Sintering and melting are two distinct processes that involve heating materials, but they differ fundamentally in terms of temperature, energy requirements, and outcomes. Sintering occurs at temperatures below the material's melting point and involves the fusion of particles through heat and pressure without liquefaction. In contrast, melting requires reaching the material's melting point, transforming it from a solid to a liquid state. The relationship between sintering temperature and melting point is critical because sintering must occur at temperatures high enough to enable particle bonding but low enough to avoid liquefaction. This balance ensures material integrity, control over the process, and the desired physical properties of the final product.
Key Points Explained:
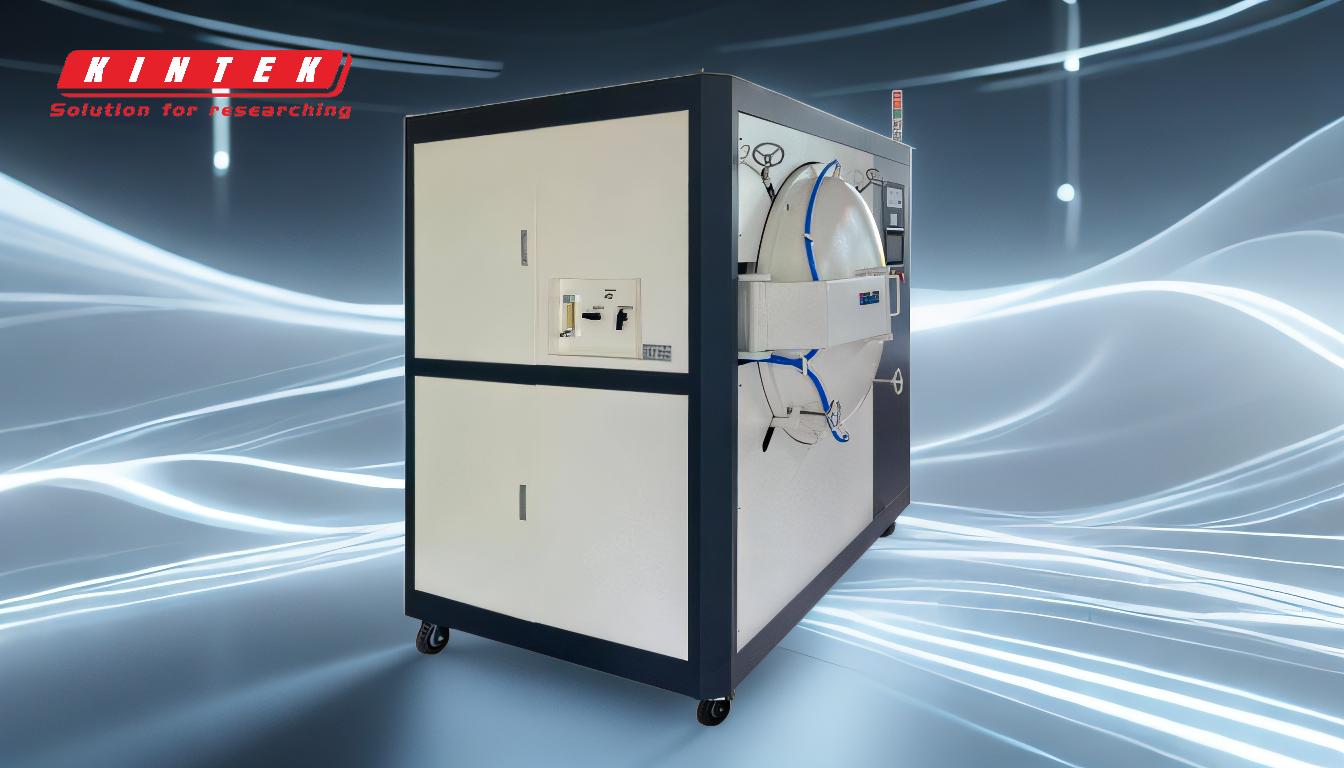
-
Definition of Sintering and Melting:
- Sintering: A process where particles of a material are fused together using heat and pressure, but without reaching the material's melting point. This allows the material to retain its solid state while achieving bonding at the particle level.
- Melting: A process where a material is heated to its melting point, causing it to transition from a solid to a liquid state. This requires sufficient thermal energy to overcome the material's internal bonds.
-
Temperature Relationship:
- Sintering temperatures are always below the material's melting point. This is because sintering relies on partial diffusion and bonding of particles without complete liquefaction.
- The melting point is the threshold temperature at which a material changes from solid to liquid. Sintering avoids this threshold to maintain the material's structural integrity.
-
Energy Requirements:
- Sintering requires less thermal energy compared to melting since it does not involve the complete breakdown of the material's internal structure.
- Melting demands significantly more energy to overcome the cohesive forces holding the material's atoms or molecules together in a solid state.
-
Process Mechanisms:
- Sintering: Combines heat and pressure to compact and bond particles. The process can be fine-tuned to achieve specific material properties, such as porosity, density, and strength.
- Melting: Primarily driven by temperature, leading to a complete phase change. The material becomes fully liquid, allowing for casting or molding into new shapes.
-
Material Outcomes:
- Sintering results in materials with controlled porosity and microstructure. It is often used in powder metallurgy, ceramics, and additive manufacturing to create complex shapes with precise properties.
- Melting produces materials with a homogeneous liquid phase, which can be cast or molded but may lose some of the original material's structural characteristics upon solidification.
-
Advantages of Sintering Over Melting:
- Greater control over material properties, such as porosity and grain size.
- Lower energy consumption due to the absence of liquefaction.
- Ability to process materials that are difficult to melt or have high melting points.
-
Applications:
- Sintering is widely used in industries such as automotive (for engine components), aerospace (for lightweight parts), and electronics (for conductive pastes).
- Melting is essential in processes like metal casting, glass manufacturing, and plastic molding.
-
Microstructural Differences:
- Sintered materials may retain microscopic gaps or pores, which can be advantageous for applications requiring controlled porosity, such as filters or catalysts.
- Melted materials typically have a denser, more uniform structure due to the complete breakdown of particle boundaries during liquefaction.
In summary, the relationship between sintering temperature and melting point is defined by the need to keep sintering temperatures below the melting point to avoid liquefaction while achieving particle bonding. This distinction allows for precise control over material properties and makes sintering a versatile and energy-efficient process for a wide range of industrial applications.
Summary Table:
Aspect | Sintering | Melting |
---|---|---|
Temperature | Below the material's melting point | At or above the material's melting point |
Energy Requirements | Lower energy, no liquefaction | Higher energy, complete phase change |
Process Mechanism | Heat and pressure bond particles; retains solid state | Temperature-driven; transforms solid to liquid |
Material Outcomes | Controlled porosity, microstructure, and precise properties | Homogeneous liquid phase; may lose structural characteristics upon cooling |
Applications | Automotive, aerospace, electronics, powder metallurgy, ceramics | Metal casting, glass manufacturing, plastic molding |
Advantages | Energy-efficient, greater control over properties, processes high-melt materials | Suitable for casting and molding |
Need help optimizing your material processing? Contact our experts today for tailored solutions!