Spark Plasma Sintering (SPS) is an advanced powder metallurgy technique used to consolidate powder materials into dense, solid structures. It combines pulsed direct current (DC) and axial pressure to rapidly heat and sinter materials at high temperatures, often reaching up to 10,000°C (18,032°F). This process generates localized plasma and high temperatures between particles, facilitating surface diffusion, particle bonding, and rapid densification. SPS is known for its fast heating rates, uniform heating, and ability to achieve near-theoretical density (over 99%) in materials. Despite its name, research indicates that plasma may not be the primary mechanism, leading to alternative names such as Field Assisted Sintering Technique (FAST) or Direct Current Sintering (DCS). SPS is widely used for ceramics, metals, and composites due to its efficiency and ability to sinter materials at lower temperatures and shorter times compared to conventional methods.
Key Points Explained:
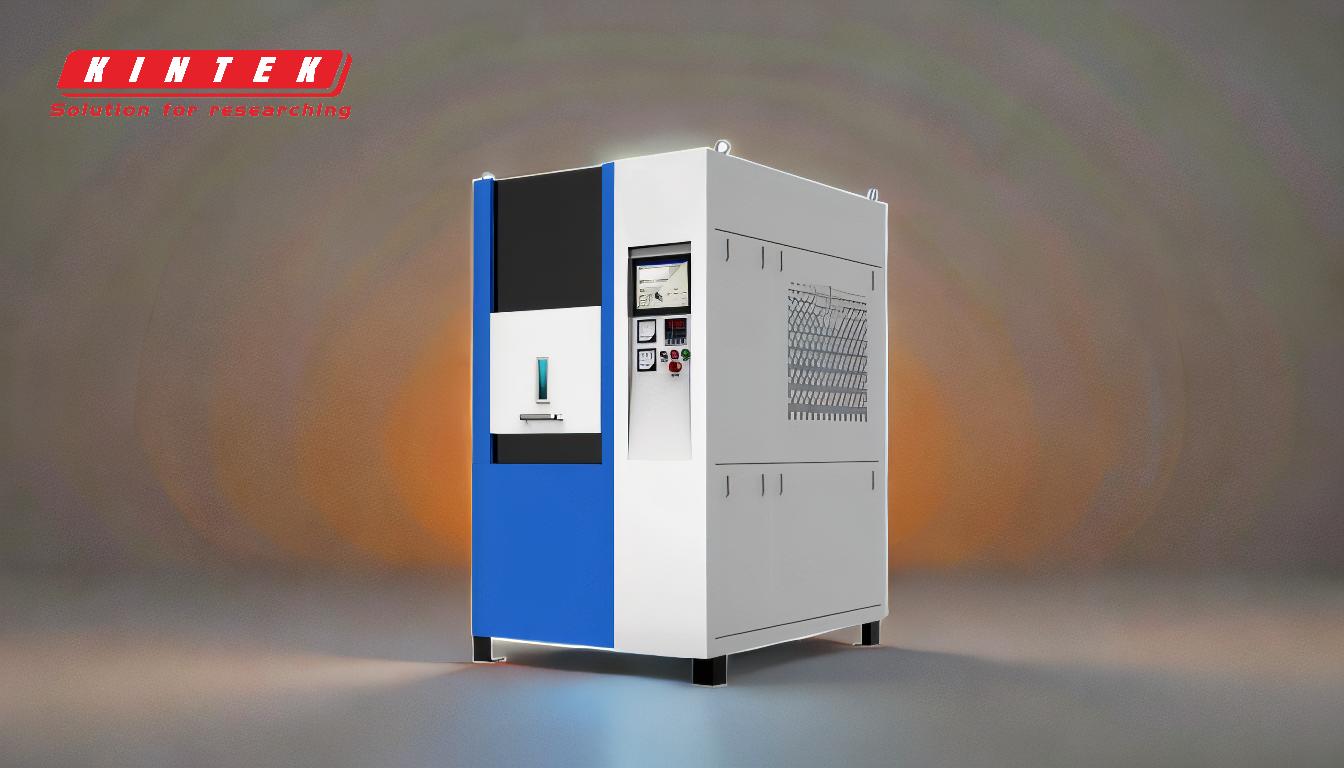
-
Definition and Purpose of SPS:
- Spark Plasma Sintering (SPS) is a powder consolidation technique that uses pulsed DC and axial pressure to rapidly sinter powder materials into dense, solid structures.
- It is particularly useful for achieving high-density materials with minimal porosity, often exceeding 99% density.
-
Mechanism of SPS:
- Pulsed DC and Spark Discharge: A high-energy pulsed current is applied, creating electric spark discharges between particles. This generates localized plasma and extremely high temperatures (up to 10,000°C or 18,032°F).
- Particle Bonding: The high temperatures cause particle surfaces to melt and fuse, forming "necks" between particles. Over time, these necks grow, increasing the material's overall density.
- Contaminant Removal: The intense heat can oxidize or evaporate surface contaminants, ensuring cleaner particle bonding.
-
Key Advantages of SPS:
- Fast Heating and Cooling Rates: SPS allows for rapid heating and cooling, significantly reducing processing time compared to conventional sintering methods.
- Lower Sintering Temperatures: The process achieves densification at temperatures several hundred degrees lower than traditional sintering, preserving material properties.
- Uniform Heating: The combination of internal and external heating ensures uniform temperature distribution, reducing thermal stress and improving material consistency.
-
Equipment and Process Details:
- Conducting Die: A graphite die is typically used to apply pressure and conduct the pulsed DC current. The die acts as both a heat source and a pressure applicator.
- Power Control Device: A specialized device applies ON-OFF DC pulse voltage to the powder sample, generating discharge plasma and utilizing Joule heating for rapid densification.
- Pressure Application: Axial pressure is applied concurrently with the electric current to enhance particle bonding and densification.
-
Applications of SPS:
- Ceramics and Metals: SPS is widely used for sintering ceramics, metals, and composites, producing high-performance materials with superior mechanical, thermal, and electrical properties.
- Nanomaterials: The process is particularly effective for consolidating nanomaterials, as it prevents grain growth and preserves nanostructures.
-
Misconceptions and Alternative Names:
- Plasma Misconception: Despite its name, research suggests that plasma may not be the primary mechanism in SPS. Instead, the process relies on electric discharge and Joule heating.
- Alternative Names: Due to this misconception, SPS is also referred to as Field Assisted Sintering Technique (FAST), Electric Field Assisted Sintering (EFAS), or Direct Current Sintering (DCS).
-
Comparison with Conventional Sintering:
- Time Efficiency: SPS significantly reduces sintering time, often completing the process in minutes rather than hours.
- Temperature Efficiency: Lower sintering temperatures in SPS help preserve material properties and reduce energy consumption.
- Density and Quality: SPS achieves higher densities and better material quality compared to conventional sintering methods.
-
Challenges and Considerations:
- Material Conductivity: Materials with low electrical conductivity may require conductive additives or alternative heating methods.
- Equipment Cost: The specialized equipment for SPS can be expensive, making it less accessible for some applications.
- Process Optimization: Achieving optimal results requires careful control of parameters such as current, pressure, and temperature.
By understanding these key points, equipment and consumable purchasers can better evaluate the suitability of SPS for their specific material processing needs and make informed decisions about adopting this advanced sintering technique.
Summary Table:
Key Aspect | Details |
---|---|
Definition | Advanced powder metallurgy technique using pulsed DC and axial pressure. |
Mechanism | Generates localized plasma and high temperatures for particle bonding. |
Advantages | Fast heating, lower sintering temperatures, and uniform heating. |
Applications | Ceramics, metals, composites, and nanomaterials. |
Alternative Names | Field Assisted Sintering Technique (FAST), Direct Current Sintering (DCS). |
Comparison with Conventional Methods | Faster, lower temperatures, higher density, and better quality. |
Ready to enhance your material processing? Contact us today to learn more about Spark Plasma Sintering!