The sintering cycle is a critical process in materials science and manufacturing, where powdered materials are transformed into dense, solid bodies through the application of heat and pressure, without reaching the material's melting point. This process is widely used in industries such as powder metallurgy, ceramics, and plastics to create durable and cohesive products. The sintering cycle typically involves several stages, including powder preparation, compaction, and controlled heating, followed by cooling. Each stage plays a vital role in ensuring the final product's structural integrity and desired properties.
Key Points Explained:
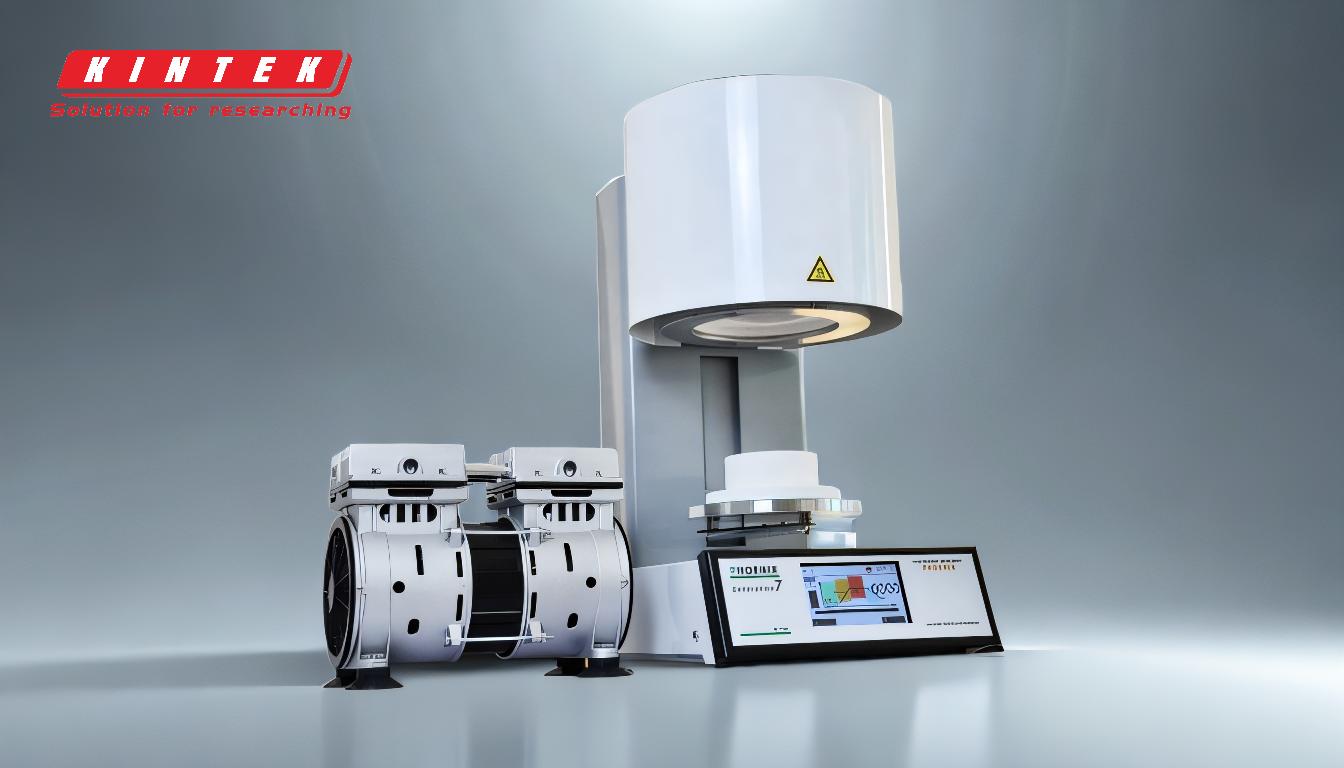
-
Definition and Purpose of Sintering:
- Sintering is a process that fuses small particles into a solid mass without melting the material. It is used to create dense, durable products from powdered materials such as metals, ceramics, and plastics.
- The primary purpose of sintering is to bond adjacent powder particles, resulting in a cohesive structure with improved mechanical properties like strength, hardness, and durability.
-
Stages of the Sintering Cycle:
-
Powder Preparation:
- The process begins with the preparation of raw materials in powder form. This may involve mixing powders with additives like binders, deflocculants, and water to create a slurry, which is then spray-dried to form granules.
-
Compaction:
- The prepared powder is compacted using mechanical pressure, either through cold or hot pressing, to form a "green" part. This stage ensures uniformity and eliminates voids in the material.
-
Sintering (Firing):
- The green part is heated in a controlled environment, typically in a sintering furnace or kiln. The temperature is carefully regulated to facilitate particle bonding through diffusion, leading to neck formation and densification. The material does not melt but undergoes atomic diffusion, which fuses the particles together.
-
Cooling:
- After sintering, the material is cooled gradually to allow it to solidify into a rigid and cohesive structure. This stage is crucial for achieving the desired mechanical properties and preventing defects.
-
Powder Preparation:
-
Key Factors Influencing the Sintering Process:
-
Temperature:
- The sintering temperature must be high enough to promote particle bonding but below the material's melting point to avoid liquefaction.
-
Pressure:
- Applied pressure during compaction ensures uniform density and reduces porosity in the green part.
-
Time:
- The duration of sintering affects the degree of particle bonding and densification. Longer sintering times generally result in stronger bonds but must be balanced against energy consumption and production efficiency.
-
Atmosphere:
- The sintering environment (e.g., inert gas, vacuum, or air) can influence the final properties of the material by preventing oxidation or facilitating specific chemical reactions.
-
Temperature:
-
Applications of Sintering:
-
Powder Metallurgy:
- Sintering is widely used to produce metal components such as gears, bearings, and automotive parts. It allows for the creation of complex shapes with high precision and minimal waste.
-
Ceramics:
- In the ceramics industry, sintering is used to produce tiles, insulators, and other products with high thermal and mechanical stability.
-
Plastics and Composites:
- Sintering is employed to create durable plastic components and composite materials with tailored properties.
-
Powder Metallurgy:
-
Advantages of Sintering:
-
Cost-Effectiveness:
- Sintering reduces material waste and allows for the production of near-net-shape components, minimizing the need for additional machining.
-
Material Versatility:
- The process can be applied to a wide range of materials, including metals, ceramics, and polymers.
-
Enhanced Properties:
- Sintered products exhibit improved mechanical strength, hardness, and wear resistance due to the densification and bonding of particles.
-
Cost-Effectiveness:
-
Challenges and Considerations:
-
Control of Process Parameters:
- Achieving consistent results requires precise control of temperature, pressure, and time, which can be challenging in large-scale production.
-
Material Limitations:
- Not all materials are suitable for sintering, particularly those with low melting points or poor thermal stability.
-
Equipment Costs:
- Sintering furnaces and presses can be expensive, particularly for high-temperature or high-pressure applications.
-
Control of Process Parameters:
In summary, the sintering cycle is a versatile and essential process in modern manufacturing, enabling the production of high-performance materials and components. By understanding the stages, influencing factors, and applications of sintering, manufacturers can optimize the process to meet specific product requirements and achieve superior results.
Summary Table:
Aspect | Details |
---|---|
Definition | Fuses powder particles into a solid mass without melting the material. |
Stages | Powder Preparation, Compaction, Sintering (Firing), Cooling. |
Key Factors | Temperature, Pressure, Time, Atmosphere. |
Applications | Powder Metallurgy, Ceramics, Plastics, and Composites. |
Advantages | Cost-effective, Material versatility, Enhanced mechanical properties. |
Challenges | Precise parameter control, Material limitations, High equipment costs. |
Optimize your sintering process with expert guidance—contact us today!