details |
---|---|
Prevents Oxidation | Eliminates oxygen, preserving surface finish and chemical composition. |
Improves Mechanical Properties | Increases hardness, strength, wear resistance, and elasticity. |
Minimizes Distortion | Reduces thermal stress, ensuring dimensional accuracy. |
Suitable for Specialized Metals | Ideal for super-alloys, reactive metals, and stainless steel. |
Environmental & Safety Benefits | Pollution-free, no flammable gases, and OSHA-compliant. |
Precision & Control | Tailored heating and cooling rates for consistent, high-quality results. |
Expanded Applications | Aerospace, medical devices, tooling, and energy industries benefit greatly. |
Learn how vacuum heat treatment can elevate your material performance—contact our experts today!