Sintering is a critical process in materials science and manufacturing, particularly for ceramics and metals, as it significantly influences the microstructure and properties of the final product. By heating powdered materials below their melting points, sintering reduces porosity, enhances density, and improves mechanical, electrical, and thermal properties. This process enables the creation of complex shapes and geometries, combines desirable material properties, and facilitates cost-effective mass production. Sintering is essential for achieving strength, durability, and precision in components, making it indispensable in industries requiring high-performance materials.
Key Points Explained:
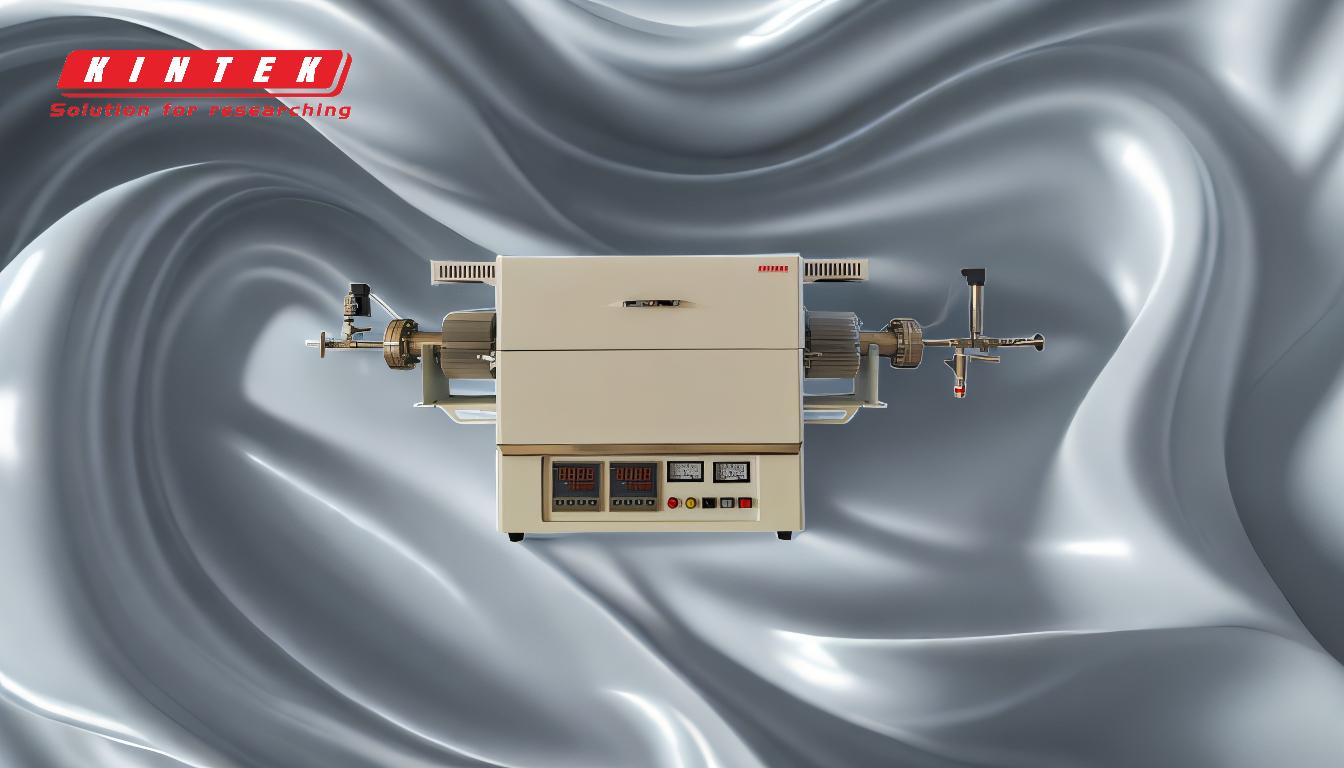
-
Microstructural Transformation:
- Sintering directly impacts the grain size, pore size, and grain boundary distribution in materials. These microstructural changes enhance the material's strength, durability, and other mechanical properties.
- By reducing porosity and increasing density, sintering ensures the material achieves its optimal performance characteristics.
-
Enhanced Material Properties:
- Sintering improves properties such as hardness, toughness, abrasion resistance, electrical conductivity, translucency, and thermal conductivity.
- The process allows materials to retain their desirable properties without requiring melting, which is particularly beneficial for metals with high melting points.
-
Complex Geometries and Precision:
- Sintering enables the production of intricate shapes and geometries that are difficult or impossible to achieve with traditional manufacturing methods.
- It ensures high precision and repeatability, making it ideal for mass production of complex parts.
-
Cost-Effective Manufacturing:
- The process reduces the need for expensive tooling, lowering overall production costs.
- It supports rapid mass production while maintaining consistent quality and precision.
-
Combination of Material Properties:
- Sintering allows the merging of properties from multiple materials, such as combining toughness with abrasion resistance, to create advanced materials tailored for specific applications.
-
Critical Role in Metal Injection Molding (MIM):
- In MIM, sintering is the most crucial step, as it determines the final density, mechanical properties, and surface quality of the part.
- The use of high-purity hydrogen during sintering helps reduce surface oxides and impurities, further enhancing material performance.
-
Versatility Across Industries:
- Sintering is widely used in industries such as automotive, aerospace, electronics, and medical devices, where high-performance materials with precise specifications are required.
By understanding these key points, it becomes clear why sintering is a cornerstone of modern materials engineering and manufacturing, enabling the creation of high-quality, durable, and cost-effective components.
Summary Table:
Key Benefits of Sintering | Details |
---|---|
Microstructural Transformation | Enhances grain size, pore size, and grain boundaries for improved strength and durability. |
Enhanced Material Properties | Improves hardness, toughness, conductivity, and thermal properties without melting. |
Complex Geometries | Enables intricate shapes and high-precision manufacturing for mass production. |
Cost-Effective Manufacturing | Reduces tooling costs and supports rapid, consistent production. |
Combination of Material Properties | Merges properties like toughness and abrasion resistance for advanced materials. |
Role in Metal Injection Molding (MIM) | Determines density, mechanical properties, and surface quality in MIM parts. |
Versatility Across Industries | Used in automotive, aerospace, electronics, and medical devices for high-performance components. |
Learn how sintering can optimize your material performance—contact us today!