Physical Vapor Deposition (PVD) is a sophisticated vacuum-based coating process used to create thin, durable, and high-performance films on substrates. It involves vaporizing a solid material in a vacuum environment, transporting the vaporized atoms to a substrate, and depositing them to form a thin film. This process is widely used in industries to enhance the mechanical, chemical, and optical properties of materials. PVD coatings are known for their precision, environmental friendliness, and ability to produce coatings with excellent adhesion and uniformity. The process typically involves steps like evaporation, transportation, reaction, and deposition, and can be tailored by using reactive gases to modify the composition of the coating.
Key Points Explained:
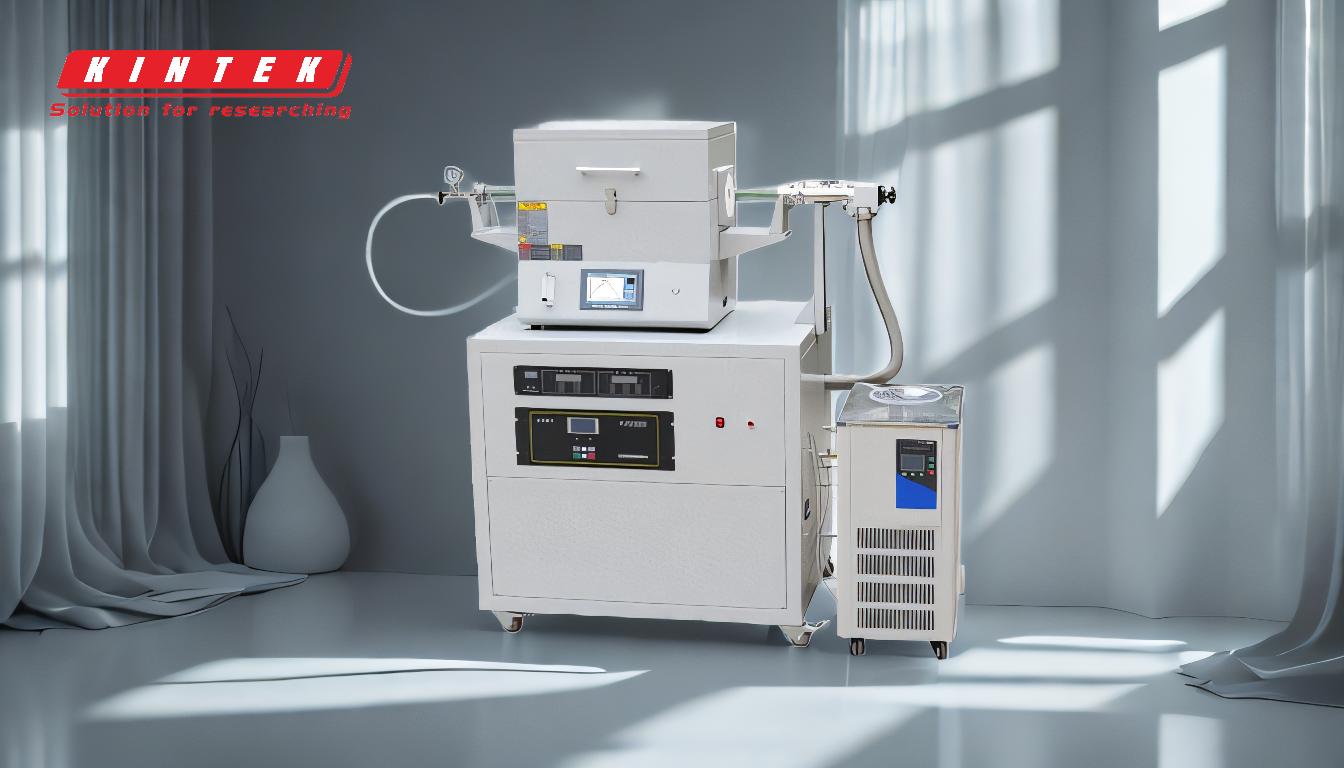
-
Definition and Overview of PVD:
- PVD is a vacuum-based thin-film deposition technique where a solid material is vaporized and then condensed onto a substrate to form a coating.
- The process occurs in a vacuum chamber to ensure the vaporized material remains clean and uncontaminated.
- PVD coatings are known for their thinness, durability, and ability to enhance the properties of the substrate.
-
Steps Involved in the PVD Process:
- Evaporation: The solid material (target) is vaporized using high-energy sources such as electron beams, ion bombardment, or cathodic arcs.
- Transportation: The vaporized atoms are transported through the vacuum chamber to the substrate.
- Reaction: The vaporized atoms may react with reactive gases (e.g., nitrogen or oxygen) to form compounds like metal nitrides, oxides, or carbides.
- Deposition: The atoms or compounds condense on the substrate, forming a thin, uniform coating.
-
Types of PVD Techniques:
- Sputtering: A method where ions bombard the target material, causing atoms to be ejected and deposited onto the substrate.
- Cathodic Arc Deposition: Uses an electric arc to vaporize the target material, creating a plasma of ionized atoms that deposit onto the substrate.
- Electron Beam Physical Vapor Deposition (EB-PVD): Utilizes an electron beam to heat and vaporize the target material.
- Thermal Evaporation: Involves heating the target material in a crucible until it vaporizes and deposits onto the substrate.
-
Advantages of PVD Coatings:
- High Precision: PVD allows for the deposition of extremely thin and uniform coatings.
- Enhanced Properties: Coatings improve hardness, wear resistance, corrosion resistance, and optical properties.
- Environmental Friendliness: PVD is a clean process that produces minimal waste and does not involve harmful chemicals.
- Versatility: Can be used to deposit a wide range of materials, including metals, ceramics, and composites.
-
Applications of PVD Coatings:
- Tool and Die Industry: Used to coat cutting tools, molds, and dies to enhance their durability and performance.
- Electronics: Applied to semiconductors, solar panels, and displays to improve conductivity and optical properties.
- Medical Devices: Used to coat implants and surgical instruments for biocompatibility and wear resistance.
- Decorative Coatings: Applied to watches, jewelry, and automotive parts to improve appearance and durability.
-
Reactive Gases in PVD:
- Reactive gases like nitrogen, oxygen, and acetylene can be introduced during the PVD process to modify the composition of the coating.
- For example, adding nitrogen can result in the formation of metal nitrides, which are known for their hardness and wear resistance.
-
Environmental and Economic Benefits:
- PVD is a sustainable alternative to traditional coating methods, as it produces minimal waste and does not involve harmful chemicals.
- The longevity and performance of PVD-coated products reduce the need for frequent replacements, leading to cost savings over time.
-
Challenges and Limitations:
- High Initial Cost: The equipment and setup for PVD can be expensive.
- Complexity: The process requires precise control of vacuum conditions, temperature, and gas flow.
- Limited Thickness: PVD coatings are typically very thin, which may not be suitable for applications requiring thicker coatings.
By understanding these key points, equipment and consumable purchasers can make informed decisions about the suitability of PVD coatings for their specific applications, considering factors like performance requirements, environmental impact, and cost-effectiveness.
Summary Table:
Aspect | Details |
---|---|
Definition | Vacuum-based thin-film deposition for durable, high-performance coatings. |
Process Steps | Evaporation, Transportation, Reaction, Deposition. |
Types of PVD | Sputtering, Cathodic Arc Deposition, EB-PVD, Thermal Evaporation. |
Advantages | High precision, enhanced properties, eco-friendly, versatile. |
Applications | Tools, electronics, medical devices, decorative coatings. |
Reactive Gases | Nitrogen, oxygen, acetylene for tailored coatings. |
Challenges | High initial cost, process complexity, limited coating thickness. |
Ready to enhance your materials with PVD coatings? Contact our experts today for tailored solutions!