The sputtering process is a plasma-based thin-film deposition technique widely used in industries such as semiconductor manufacturing, optics, and surface engineering. It involves the ejection of atoms from a solid target material through bombardment by high-energy ions, typically from a noble gas like argon. These ejected atoms then travel through a vacuum and deposit onto a substrate, forming a thin film. The process is highly controllable, allowing for precise deposition of materials with specific properties. Key steps include creating a vacuum, introducing an inert gas, ionizing the gas to form a plasma, and using a magnetic field to direct ions toward the target. The sputtered atoms then condense on the substrate, forming a uniform and adherent thin film.
Key Points Explained:
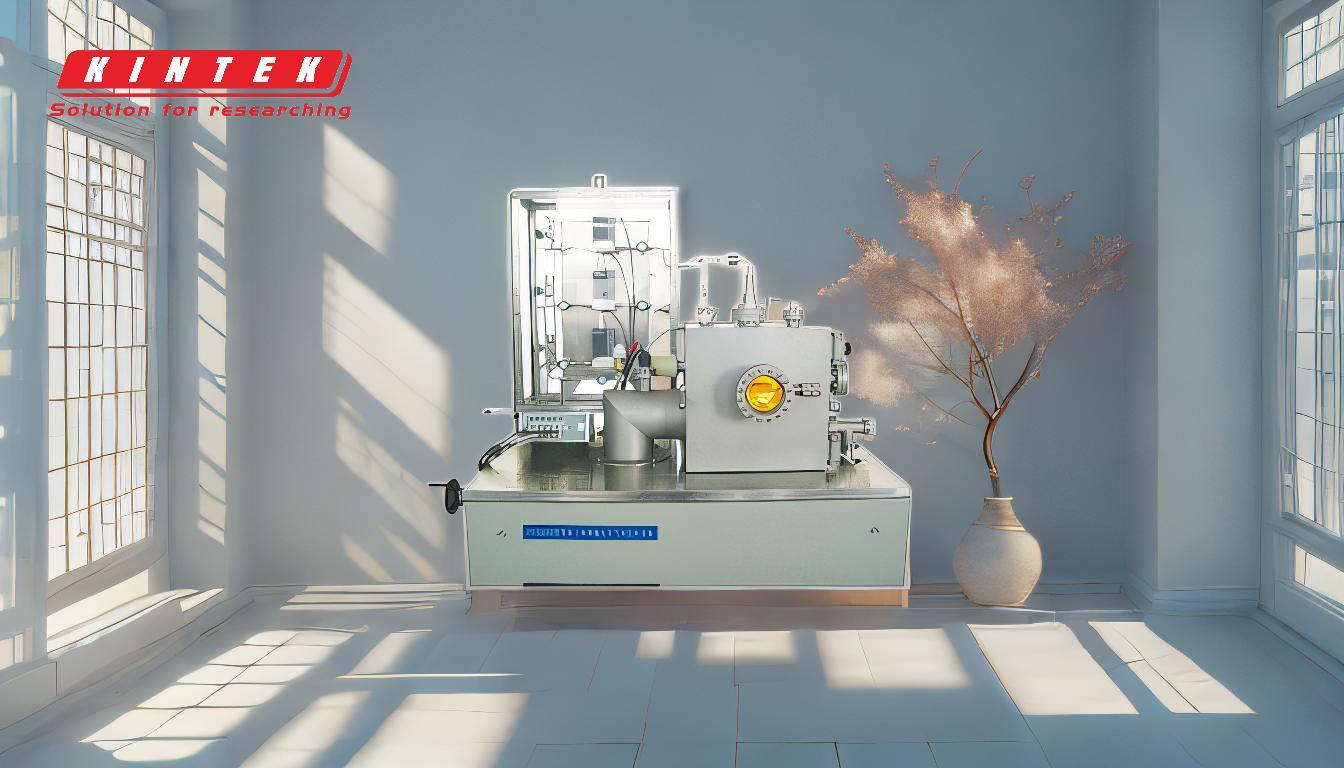
-
Plasma Creation and Ionization:
- A noble gas, typically argon, is introduced into a vacuum chamber.
- The gas is ionized using a high voltage or electromagnetic excitation, creating a plasma composed of positively charged argon ions (Ar+).
- This plasma is essential for generating the high-energy ions needed to sputter atoms from the target material.
-
Vacuum Environment:
- The process begins by evacuating the chamber to a low pressure (around 1 Pa or 0.0000145 psi) to remove moisture and impurities.
- A vacuum ensures minimal contamination and allows for precise control over the deposition process.
-
Target Bombardment:
- The positively charged argon ions are accelerated toward the target material, which is typically a solid metal or compound.
- Upon impact, the ions transfer their energy to the target, ejecting atoms from its surface in a process known as sputtering.
-
Magnetic Field Confinement:
- A magnetic field is often used to confine the plasma and increase the efficiency of the sputtering process.
- This magnetic field helps direct the ions toward the target, ensuring a higher rate of atom ejection.
-
Transport of Sputtered Atoms:
- The ejected atoms travel through the vacuum chamber and deposit onto the substrate.
- The low-pressure environment ensures that the atoms travel ballistically, minimizing collisions and ensuring a uniform deposition.
-
Film Formation:
- The sputtered atoms condense on the substrate, forming a thin film.
- The film grows layer by layer, with the thickness and properties of the film controlled by the duration of the sputtering process and the energy of the ions.
-
Process Parameters:
- Pressure: The chamber pressure is carefully controlled, typically in the range of 10^-1 to 10^-3 mbar, to optimize the sputtering process.
- Temperature: The substrate may be heated to temperatures ranging from 150°C to 750°C, depending on the material being deposited.
- Voltage: A high voltage (3-5 kV) is applied to ionize the argon gas and accelerate the ions toward the target.
-
Applications:
- Sputtering is used in a wide range of applications, including the deposition of thin films for semiconductors, optical coatings, and protective layers.
- It is also used in the production of reflective coatings, solar cells, and decorative finishes.
-
Historical Context:
- The sputtering process has been used commercially since the early 20th century, with Thomas Edison being one of the first to apply it for mass-duplication of phonograph recordings.
- Variations of sputtering, such as anodizing, are used to create uniform and durable surfaces on materials like aluminum.
-
Advantages:
- Precision: The process allows for precise control over film thickness and composition.
- Uniformity: Sputtering produces highly uniform films, even on complex geometries.
- Versatility: A wide range of materials, including metals, alloys, and compounds, can be deposited using sputtering.
In summary, the sputtering process is a versatile and highly controllable method for depositing thin films. It involves creating a plasma, bombarding a target material with high-energy ions, and depositing the ejected atoms onto a substrate. The process is widely used in various industries due to its ability to produce uniform, high-quality films with precise control over their properties.
Summary Table:
Key Aspect | Details |
---|---|
Plasma Creation | Noble gas (e.g., argon) ionized to form plasma for high-energy ion generation. |
Vacuum Environment | Chamber evacuated to ~1 Pa to ensure minimal contamination. |
Target Bombardment | Argon ions eject atoms from a solid target material. |
Magnetic Field | Confines plasma, increasing sputtering efficiency. |
Film Formation | Sputtered atoms condense on a substrate, forming a uniform thin film. |
Applications | Semiconductors, optical coatings, solar cells, and decorative finishes. |
Advantages | Precision, uniformity, and versatility in material deposition. |
Interested in leveraging sputtering for your projects? Contact us today to learn more!