Sintering is a critical process in powder metallurgy that involves heating compacted metal powders to a temperature below their melting point. This process bonds the particles together, enhancing the material's strength, density, and structural integrity, ultimately transforming the powder into a solid, usable component. Sintering ensures the final product meets the required mechanical and dimensional specifications, making it indispensable in the production of high-performance parts.
Key Points Explained:
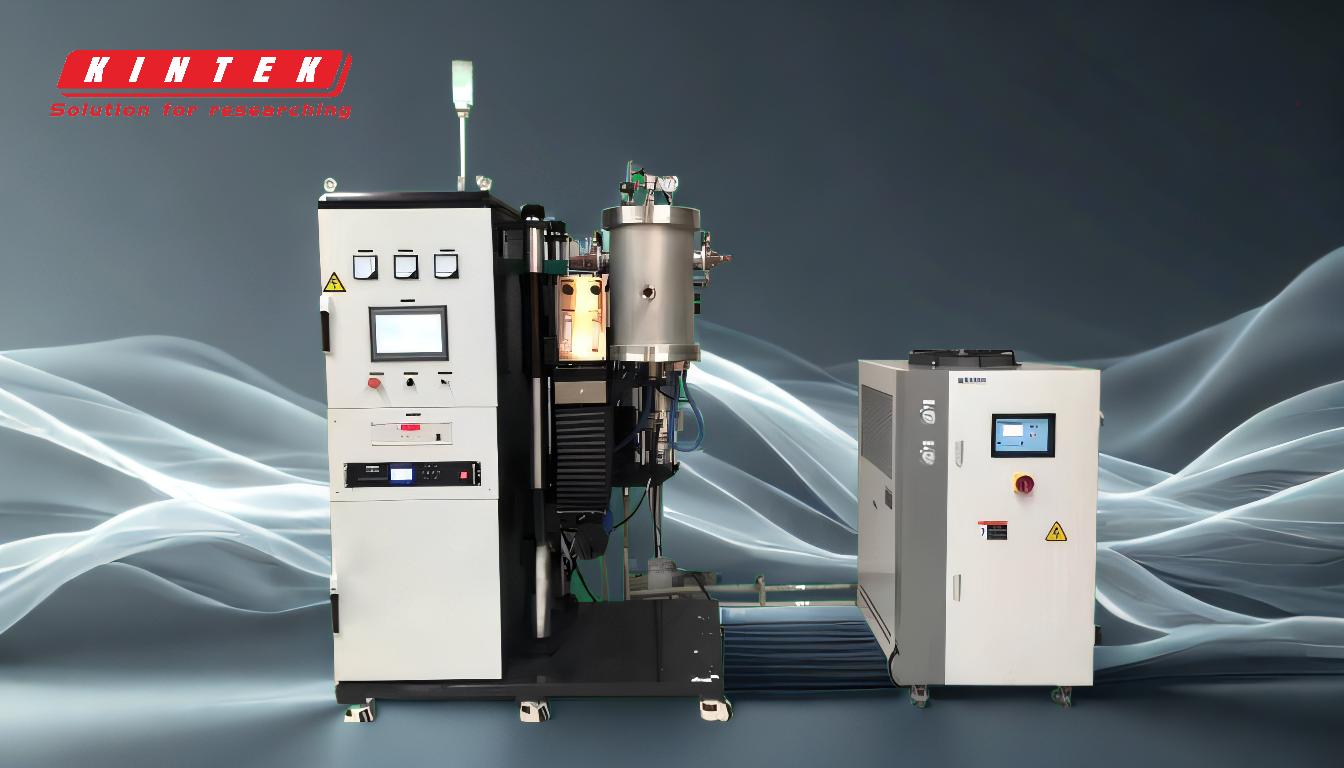
-
Definition and Purpose of Sintering:
- Sintering is a heat treatment process used in powder metallurgy to bond metal powder particles together without melting them. This process imparts mechanical strength, density, and structural integrity to the compacted powder, transforming it into a solid, functional component. The temperature used is typically below the melting point of the primary material, ensuring the powder particles fuse while maintaining their shape.
-
Role in Powder Metallurgy:
- Sintering is a key step in powder metallurgy that bridges the gap between powder compaction and the final product. It ensures the accuracy, durability, and performance of the manufactured parts. By bonding the particles, sintering enhances the material's properties, making it suitable for end-use applications in industries such as automotive, aerospace, and electronics.
-
Mechanical Strength and Density:
- During sintering, the powder particles undergo diffusion, which reduces porosity and increases density. This results in a stronger, more durable material. The process also improves the translucency and stability of the workpiece, making it capable of withstanding mechanical stresses and environmental conditions.
-
Temperature Control:
- Sintering is carried out at temperatures slightly below the melting point of the material. This precise temperature control is crucial to ensure the particles bond effectively without causing deformation or melting. The use of specialized equipment, such as a sintering furnace, allows for accurate temperature regulation and uniform heating.
-
Applications and Benefits:
- Sintering is widely used to produce complex, high-precision components with excellent mechanical properties. It enables the creation of parts with intricate geometries that would be difficult or impossible to achieve through traditional manufacturing methods. The process also reduces material waste and allows for the use of a wide range of metal powders, including alloys and composites.
-
Importance in Final Product Quality:
- The success of the sintering process directly impacts the quality of the final product. Proper sintering ensures the part meets dimensional tolerances, mechanical strength requirements, and surface finish specifications. This makes it a vital step in the production of reliable and high-performance components.
By understanding the role of sintering in powder metallurgy, manufacturers can optimize the process to produce superior parts with enhanced properties and performance. The use of advanced sintering techniques and equipment, such as a sintering furnace, further ensures the consistency and quality of the final product.
Summary Table:
Aspect | Description |
---|---|
Definition | Sintering bonds metal powder particles without melting, enhancing strength and density. |
Role in Powder Metallurgy | Bridges powder compaction to final product, ensuring accuracy and durability. |
Mechanical Strength | Reduces porosity, increases density, and improves material stability. |
Temperature Control | Conducted below melting point for effective bonding without deformation. |
Applications | Produces complex, high-precision parts for industries like automotive and aerospace. |
Final Product Quality | Ensures dimensional tolerances, mechanical strength, and surface finish. |
Optimize your powder metallurgy process with advanced sintering techniques—contact our experts today!