The sintering temperature of polymers is a critical parameter in processes like selective laser sintering (SLS) and other additive manufacturing techniques. It generally ranges between 100°C to 300°C, depending on the type of polymer and its thermal properties. For instance, semi-crystalline polymers like polyamide (PA) typically sinter at temperatures just below their melting point, around 170°C to 190°C, while amorphous polymers like polystyrene require lower temperatures. The sintering temperature must be carefully controlled to ensure proper particle fusion without degradation. Factors influencing this temperature include polymer composition, molecular weight, and the presence of additives. Understanding these factors is essential for optimizing the sintering process and achieving high-quality parts.
Key Points Explained:
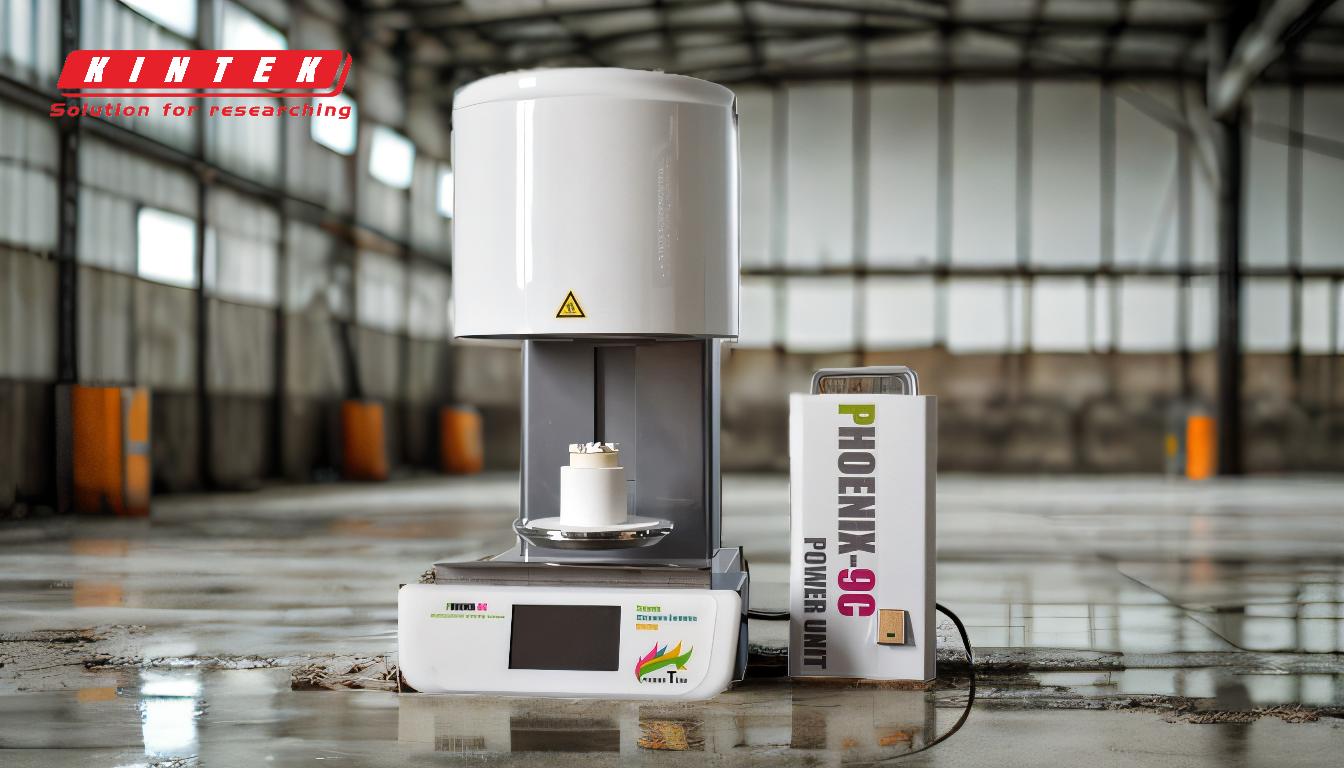
-
Definition of Sintering Temperature in Polymers:
- Sintering temperature refers to the temperature at which polymer particles fuse together to form a solid structure without fully melting. This is crucial in additive manufacturing processes like SLS, where precise temperature control ensures part integrity and dimensional accuracy.
-
Typical Sintering Temperature Range:
- Polymers generally sinter between 100°C to 300°C, depending on their thermal properties.
- Semi-crystalline polymers, such as polyamide (PA), sinter at temperatures close to their melting point, typically 170°C to 190°C.
- Amorphous polymers, like polystyrene, require lower sintering temperatures due to their lack of a distinct melting point.
-
Factors Influencing Sintering Temperature:
- Polymer Composition: The chemical structure of the polymer determines its thermal behavior. For example, PA12 (a common SLS material) has a lower sintering temperature compared to PA6 due to differences in crystallinity.
- Molecular Weight: Higher molecular weight polymers often require higher sintering temperatures due to increased chain entanglement.
- Additives: Fillers, plasticizers, or stabilizers can alter the sintering temperature by modifying the polymer's thermal properties.
-
Importance of Temperature Control:
- Too Low: Insufficient sintering leads to weak inter-particle bonding, resulting in porous or brittle parts.
- Too High: Excessive temperatures can cause polymer degradation, warping, or unwanted melting, compromising part quality.
-
Examples of Sintering Temperatures for Common Polymers:
- Polyamide (PA12): Sinters at 170°C to 190°C.
- Polystyrene (PS): Sinters at 100°C to 120°C.
- Polyetheretherketone (PEEK): Requires higher sintering temperatures, typically 340°C to 380°C, due to its high thermal stability.
-
Practical Considerations for Equipment and Consumable Purchasers:
- Material Selection: Choose polymers with sintering temperatures compatible with your equipment's capabilities.
- Process Optimization: Ensure your sintering equipment can maintain precise temperature control to avoid defects.
- Cost and Availability: Consider the cost and availability of polymers with suitable sintering temperatures for your application.
By understanding these key points, purchasers and engineers can make informed decisions about material selection and process optimization, ensuring successful sintering outcomes.
Summary Table:
Polymer Type | Sintering Temperature Range |
---|---|
Polyamide (PA12) | 170°C to 190°C |
Polystyrene (PS) | 100°C to 120°C |
PEEK | 340°C to 380°C |
Semi-Crystalline | Close to melting point |
Amorphous | Lower temperatures |
Factors Influencing | Composition, molecular weight, additives |
Need help selecting the right polymer for your sintering process? Contact our experts today for personalized guidance!