Sputtering deposition is a widely used physical vapor deposition (PVD) technique for creating thin films on substrates. It involves bombarding a solid target material with high-energy ions, typically from an inert gas like argon, in a vacuum chamber. The bombardment ejects atoms from the target, which then travel through the vacuum and deposit onto a substrate, forming a thin, uniform coating. This process is highly controllable and versatile, making it suitable for applications in semiconductors, optics, and coatings. The system typically includes a vacuum chamber, a target material, a substrate holder, and a power supply to generate the plasma.
Key Points Explained:
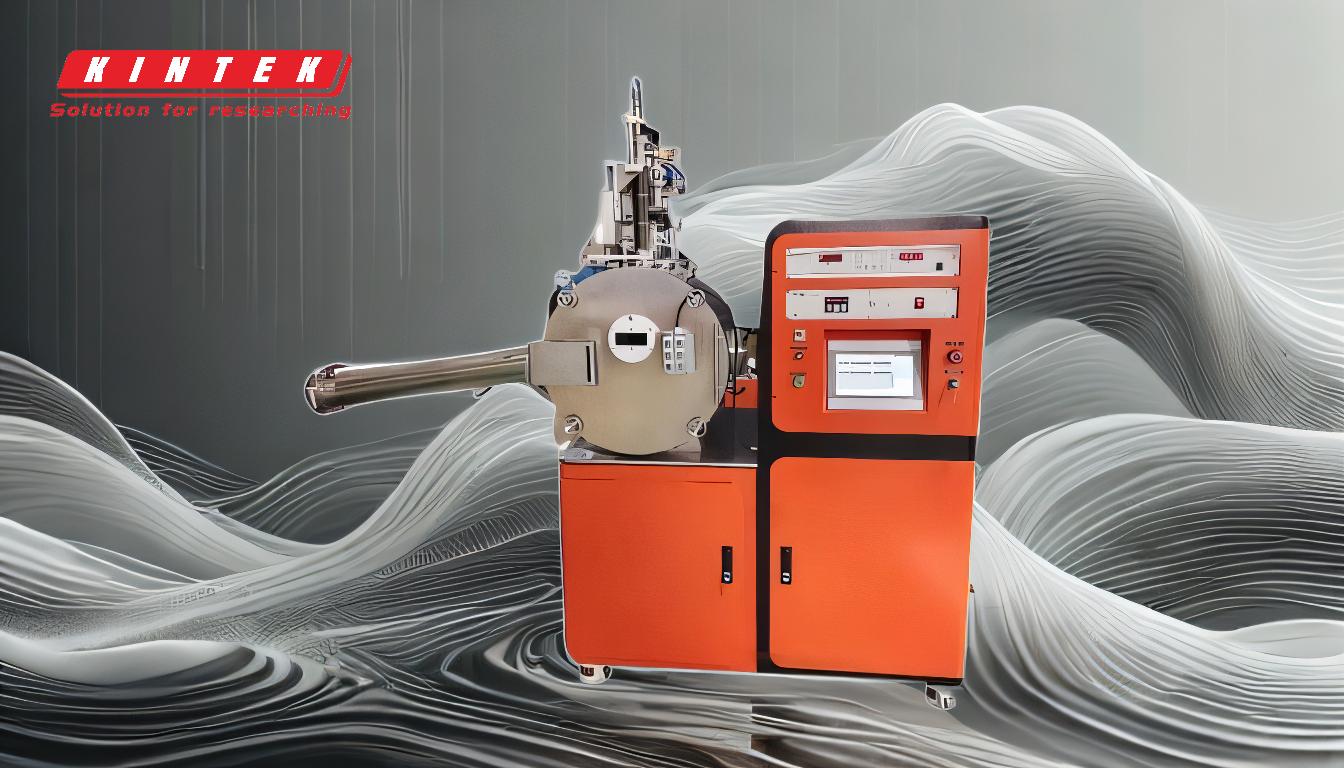
-
Basic Principle of Sputtering Deposition:
- Sputtering deposition is a PVD method where atoms are ejected from a solid target material due to bombardment by high-energy ions.
- The ejected atoms travel through a vacuum and deposit onto a substrate, forming a thin film.
- This process is driven by plasma, often created using inert gases like argon.
-
Components of a Sputtering System:
- Vacuum Chamber: Maintains a low-pressure environment to ensure the sputtered atoms travel unimpeded to the substrate.
- Target Material: The source material that is bombarded by ions. It is typically connected to a negatively charged cathode.
- Substrate Holder: Holds the substrate onto which the thin film is deposited. It is usually connected to a positively charged anode.
- Power Supply: Generates the electrical potential needed to create and sustain the plasma.
- Inert Gas Source: Supplies the gas (e.g., argon) used to create the plasma.
-
Process Steps:
- Vacuum Creation: The chamber is evacuated to a high vacuum to minimize contamination.
- Gas Introduction: Inert gas (e.g., argon) is introduced into the chamber.
- Plasma Formation: A high-voltage power supply ionizes the gas, creating a plasma of positively charged ions and free electrons.
- Ion Bombardment: The ions are accelerated toward the negatively charged target, ejecting atoms from its surface.
- Deposition: The ejected atoms travel through the vacuum and deposit onto the substrate, forming a thin film.
-
Advantages of Sputtering Deposition:
- Uniformity: Produces highly uniform thin films, even on complex geometries.
- Versatility: Can deposit a wide range of materials, including metals, alloys, and ceramics.
- Control: Allows precise control over film thickness and composition.
- Adhesion: Results in strong adhesion between the film and substrate.
-
Applications:
- Semiconductors: Used to deposit thin films in the fabrication of integrated circuits and solar cells.
- Optics: Creates reflective and anti-reflective coatings for lenses and mirrors.
- Coatings: Provides wear-resistant and decorative coatings for tools, jewelry, and automotive parts.
-
Considerations for Equipment Purchasers:
- Chamber Size: Ensure the chamber can accommodate the required substrate sizes.
- Target Material Compatibility: Verify the system supports the materials needed for your application.
- Power Supply: Choose a power supply that matches the required deposition rates and film quality.
- Gas Handling: Ensure the system can handle the specific gases and flow rates needed for your process.
- Automation: Consider systems with automation features for improved reproducibility and efficiency.
By understanding these key points, purchasers can make informed decisions when selecting a sputtering system for their specific needs.
Summary Table:
Key Aspect | Details |
---|---|
Basic Principle | Ejects atoms from a target using high-energy ions, forming a thin film. |
Main Components | Vacuum chamber, target material, substrate holder, power supply, gas source. |
Process Steps | Vacuum creation, gas introduction, plasma formation, ion bombardment, deposition. |
Advantages | Uniformity, versatility, precise control, strong adhesion. |
Applications | Semiconductors, optics, wear-resistant coatings. |
Purchasing Considerations | Chamber size, target material compatibility, power supply, gas handling, automation. |
Ready to enhance your thin film processes? Contact us today to find the perfect sputtering system for your needs!