The rotational speed of a rotary kiln, measured in revolutions per minute (rpm), is a critical operational parameter that influences material flow, heat transfer, and overall process efficiency. Rotary kilns generally operate at speeds ranging from 0.5 to 2 rpm, with some modern cement plant kilns running faster at 4 to 5 rpm. The rotation speed is proportional to the material flow rate through the kiln, ensuring proper mixing, heating, and chemical reactions. Factors such as kiln design, material properties, and process requirements determine the optimal rpm. Understanding these dynamics is essential for equipment purchasers to select a kiln that meets specific operational needs.
Key Points Explained:
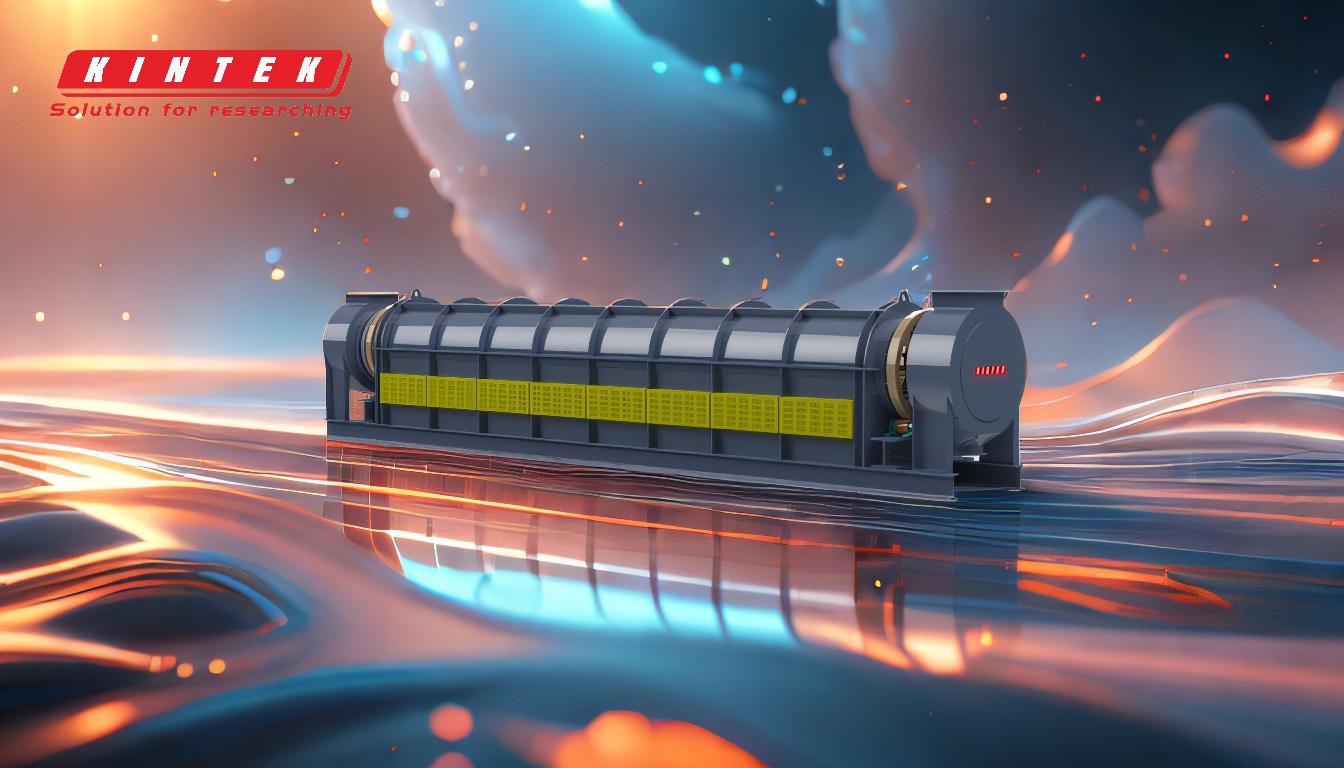
-
Typical RPM Range for Rotary Kilns:
- Rotary kilns usually operate at a rotational speed of 0.5 to 2 rpm. This range is suitable for most industrial applications, including calcination, drying, and chemical processing.
- Modern cement plant kilns, however, often run at higher speeds of 4 to 5 rpm to accommodate faster material processing and increased production demands.
-
Factors Influencing RPM:
- Material Flow Rate: The rotation speed directly affects the speed at which materials move through the kiln. Faster rotation speeds result in quicker material flow, while slower speeds allow for longer retention times.
- Process Requirements: Different processes, such as calcination or sintering, may require specific rpm settings to achieve optimal heat transfer and chemical reactions.
- Kiln Design: The size, tilt angle, and internal configuration of the kiln influence the ideal rotation speed. For example, larger kilns may require slower speeds to ensure uniform heating.
-
Impact of RPM on Kiln Operation:
- Heat Transfer: Proper rotation ensures consistent mixing and exposure of materials to hot gases, enhancing heat transfer efficiency.
- Retention Time: The rpm determines how long materials remain in the kiln, which is critical for achieving desired chemical or physical transformations.
- Energy Efficiency: Optimizing rpm can reduce energy consumption by minimizing unnecessary heat loss and improving process control.
-
Modern Trends in Kiln RPM:
- In cement plants, higher rotation speeds (4–5 rpm) are increasingly common due to advancements in kiln design and process optimization. These speeds enable faster production rates while maintaining product quality.
- Advanced control systems allow for precise adjustment of rpm to match specific process conditions, improving flexibility and efficiency.
-
Considerations for Equipment Purchasers:
- Process Compatibility: Ensure the kiln's rpm range aligns with the intended application and material characteristics.
- Energy Consumption: Evaluate how different rpm settings impact energy usage and operational costs.
- Maintenance and Durability: Higher rpm may increase wear and tear on kiln components, so consider the long-term maintenance requirements.
By understanding the role of rpm in rotary kiln operation, purchasers can make informed decisions that balance production efficiency, energy consumption, and equipment longevity.
Summary Table:
Aspect | Details |
---|---|
Typical RPM Range | 0.5–2 rpm (industrial), 4–5 rpm (modern cement plants) |
Factors Influencing RPM | Material flow rate, process requirements, kiln design |
Impact of RPM | Heat transfer, retention time, energy efficiency |
Modern Trends | Higher speeds (4–5 rpm) for faster production and advanced control systems |
Purchasing Tips | Process compatibility, energy consumption, maintenance considerations |
Ready to optimize your rotary kiln operation? Contact us today for expert guidance!