Sputtering deposition is a physical vapor deposition (PVD) technique used to create thin films by ejecting material from a target and depositing it onto a substrate. This process involves bombarding a target material with high-energy ions, typically from argon gas, in a vacuum environment. The ions dislodge atoms from the target, which then travel and deposit onto a substrate, forming a thin film. This method is widely used in industries such as semiconductors, optics, and coatings due to its ability to produce high-quality, uniform films with strong adhesion. Below, the key aspects of sputtering deposition are explained in detail.
Key Points Explained:
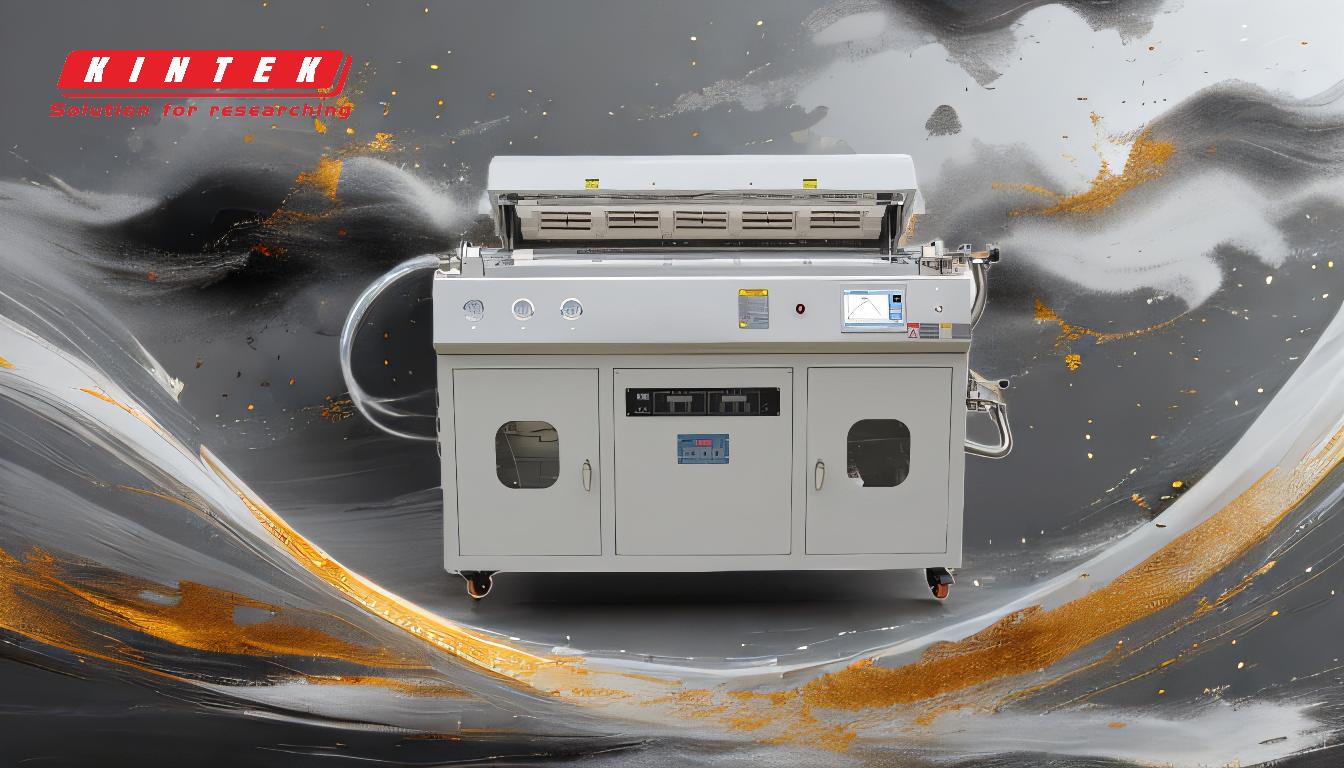
-
Definition and Process Overview:
- Sputtering deposition is a physical vapor deposition (PVD) method where material is ejected from a solid target and deposited onto a substrate.
- High-energy ions, usually argon, bombard the target, causing atoms to be ejected and travel to the substrate.
- The process occurs in a vacuum chamber to ensure controlled conditions and minimize contamination.
-
Mechanism of Sputtering:
- Ion Bombardment: Argon gas is ionized to form a plasma, and the ions are accelerated toward the target material.
- Ejection of Atoms: The high-energy ions collide with the target, transferring energy and ejecting atoms from the target surface.
- Deposition: The ejected atoms travel through the vacuum and deposit onto the substrate, forming a thin film.
-
Components of Sputtering Deposition:
- Target Material: The source material from which atoms are ejected. It is typically a metal or compound.
- Substrate: The surface onto which the ejected atoms are deposited, such as a silicon wafer or glass.
- Vacuum Chamber: Provides a controlled environment to prevent contamination and ensure efficient deposition.
- Power Supply: Generates the plasma and accelerates ions toward the target.
- Argon Gas: Commonly used as the sputtering gas due to its inert nature and ability to form a stable plasma.
-
Advantages of Sputtering Deposition:
- High-Quality Films: Produces uniform, dense, and adherent thin films.
- Versatility: Can deposit a wide range of materials, including metals, alloys, and compounds.
- Precision: Allows for precise control over film thickness and composition.
- Scalability: Suitable for both small-scale research and large-scale industrial applications.
-
Applications of Sputtering Deposition:
- Semiconductors: Used to deposit conductive and insulating layers in integrated circuits.
- Optics: Creates anti-reflective, reflective, and protective coatings for lenses and mirrors.
- Coatings: Provides wear-resistant, corrosion-resistant, and decorative coatings for various industries.
- Solar Cells: Deposits thin films for photovoltaic applications.
-
Types of Sputtering Deposition:
- DC Sputtering: Uses a direct current power supply, suitable for conductive materials.
- RF Sputtering: Uses radio frequency power, ideal for insulating materials.
- Magnetron Sputtering: Enhances efficiency by using magnetic fields to confine electrons near the target.
- Reactive Sputtering: Introduces reactive gases (e.g., oxygen or nitrogen) to form compound films.
-
Challenges and Considerations:
- Target Erosion: The target material gradually erodes, requiring periodic replacement.
- Contamination: Proper vacuum conditions and gas purity are critical to avoid impurities in the film.
- Energy Efficiency: High-energy processes can be energy-intensive, requiring optimization for cost-effectiveness.
-
Comparison with Other Deposition Methods:
- Thermal Evaporation: Sputtering provides better adhesion and uniformity compared to thermal evaporation.
- Chemical Vapor Deposition (CVD): Sputtering is a purely physical process, avoiding chemical reactions and potential contamination.
By understanding these key points, one can appreciate the complexity and versatility of sputtering deposition, making it a cornerstone technique in modern thin-film technology.
Summary Table:
Aspect | Details |
---|---|
Definition | Physical vapor deposition (PVD) technique for thin film production. |
Key Components | Target material, substrate, vacuum chamber, power supply, argon gas. |
Advantages | High-quality, uniform films; versatile; precise; scalable. |
Applications | Semiconductors, optics, coatings, solar cells. |
Types | DC, RF, magnetron, reactive sputtering. |
Challenges | Target erosion, contamination, energy efficiency. |
Discover how sputtering deposition can enhance your thin film production—contact our experts today!