The synthesis of carbon nanotubes (CNTs) using the Chemical Vapor Deposition (CVD) process involves a series of thermal and chemical reactions that facilitate the growth of CNTs on a substrate. The process begins with the generation of a gaseous precursor in the source area, which is then transported to the growth area where it undergoes decomposition or reaction to form the desired material. In the context of CNT synthesis, the forward reaction involves the generation of carbon-containing gases, while the reverse reaction involves the deposition and growth of CNTs on a catalyst surface. This method is highly controllable and allows for the production of high-quality CNTs with specific properties.
Key Points Explained:
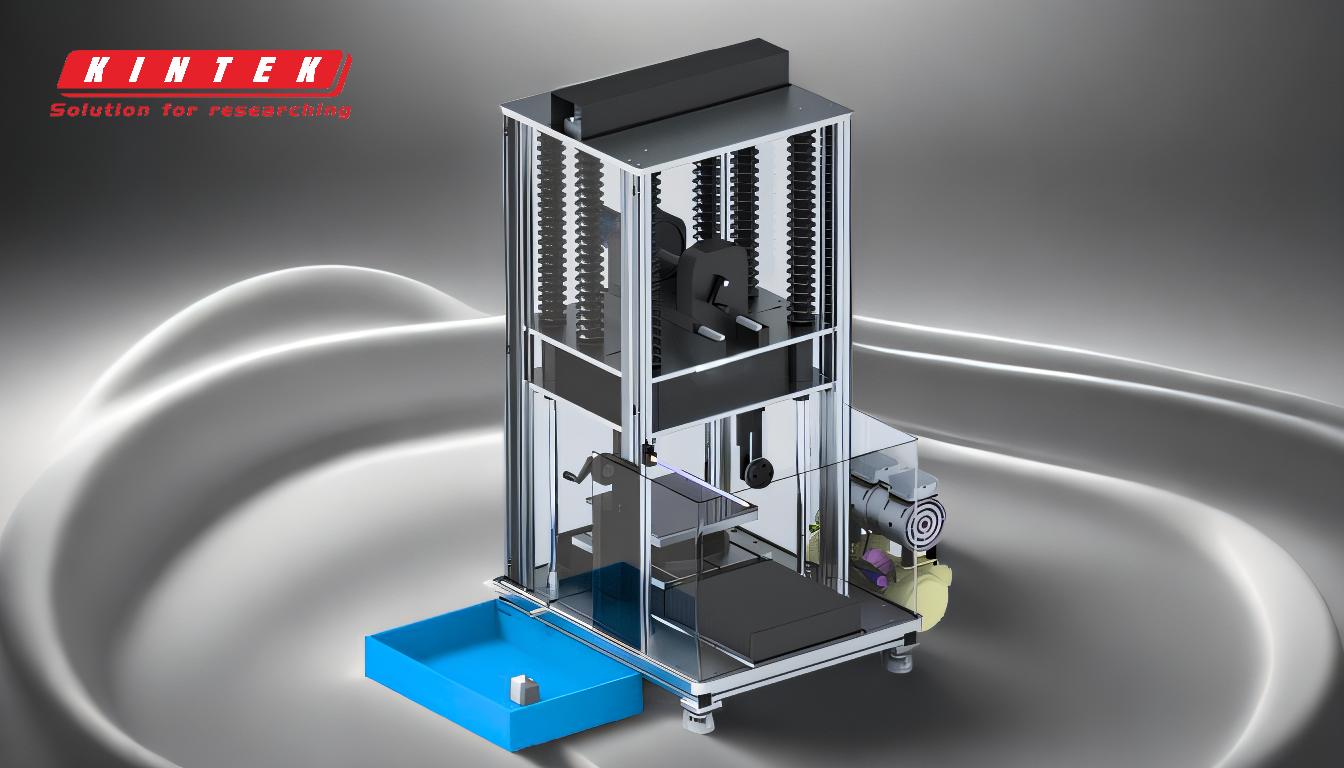
-
Generation of Gaseous Precursor:
- In the CVD process, a carbon-containing gas such as methane (CH₄), ethylene (C₂H₄), or acetylene (C₂H₂) is introduced into the reaction chamber.
- This gas reacts with a catalyst, typically a transition metal like iron, nickel, or cobalt, which is often deposited on a substrate.
-
Transport of Gas to Growth Area:
- The gaseous precursor is transported to the growth area, which is maintained at a high temperature (typically between 600°C to 1200°C).
- The high temperature facilitates the decomposition of the carbon-containing gas into carbon atoms and hydrogen.
-
Decomposition and Carbon Atom Release:
- At the elevated temperature, the carbon-containing gas decomposes, releasing carbon atoms.
- These carbon atoms then diffuse into the catalyst particles.
-
Nucleation and Growth of Carbon Nanotubes:
- The carbon atoms dissolved in the catalyst particles eventually reach supersaturation, leading to the nucleation of carbon nanotubes.
- The growth of CNTs occurs as carbon atoms continue to diffuse through the catalyst particle and precipitate at the interface between the catalyst and the growing nanotube.
-
Role of Catalyst:
- The catalyst plays a crucial role in the CVD process. It not only facilitates the decomposition of the carbon-containing gas but also acts as a template for the growth of CNTs.
- The size and type of the catalyst particles determine the diameter and structure (single-walled or multi-walled) of the resulting CNTs.
-
Thermodynamic and Kinetic Considerations:
- The forward reaction (generation of carbon-containing gas) and the reverse reaction (deposition and growth of CNTs) are governed by thermodynamic and kinetic factors.
- The temperature, pressure, and gas flow rates are carefully controlled to optimize the growth conditions and ensure the formation of high-quality CNTs.
-
Control of CNT Properties:
- The properties of the CNTs, such as their length, diameter, and chirality, can be controlled by adjusting the process parameters, including the type of catalyst, the temperature, and the composition of the gas mixture.
- This level of control makes the CVD process highly versatile for producing CNTs with tailored properties for specific applications.
-
Applications of CVD-Grown CNTs:
- CNTs synthesized via the CVD process are used in a wide range of applications, including electronics, composites, energy storage, and biomedical devices.
- The ability to produce CNTs with specific properties makes them particularly valuable in advanced materials and nanotechnology.
In summary, the CVD process for synthesizing carbon nanotubes involves a complex interplay of chemical reactions, transport phenomena, and catalytic processes. The careful control of these factors allows for the production of high-quality CNTs with tailored properties, making the CVD method a cornerstone of modern nanotechnology.
Summary Table:
Step | Description |
---|---|
Generation of Gaseous Precursor | Carbon-containing gases like methane (CH₄) are introduced into the reaction chamber. |
Transport to Growth Area | Gases are transported to a high-temperature growth area (600°C–1200°C) for decomposition. |
Decomposition and Carbon Release | Carbon-containing gases decompose, releasing carbon atoms that diffuse into catalyst particles. |
Nucleation and Growth | Carbon atoms reach supersaturation, nucleating and growing CNTs on the catalyst surface. |
Role of Catalyst | Catalyst (e.g., iron, nickel) facilitates gas decomposition and templates CNT growth. |
Control of CNT Properties | Adjusting temperature, pressure, and gas flow tailors CNT length, diameter, and chirality. |
Applications | CVD-grown CNTs are used in electronics, composites, energy storage, and biomedical devices. |
Discover how the CVD process can revolutionize your nanotechnology applications—contact our experts today!