Dental ceramics, often referred to as fine ceramics, are widely used in restorative dentistry due to their excellent biocompatibility, aesthetic properties, and mechanical strength. The strength of dental ceramics is a critical factor in their performance, as it determines their ability to withstand the forces exerted during chewing and other oral functions. The strength of these materials is influenced by their composition, microstructure, and processing techniques. Understanding the strength of dental ceramics is essential for selecting the right material for specific dental applications, ensuring durability and longevity of dental restorations.
Key Points Explained:
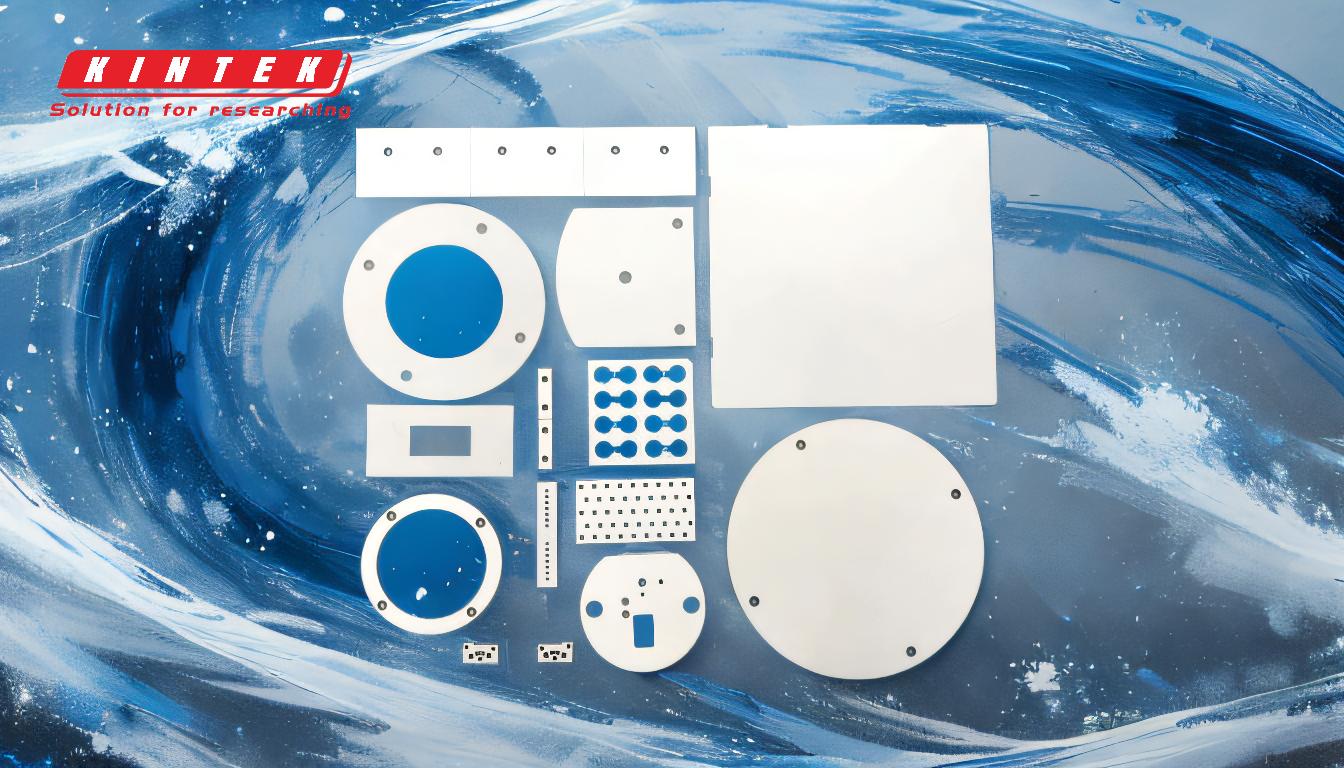
-
Composition and Types of Dental Ceramics:
- Dental ceramics are primarily composed of inorganic, non-metallic materials, often based on silica, alumina, and zirconia. These materials are categorized into different types based on their composition and processing methods:
- Feldspathic Porcelain: Known for its excellent aesthetic properties but relatively lower strength.
- Glass Ceramics: These include materials like lithium disilicate, which offer a balance between strength and aesthetics.
- Zirconia-Based Ceramics: These are known for their high strength and toughness, making them suitable for posterior restorations.
- The composition directly impacts the mechanical properties, including strength, fracture toughness, and wear resistance.
- Dental ceramics are primarily composed of inorganic, non-metallic materials, often based on silica, alumina, and zirconia. These materials are categorized into different types based on their composition and processing methods:
-
Mechanical Strength of Dental Ceramics:
- The strength of dental ceramics is typically measured in terms of flexural strength, which is the ability of the material to resist deformation under load. The flexural strength of dental ceramics can range from:
- Feldspathic Porcelain: 60-120 MPa.
- Lithium Disilicate: 300-400 MPa.
- Zirconia: 900-1200 MPa.
- These values indicate that zirconia-based ceramics are significantly stronger than other types, making them ideal for high-stress applications like crowns and bridges.
- The strength of dental ceramics is typically measured in terms of flexural strength, which is the ability of the material to resist deformation under load. The flexural strength of dental ceramics can range from:
-
Factors Influencing Strength:
- Microstructure: The size and distribution of crystalline phases within the ceramic material play a crucial role in determining its strength. Finer and more uniform microstructures generally result in higher strength.
- Processing Techniques: The method used to fabricate the ceramic, such as sintering, hot pressing, or CAD/CAM milling, affects its final strength. For example, zirconia ceramics are often sintered at high temperatures to achieve maximum density and strength.
- Surface Treatments: Techniques like polishing, glazing, or applying a veneer can influence the surface integrity and overall strength of the ceramic restoration.
-
Clinical Implications of Strength:
- The strength of dental ceramics is a critical factor in determining their suitability for different clinical applications:
- Anterior Restorations: Aesthetic considerations are often prioritized, and materials like feldspathic porcelain or lithium disilicate are commonly used.
- Posterior Restorations: Higher strength materials like zirconia are preferred due to the higher masticatory forces in the posterior region.
- Understanding the strength properties helps clinicians choose the appropriate material to ensure the longevity and functionality of the restoration.
- The strength of dental ceramics is a critical factor in determining their suitability for different clinical applications:
-
Challenges and Future Directions:
- Despite their high strength, dental ceramics are still prone to brittle fracture under certain conditions. Research is ongoing to develop new materials and processing techniques to enhance the toughness and reliability of dental ceramics.
- Advances in nanotechnology and composite materials are being explored to create ceramics with improved mechanical properties and reduced susceptibility to fracture.
In conclusion, the strength of dental ceramics is a multifaceted property influenced by composition, microstructure, and processing techniques. Fine ceramics, such as zirconia, offer exceptional strength and are increasingly used in demanding dental applications. However, ongoing research and development are essential to further improve the mechanical properties and clinical performance of these materials. For more detailed information on fine ceramics, you can refer to fine ceramics.
Summary Table:
Type of Dental Ceramic | Flexural Strength (MPa) | Key Characteristics |
---|---|---|
Feldspathic Porcelain | 60-120 | Excellent aesthetics, lower strength |
Lithium Disilicate | 300-400 | Balanced strength and aesthetics |
Zirconia-Based Ceramics | 900-1200 | High strength, ideal for posterior restorations |
Need help selecting the right dental ceramic for your practice? Contact our experts today for personalized guidance!