Sputter coating is a critical preparatory technique in scanning electron microscopy (SEM) used to deposit a thin, conductive layer of material onto non-conductive or poorly conductive samples. This process enhances the sample's conductivity, reduces charging effects caused by the electron beam, and improves the quality of imaging by increasing secondary electron emission. Common materials used for sputter coating include gold, platinum, and carbon, each chosen based on specific analytical needs. Gold is favored for its high conductivity and fine grain size, while carbon is preferred for energy-dispersive X-ray (EDX) analysis due to its non-interfering X-ray peak. The process ensures that samples are representative and protected during SEM analysis.
Key Points Explained:
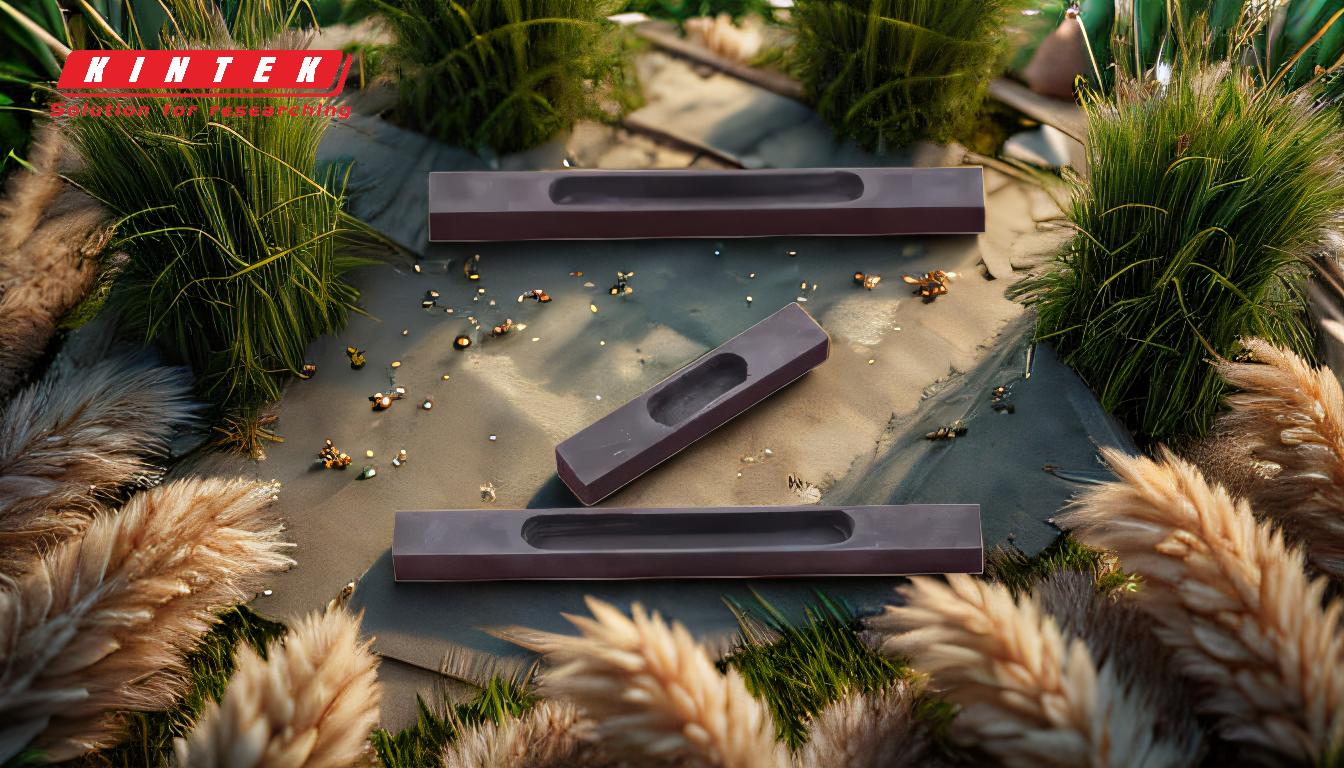
-
Purpose of Sputter Coating in SEM:
- Sputter coating is primarily used to prepare non-conductive or poorly conductive samples for SEM analysis. The technique involves depositing a thin layer of conductive material (typically 2-20 nanometers thick) onto the sample surface. This coating prevents charging effects caused by the electron beam, which can distort imaging and damage the sample. Additionally, it enhances the secondary electron signal, improving the clarity and resolution of the SEM images.
-
Materials Used in Sputter Coating:
- The choice of coating material depends on the specific requirements of the analysis. Common materials include:
- Gold (Au): Widely used due to its high conductivity and small grain size, which minimizes interference with the sample's surface features.
- Platinum (Pt) and Palladium (Pd): Often used in alloys (e.g., gold/palladium) for their durability and resistance to oxidation.
- Carbon (C): Preferred for EDX analysis because its X-ray peak does not overlap with those of other elements, making it ideal for compositional studies.
- Other materials like silver, chromium, tungsten, and iridium are also used depending on the application.
- The choice of coating material depends on the specific requirements of the analysis. Common materials include:
-
Benefits of Sputter Coating:
- Improved Conductivity: The conductive layer allows the electron beam to interact with the sample without causing charging artifacts.
- Enhanced Imaging: By increasing secondary electron emission, sputter coating improves the contrast and resolution of SEM images.
- Sample Protection: The coating provides a protective barrier, reducing thermal damage and beam-induced degradation of the sample.
-
Process of Sputter Coating:
- Sputter coating involves placing the sample in a vacuum chamber and bombarding a target material (e.g., gold or platinum) with ions. This causes atoms from the target to be ejected and deposited onto the sample surface, forming a uniform, ultra-thin layer. The process is carefully controlled to ensure the desired thickness and uniformity of the coating.
-
Applications in SEM:
- Sputter coating is essential for analyzing biological samples, polymers, ceramics, and other non-conductive materials in SEM. It enables high-quality imaging and accurate compositional analysis, making it a vital step in materials science, life sciences, and industrial research.
By understanding the principles and applications of sputter coating, researchers can optimize their SEM workflows to achieve reliable and high-quality results.
Summary Table:
Aspect | Details |
---|---|
Purpose | Prepares non-conductive samples for SEM, prevents charging, enhances imaging |
Common Materials | Gold (Au), Platinum (Pt), Carbon (C), Palladium (Pd), and others |
Benefits | Improved conductivity, enhanced imaging, sample protection |
Process | Deposition of ultra-thin conductive layer in a vacuum chamber |
Applications | Biological samples, polymers, ceramics, and non-conductive materials |
Optimize your SEM analysis with sputter coating—contact our experts today for tailored solutions!