Sintering is a critical process in ceramic manufacturing, where ceramic powders are compacted and heated to form a dense, cohesive structure. The process involves several steps, including powder preparation, shaping, heating, and cooling, to achieve the desired physical and mechanical properties. Sintering transforms the ceramic powder into a solid, low-porosity material by bonding particles at high temperatures, often below the melting point of the primary material. This method ensures the final product has structural integrity and specific functional characteristics.
Key Points Explained:
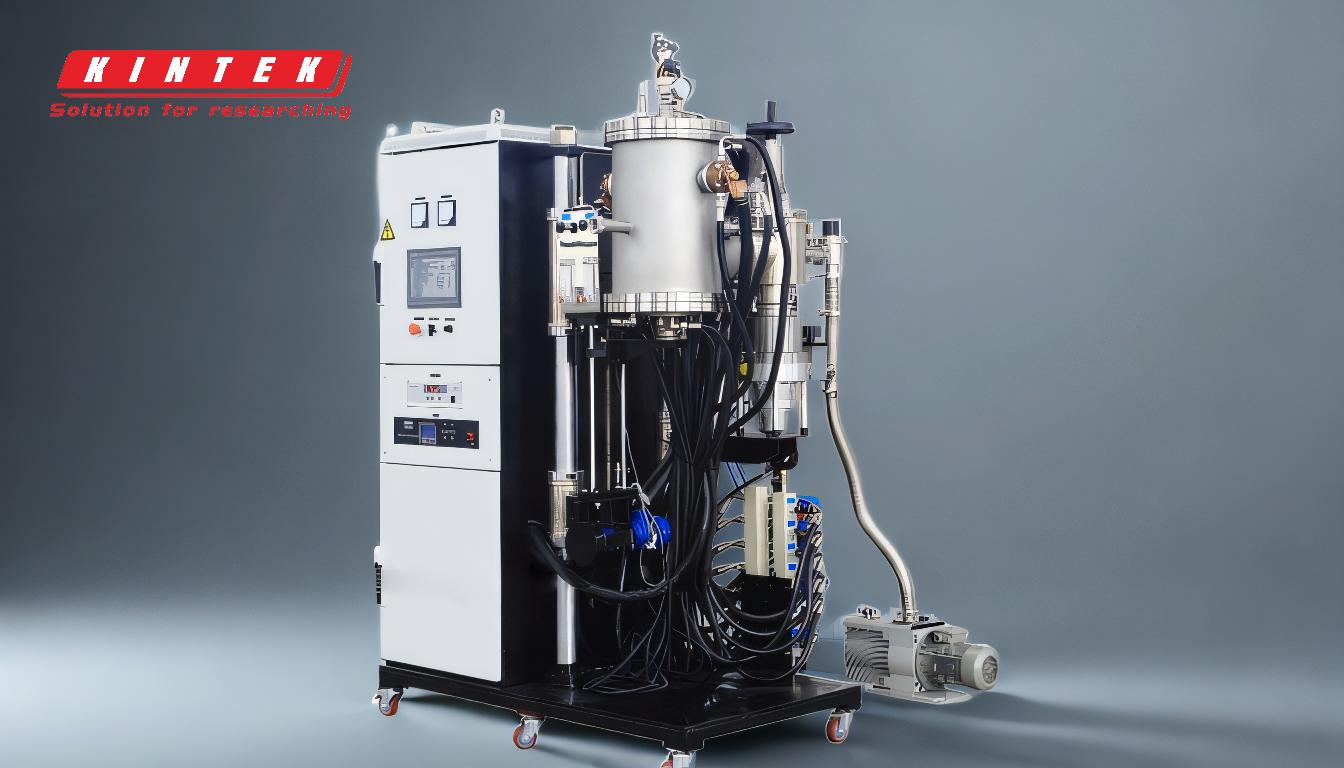
-
Powder Preparation
- The process begins with preparing the ceramic powder, which involves mixing raw materials, binders, and additives to achieve a homogeneous mixture.
- Binders and deflocculants are added to improve the flowability and compaction of the powder.
- The mixture is often spray-dried to form granules, which are easier to handle and press into molds.
-
Shaping (Pressing)
- The prepared powder is compacted into a desired shape using pressing tools or molds. This step forms a "green body," which is a fragile, pre-sintered structure.
- Pressing can be done using methods like uniaxial pressing, isostatic pressing, or 3D printing, depending on the complexity of the part.
-
Binder Removal (Debinding)
- The green body is heated at a low temperature to remove binders and other volatile components. This step is crucial to prevent defects during sintering.
- The temperature is carefully controlled to avoid cracking or warping of the green body.
-
Sintering (Heating and Consolidation)
- The green body is heated to a high temperature, typically just below the melting point of the ceramic material. This allows the particles to bond and densify.
- Sintering can occur in different stages:
- Initial Stage: Particles begin to bond at contact points.
- Intermediate Stage: Pores shrink, and the material densifies.
- Final Stage: Grain growth occurs, and the material reaches its final density.
- Liquid phase sintering (LPS) may be used to accelerate densification by introducing a liquid phase that fills pores and promotes particle bonding.
-
Cooling and Solidification
- After sintering, the material is cooled slowly to room temperature to prevent thermal stresses and cracking.
- The cooling rate is controlled to ensure the material solidifies into a unified, dense structure.
-
Post-Sintering Processes
- Machining: Sintered ceramics are often machined using diamond tools or ultrasonic methods to achieve precise dimensions and surface finishes.
- Assembly: Ceramic parts may be metallized and brazed to other components for specific applications.
-
Key Parameters in Sintering
- Temperature: Must be carefully controlled to ensure proper bonding without melting the material.
- Atmosphere: Sintering is often performed in a controlled atmosphere (e.g., inert gas or vacuum) to prevent oxidation or contamination.
- Time: The duration of sintering affects the density and grain size of the final product.
- Pressure: In some cases, pressure is applied during sintering (hot pressing) to enhance densification.
-
Applications and Importance
- Sintered ceramics are used in a wide range of industries, including electronics, aerospace, automotive, and medical devices.
- The sintering process ensures the final product has high strength, wear resistance, thermal stability, and electrical insulation properties.
By following these steps and controlling key parameters, the sintering method transforms ceramic powders into high-performance materials suitable for demanding applications.
Summary Table:
Step | Description |
---|---|
Powder Preparation | Mixing raw materials, binders, and additives to form a homogeneous mixture. |
Shaping (Pressing) | Compacting powder into molds to create a fragile "green body." |
Binder Removal | Heating to remove binders and prevent defects during sintering. |
Sintering | Heating to high temperatures to bond particles and densify the material. |
Cooling | Controlled cooling to solidify the material into a dense, unified structure. |
Post-Sintering | Machining and assembly to achieve precise dimensions and functional properties. |
Key Parameters | Temperature, atmosphere, time, and pressure are critical for optimal results. |
Transform your ceramic manufacturing process—contact our experts today for tailored solutions!